History
1944・December
In December 1944, Nishio Seiki Co., Ltd., changed its name to Taiho Kogyo Co., Ltd., and relocated its business plant to its current site near the head office of Toyota Motor Corporation. In December 1944, Nishio Seiki Co., Ltd., changed its name to Taiho Kogyo Co., Ltd., and relocated its business plant to its current site near the head office of Toyota Motor Corporation.
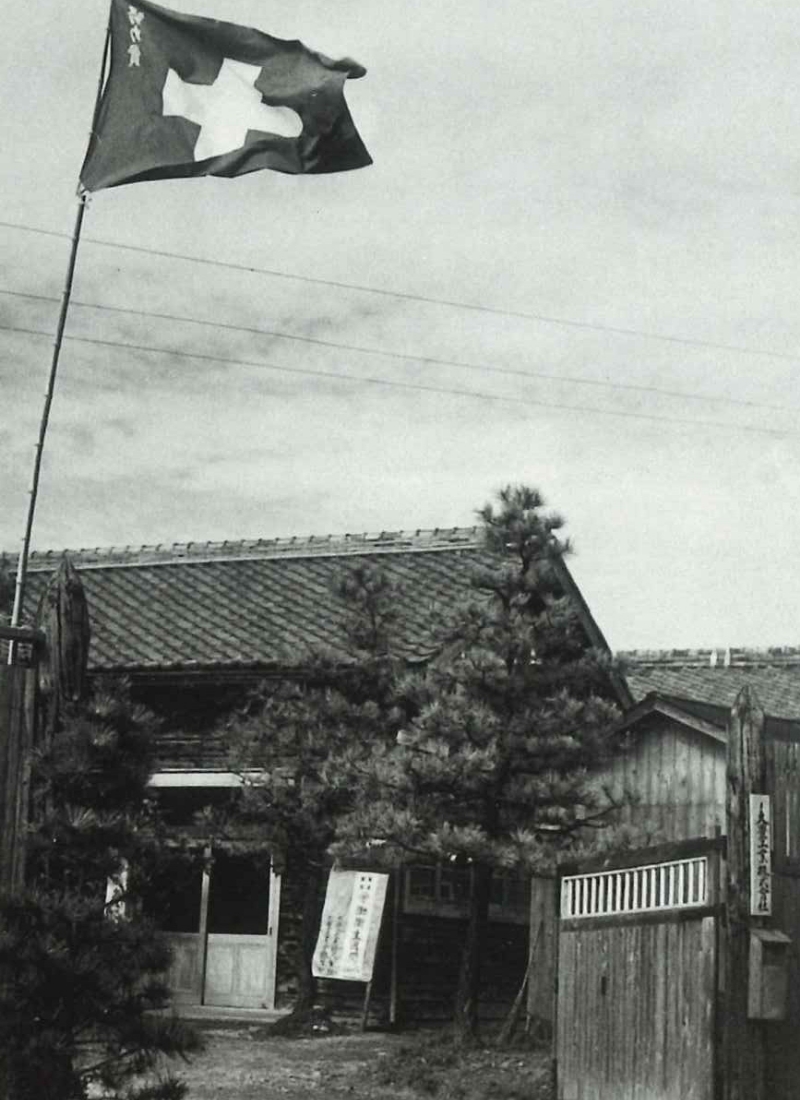
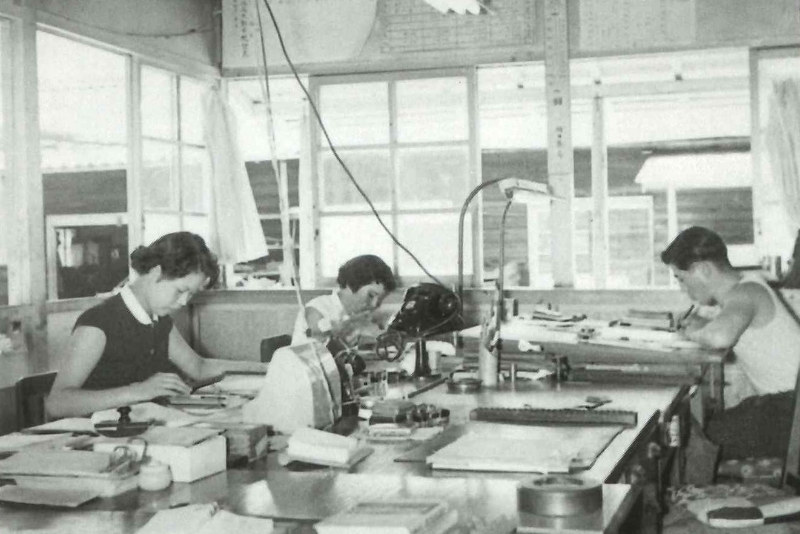
1946・Production of automotive bushings begins
In 1946, when the automotive industry first began to show signs of recovery, we received a request to machine bronze bushings from Toyota Motor Corporation. This request cast an illuminating light on our company at the time when we were little more than a mere small-town factory. However, we lacked sufficient equipment and were given the necessary set of equipment for machining purposes by Toyota Motor Corporation.
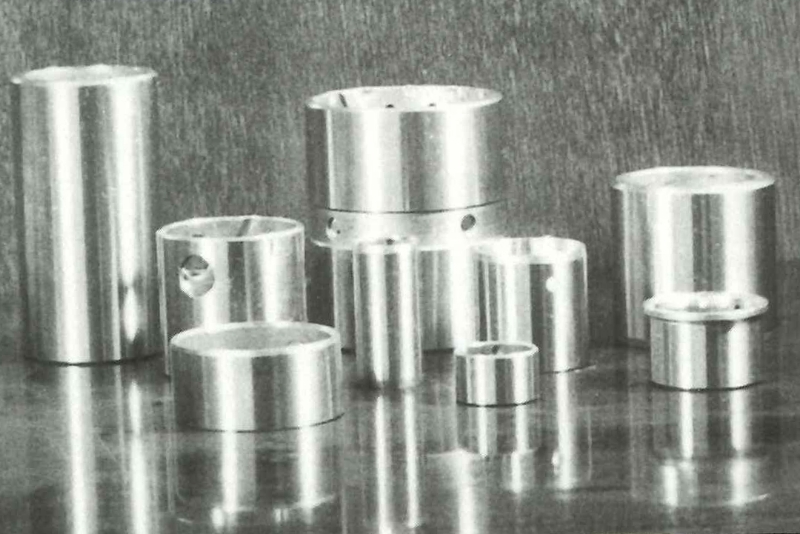
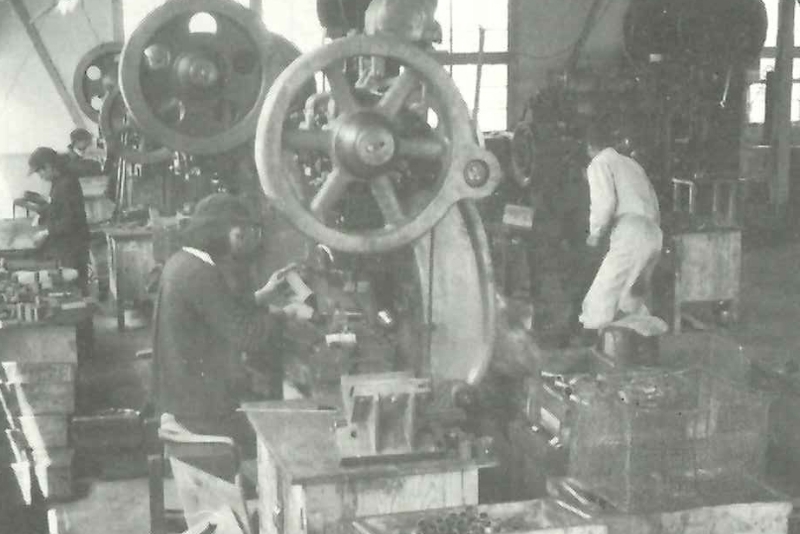
1958・Production of aluminum die-cast products begins
We added completely new products to the lineup on the heel of automotive bushings. This was a time when aluminum alloys first appeared as a new metal material for use in motorcycle wheel hubs and other applications. Manufacturers were eagerly declaring that the future belonged to aluminum die-casting. In the midst of this trend, we began to produce aluminum die-cast products. Our integrated approach to production, which encompassed everything up to and including the casting, machining, and painting steps, was rare at the time and drew the attention of related industrial sectors.
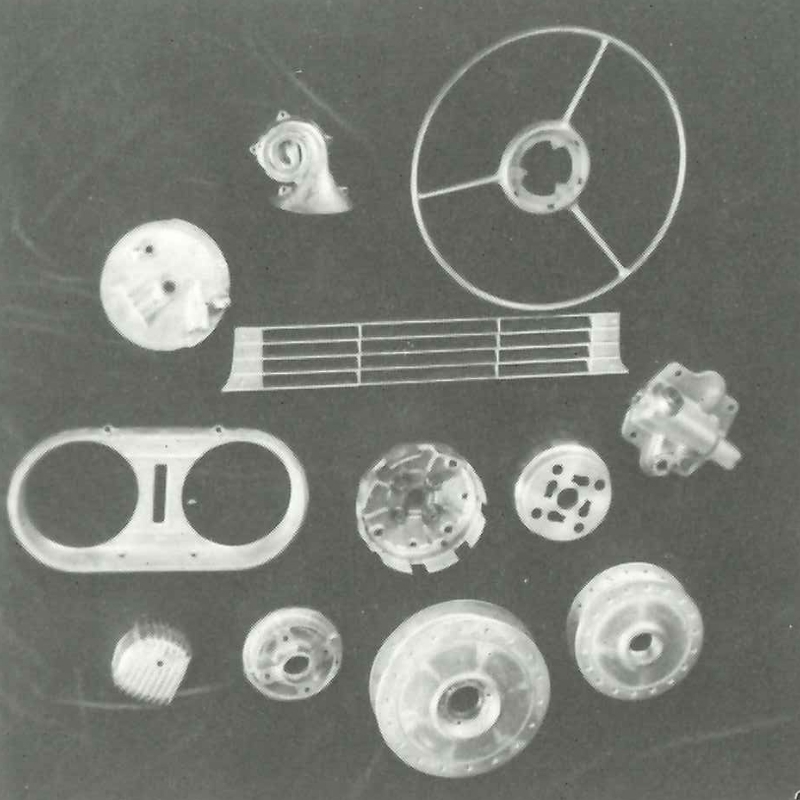
1961・Production of slide bearings for engines begins
It came to pass that we would begin to produce slide bearings for engines thanks to orders placed by Toyota Motor Corporation. In order to manufacture slide bearings for engines, a task requiring a more advanced level of expertise than other types of slide bearings, we received technical guidance from Toyota Motor Corporation and concluded a technical tie-up with FM to gain access to world-class technology. These slide bearings were incorporated into a wide range of vehicular models, including the Crown and New Corona nameplates of the time as well as trucks.
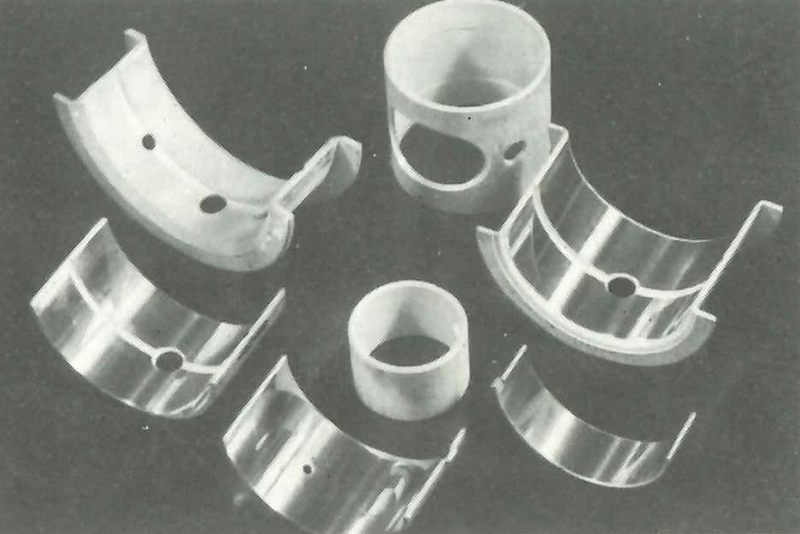
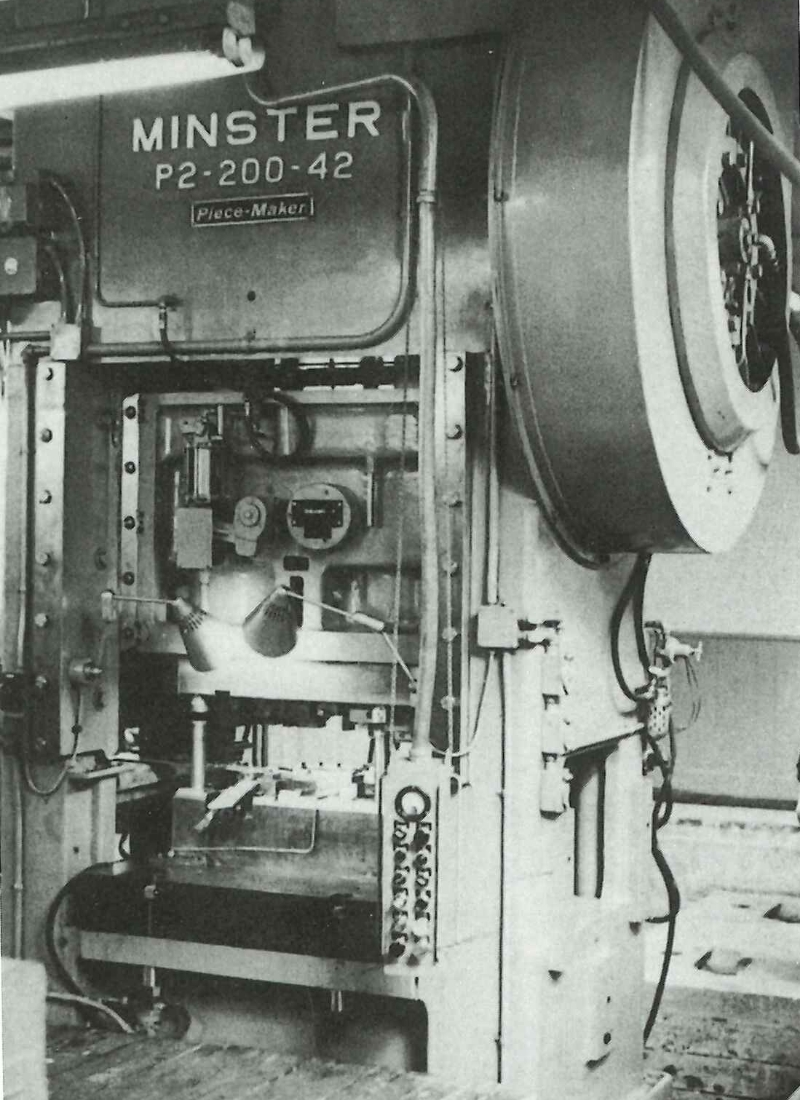
1965・Entering the supply parts market on a full-scale basis
1969・Hosoya Plant completed
1972・Production of aluminum alloy bearings begins
We began producing aluminum alloy bearings as a type of bearing material that could help lower costs. We devised proprietary equipment for the casting process to produce the alloy for the bearing material and for the drawing and metal rolling processes to produce sheets and put together an integrated production line ahead of our competitors.
1973・Taiho Livernois Automation Co., Ltd. established (Company name changed to Taiho Seiki Co., Ltd. in 1978)
1975・Production of EGR valves begins
We began developing and delivering an EGR valve for Toyota’s 20R engine. This was designed to reduce NOx emissions by returning exhaust gases to the combustion chamber for re-combustion at a time when demand was increasing in line with a tightening of exhaust gas controls. The EGR valve, which was developed by applying technology to secure the area around bearings, was adopted for all engines produced by Toyota Motor Corporation to comply with regulations enacted in 1975.
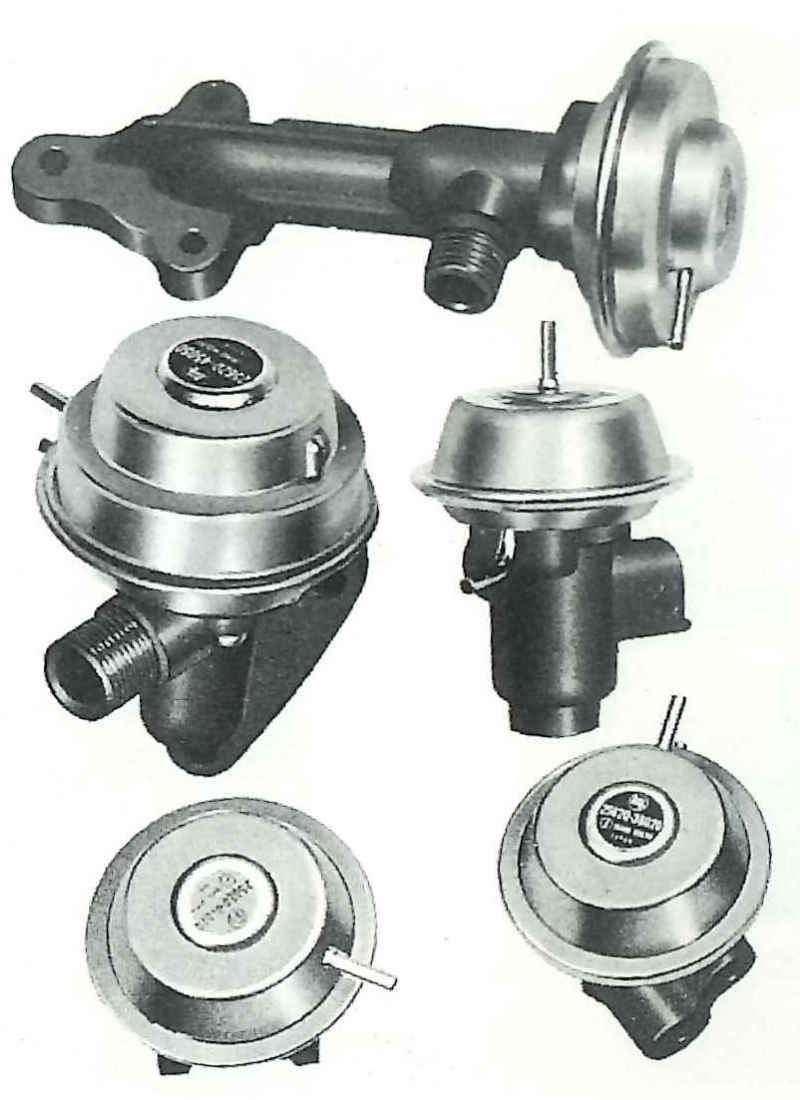
1978・Production of shoes for automobile air-conditioning systems begins
Our special bearings for car air-conditioning systems (shoes) drew the attention of American automobile manufacturers since they were highly wear-resistant and helped to reduce the size and weight of compressors.
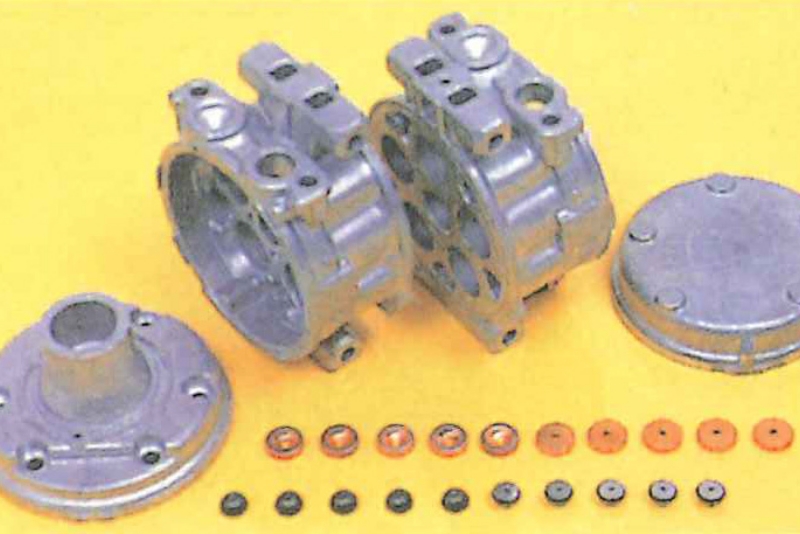
1978・Toyota Quality Control Award received
1980・Shoes for automobile air-conditioning systems are exported to Chrysler and Ford
1981・U.S. subsidiary Taiho Corporation of America (TCA) established
We set up a representative office in the United States in 1972 to expand our sales channels. Based on the track record that we had built up through this endeavor, we established Taiho Corporation of America (TCA) on the outskirts of Chicago in 1981. At the time, we focused on selling directly to Ford and Chrysler, which allowed us to provide services on a more tight-knit basis.
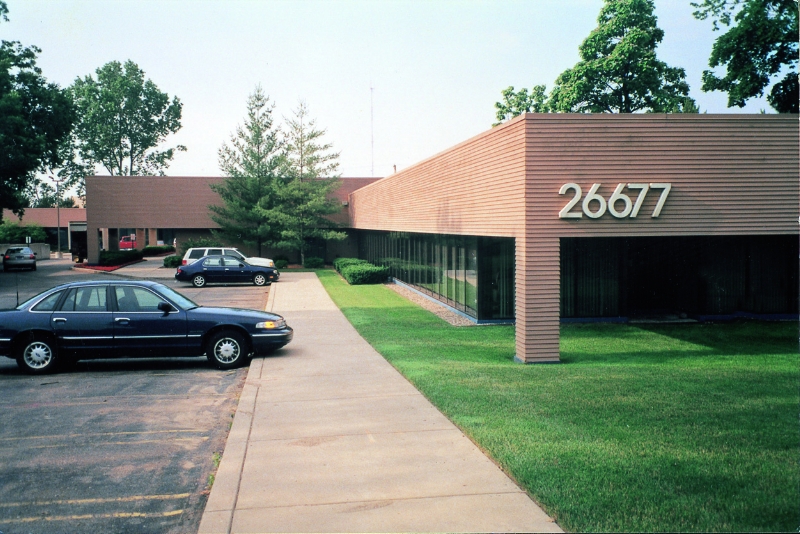
1984・Production of Turbocharger parts begins
1985・Sasahara Plant completed
We constructed our third plant, the Sasahara Plant, in the Green Technopia Industrial Park in the Sasahara district of Toyota City with the aim of increasing industrial capacity and entering new sectors. We began to take on the challenges posed by new areas, which primarily consisted of the manufacturing of precision dies, special bearings, and ultra-precision parts.
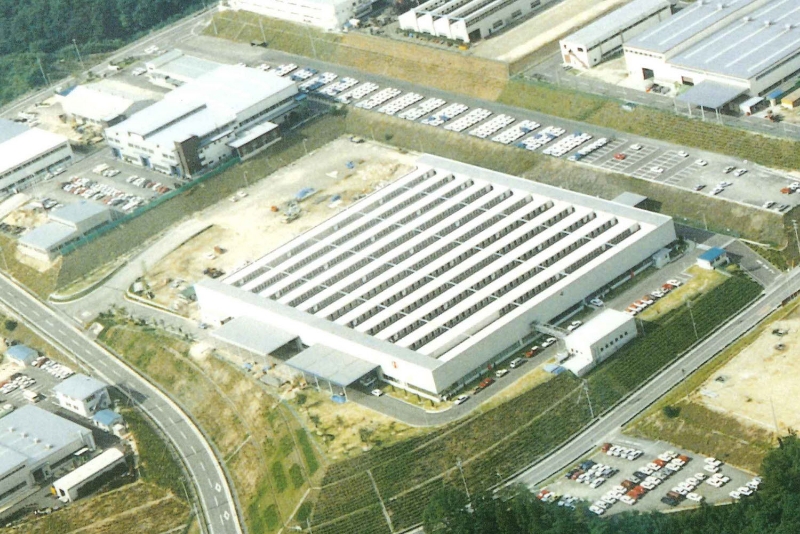
1985・Production of Precision Dies begins
1986・Ford Q1 Award received
1988・Production of resin products begins
We developed an intake air connector made of integrally molded resin that weighed 50% less, was quieter by 2 dB, and lowered costs by reducing the machining processes that needed to be undertaken. For us, this marked the birth of the first-ever resin product that we developed on our own. he resin molding of intake air connectors that consisted of multiple parts was difficult, but we dared to take on this challenge and succeeded in mass-producing this product. This became the driving force behind the subsequent development of other resin products.
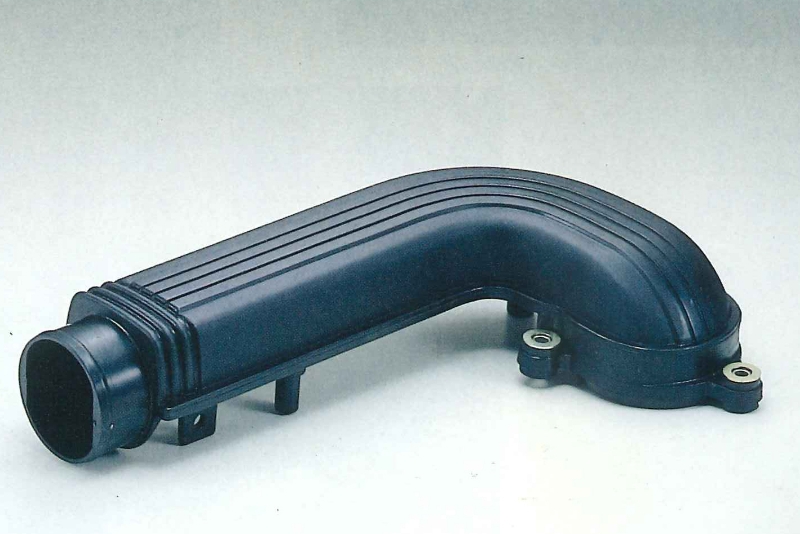
1989・Micro-group bearings (MGB) are adopted by Lexus
1989・Production of Metal Gaskets begins
1991・Kyushu Plant completed
The Kyushu Plant, our fourth plant, was built in Izumi City, Kagoshima Prefecture. Our high-mix, low-volume production line for bearings for the overseas supply market was relocated from the Hosoya Plant to this location, which began operations as an overseas strategic production base.
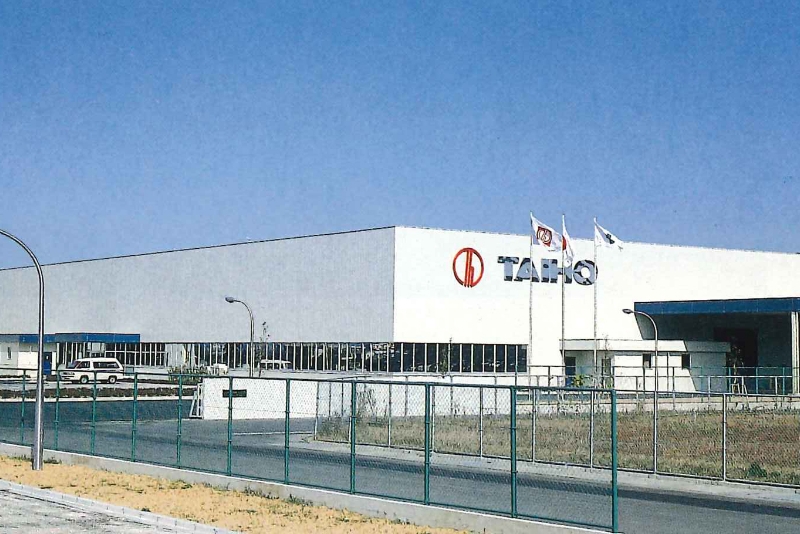
1993・PM operation site excellence Award received
1996・TCA Plant completed in the United States
The TCA Plant, our first-ever overseas production base, was completed in Tiffin, Ohio, in the United States. In June of that year, our first shipment of special bearings (shoes) produced for Ford was made. This event was also covered by the local newspaper. This marked a new beginning amid significant expectations from the local community.
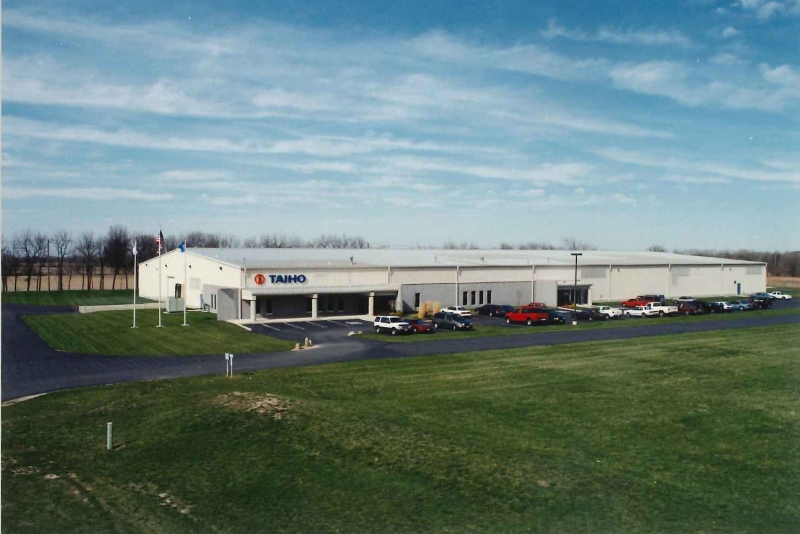
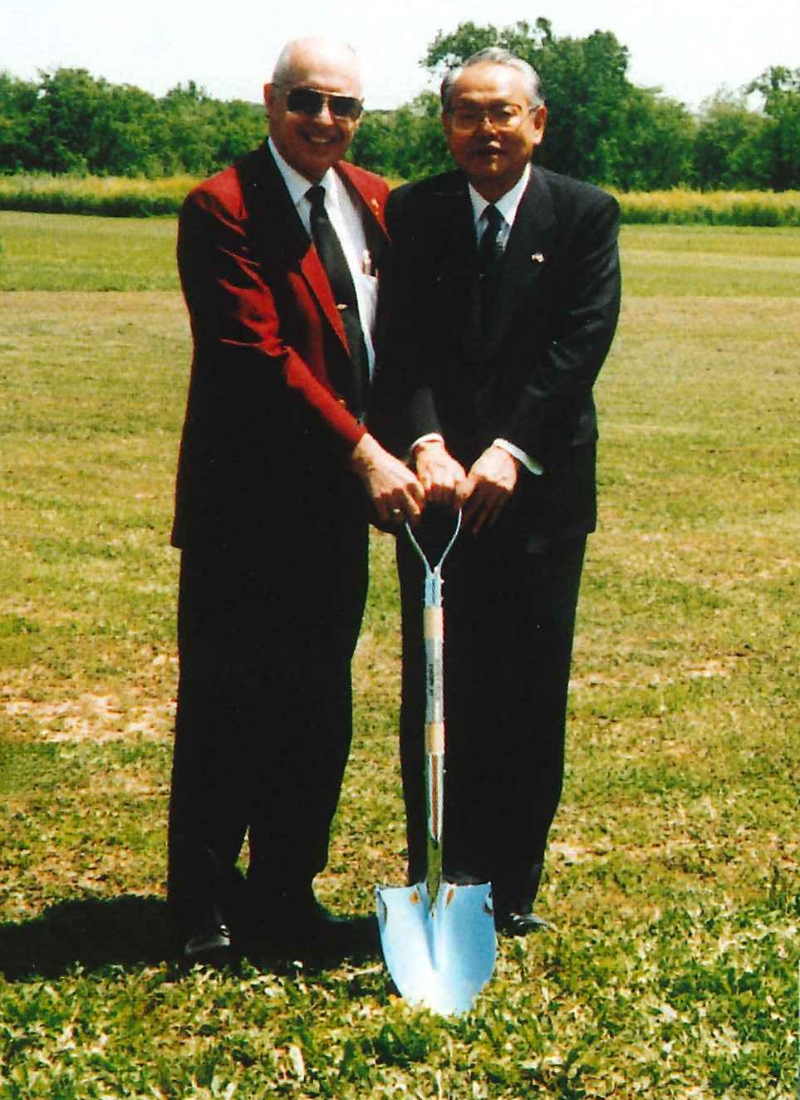
11996・Taiho Kogyo awarded QS-9000 certification
1997・Micro Grooved Bearing received the Tribology Society Technology Award
1998・Pt. Taiho Nusantara established in Indonesia
Pt. Taiho Nusantara (PTN) was established in Jakarta, Indonesia. PTN was our first full-scale production and sales base in Asia and its construction meant that we had managed to gain a solid foothold in three global regions: Japan, the United States, and Asia.
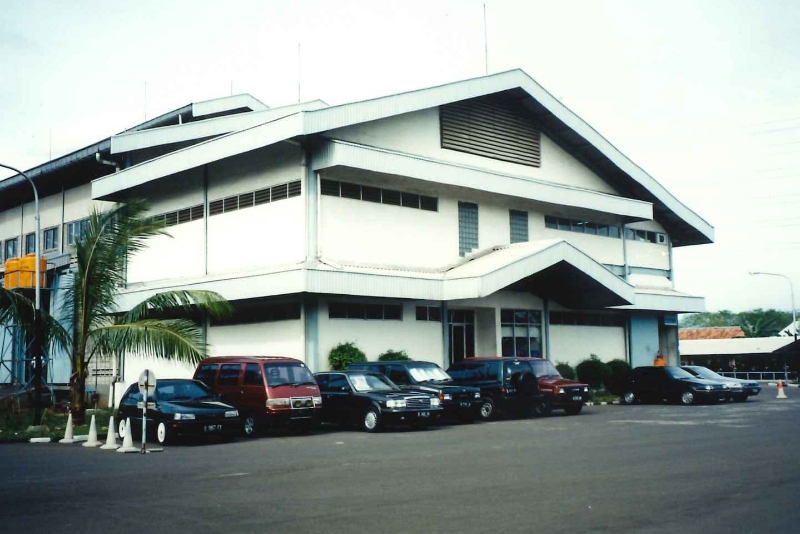
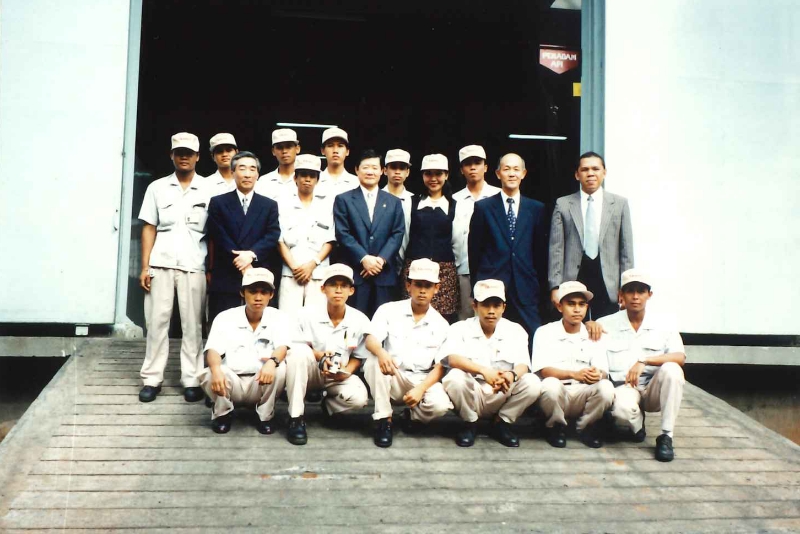
1999・Listed on the Second Section of the Nagoya Stock Exchange
1999・Obtained ISO14001 certification
2000・Listed on the Second Section of the Tokyo Stock Exchange
2000・Taiho Corporation of Europe (TCE) established
Taiho Corporation of Europe was established on the outskirts of Budapest, the capital of Hungary. Local production of primarily special bearings (shoes) was commenced. In this way, we managed to set up four regional bases worldwide in order to expand proactive transactions with automobile and parts manufacturers around the world.
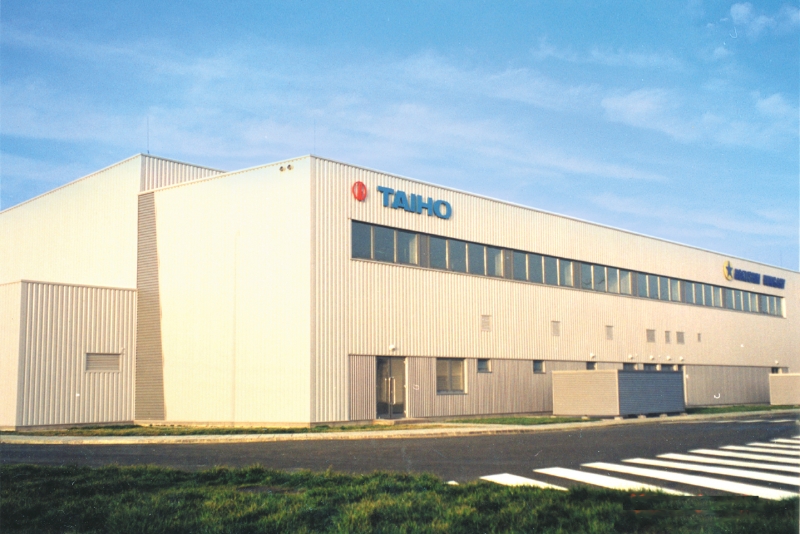
2000・Kokai Plant completed
The Kokai Plant, our fifth domestic plan, was completed in Kokai, Toyota City. At this plant, we mainly produce bearing materials and utilize a newly developed high-frequency sintering technology in the production system. This plant has emerged as a base for the production of materials for high-contact pressure and lead-free bearings. In 2003, we built a second plant in Kokai.
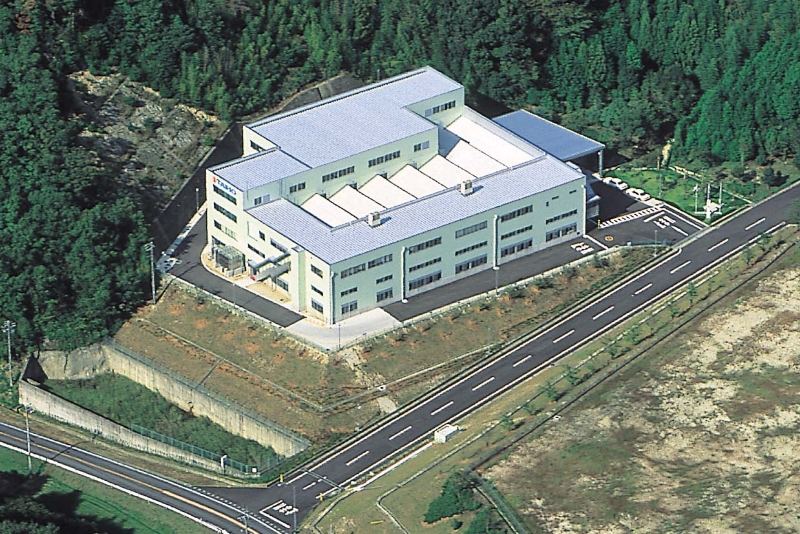
2001・Listed on the First Section of the Tokyo Stock Exchange and Nagoya Stock Exchange
We succeeded in becoming listed on the First Section of the Tokyo Stock Exchange and Nagoya Stock Exchange. In order to increase our corporate value in the stock market, we took new steps forward by working to develop proprietary technology, strengthen our international competitiveness, and improve our financing capabilities and gaining renewed awareness of our corporate responsibilities in such terms as compliance and environmental conservation.
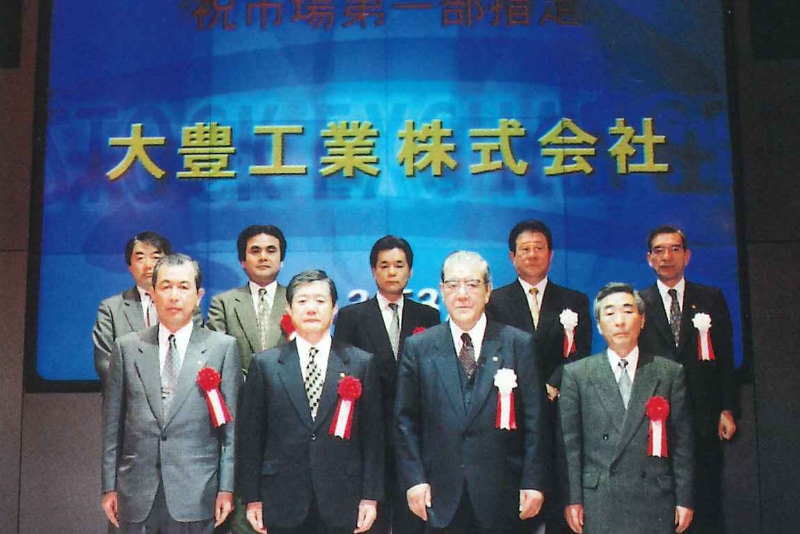
2001・Taiho Corporation of Korea (TCK) established
Taiho Corporation of Korea (TCK) was established in Daegu, South Korea. At this location, we expanded the local production and sales of compressor parts to accommodate the shift to local procurement in South Korea. TCK would subsequently increase the number of products it produces and expand its role as an important production and sales base in Asia.
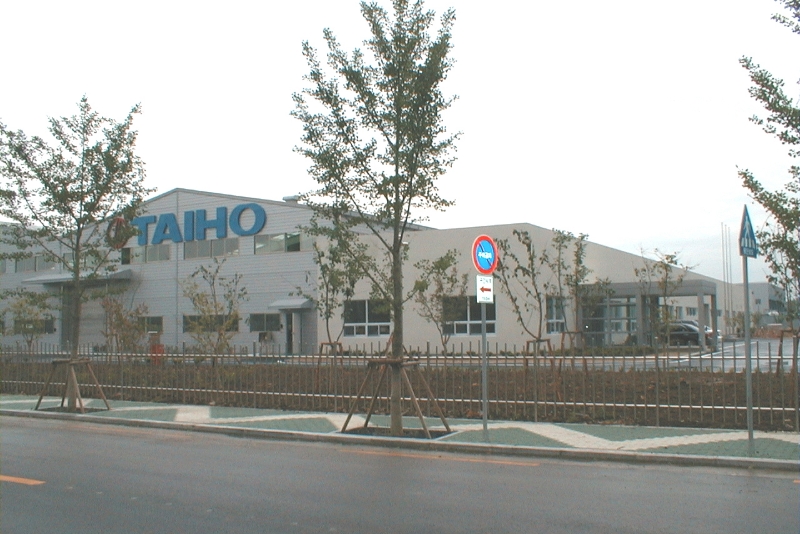
2002・TFGG, a joint venture with FM, established
2003・Taiho Kogyo Corporation of Yantai (TCY) takes over a Chinese manufacturer of bearings
Yantai Chunsang Sliding Bearing Co., Ltd., a Chinese manufacturer of bearings that we purchased in 2002, was taken over by Taiho Kogyo Corporation of Yantai (TCY). We introduced our latest equipment to build an integrated production system encompassing everything from materials to machining in hopes of making this company the leading manufacturer of bearings in China.
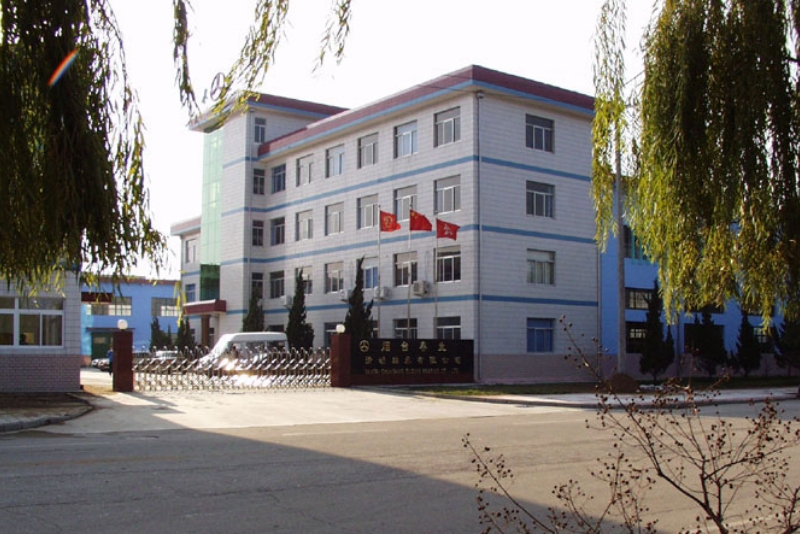
2003・Taiho Corporation of Thailand (TCT) established
Taiho Corporation of Thailand (TCT) was established as our second production base in the ASEAN region in order to meet production and supply needs in Thailand. This company primarily produces turbo parts, washers, and bushes. In 2014, a new plant was completed, and the production of vacuum pumps began.
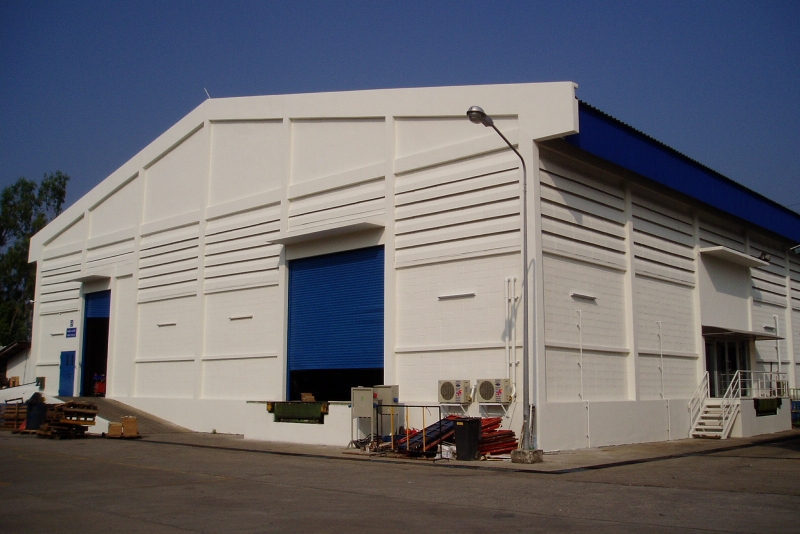
2003・Concluded an operational tie-up with Nippon Gasket
2004・Obtained ISO/TS16949 certification
2004・Taiho Kogyo awarded ISO/TS16949 certification
2005・Taiho Gifu Co., Ltd. (now the Gifu Plant) established
Taiho Gifu Co., Ltd., was established in the town of Mitake, Gifu Prefecture, in an effort to expand the production of slide bearings for engines, die-cast products, and system products. To this end, a third plant was built between 2005 and 2017. In 2019, this company was taken over by Taiho Kogyo in order to improve the efficiency of business operations and the site is currently operated as the Gifu Plant.
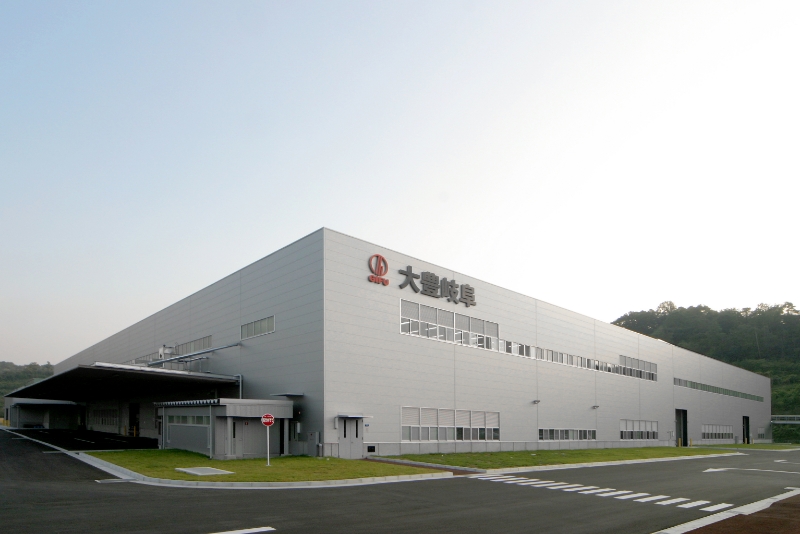
2005・Nippon Gasket made a wholly owned subsidiary
Nippon Gasket Co., Ltd., was made a wholly owned subsidiary for the purpose of consolidating our gasket business. Through this move, we integrated gasket development and production capabilities cultivated over time by Taiho Kogyo into Nippon Gasket in order to fortify our competitiveness as a more highly specialized and comprehensive gasket manufacturer.
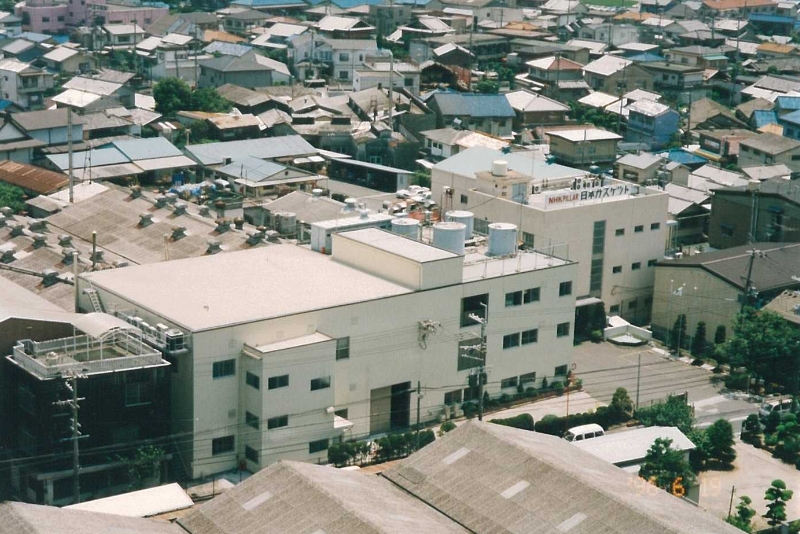
2007・Taiho Manufacturing of Tennessee (TTN) established
2007・Production of Vacuum Pump begins
2012・Hengye Bearing Materials Co., Ltd. (Changzhou) (WBM) acquired
We purchased Hengye Bearing Materials Co., Ltd. (Changzhou) (WBM), the largest manufacturer of aluminum bearing materials in China. By introducing the latest Japanese technology for manufacturing bearing materials, we will achieve an integrated production system encompassing everything from materials to machining in China. We have taken the first step to becoming a leading manufacturer of bearings in China.
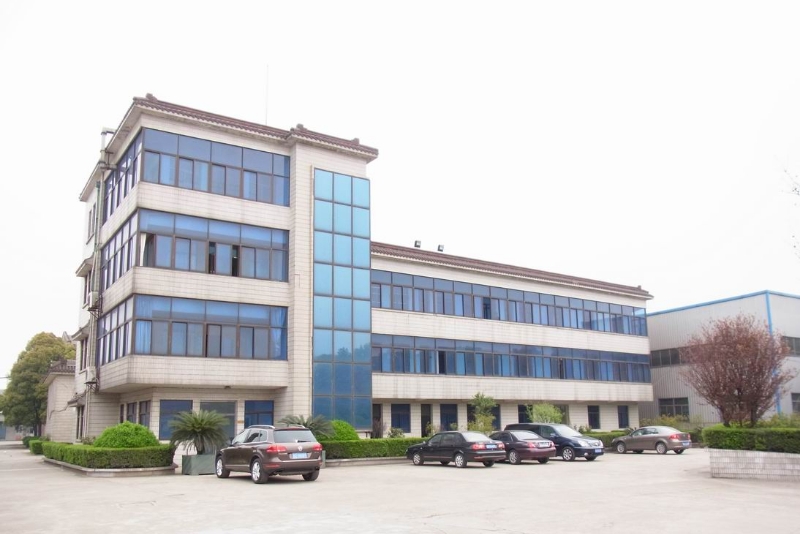
2014・The aluminum die-cast product pressure plate was adopted for the Toyota MIRAI
2015・Opened in-house day-care center T-Kids
In order to help our employees both work and raise children, we opened in-house day-care center T-Kids. This center is operated in line with days on which we operate as a company and can also take in children on holidays and other such days.
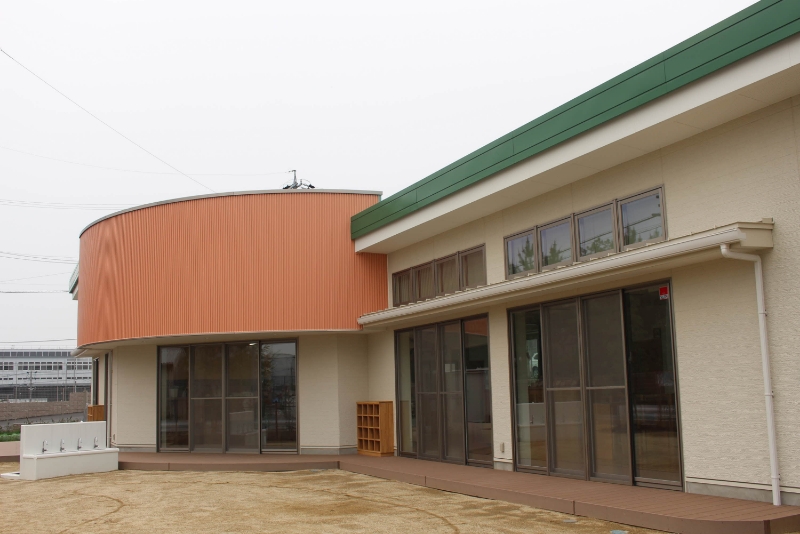
2019・Declaration of health management
We issued a declaration of health management in hopes of cultivating a workplace where each and every employee can continue to work with vitality. Each employee considers matters concerning his or her own health and undertakes measures to maintain and improve his or her own health on his or her own initiative.
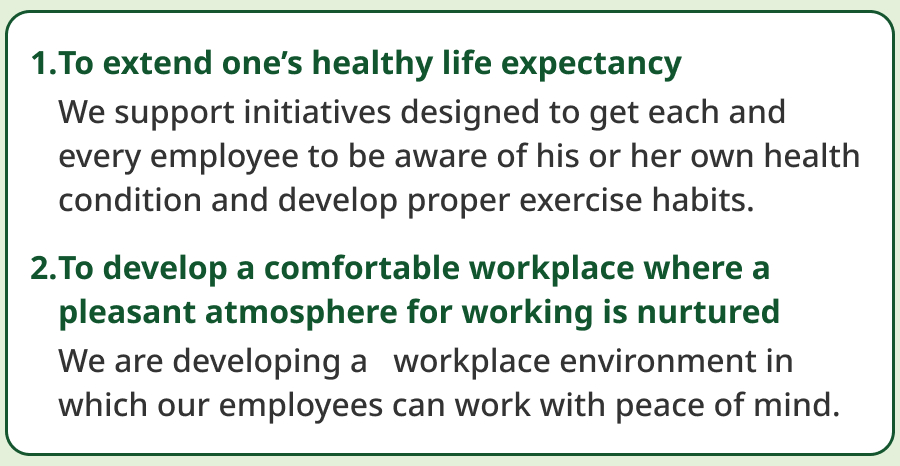