Optimization of the global production system
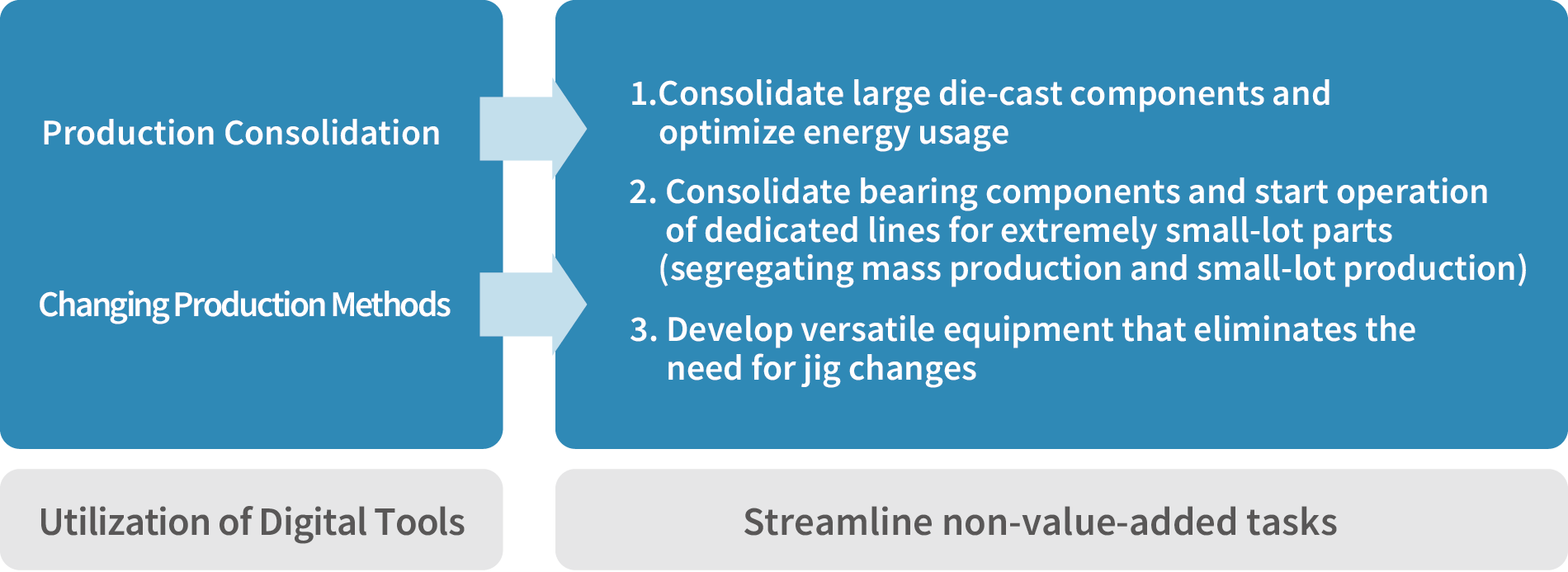
Production consolidation Improving energy efficiency of die-cast products
The production sites for die-cast products were previously divided between two domestic factories, with large parts and small parts being produced separately, leading to inefficient energy usage. To address this issue, we have consolidated the production of large parts at the Gifu factory, improving energy efficiency, enhancing productivity, and contributing to environmental sustainability.Additionally, the production of small parts at the head office factory has been transferred to affiliated companies to level the manufacturing load across the entire group, further boosting productivity.Changing production methods development and consolidation of versatile equipment for engine bearings
Engine bearings are produced both for mass production to automobile manufacturers and for small-lot production to the aftermarket, with production spread across three domestic factories. The mix of mass production and small-lot production caused long downtimes due to jig changes, leading to reduced productivity. To address this issue, we have developed a dedicated small-lot production line and consolidated small-lot production at the Kyushu factory, improving overall productivity.Quality improvement
- Through company-wide cross-functional activities, we share past defect cases to cultivate a strong sense of quality.
- Our quality improvement activities overseas have led to receiving quality awards from multiple customers.
Re-recognizing past cases
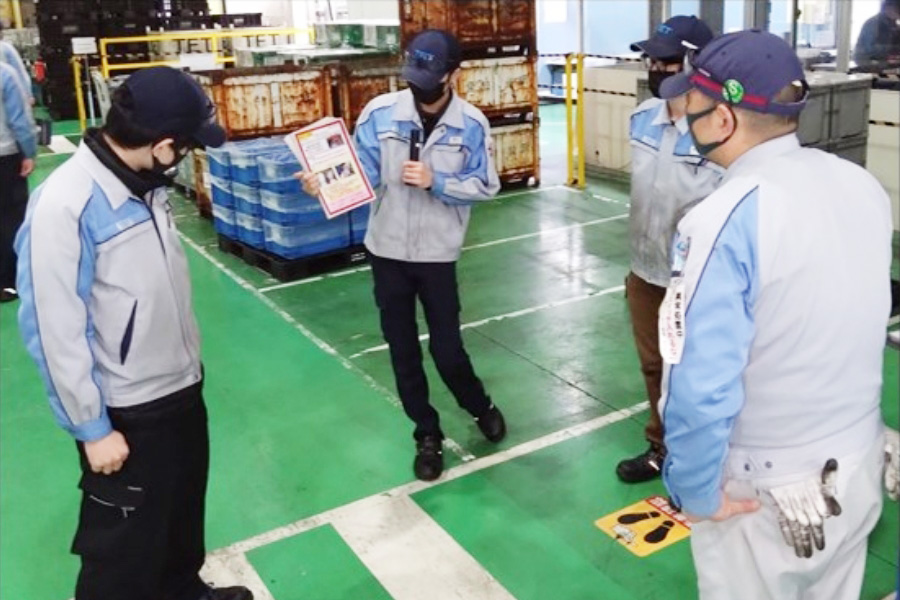
Integrated process inspection of manufacturing and quality
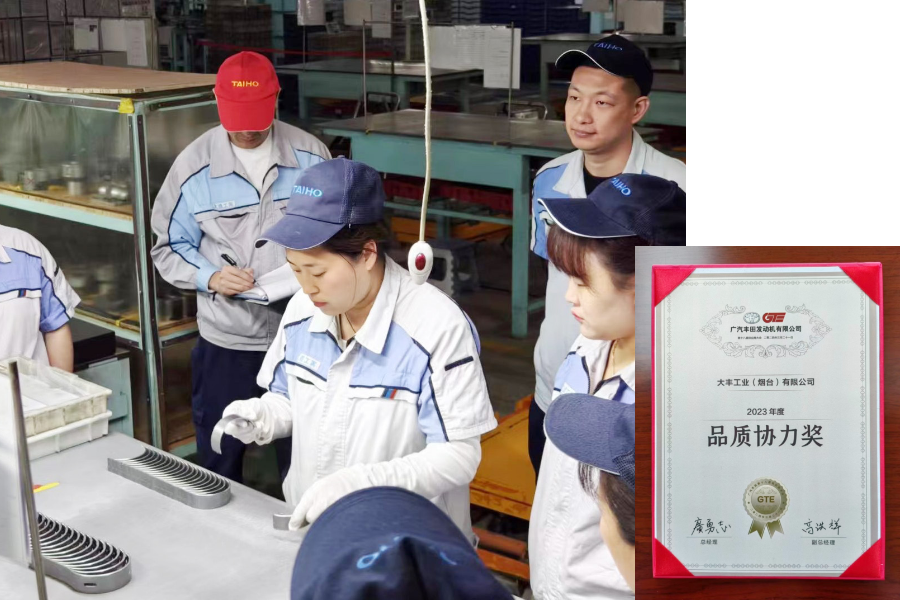