Development aims
To lower costs
- Downsizing of casting machines: 1,250t → 800t
- Weight reduction thanks to an optimal rib design

Downsizing of casting machines
Technology to reduce casting pressure
Die temperature control
Practical application of die surface treatment
CAE-based predictions of casting defects (product form and casting plan)
Increased sleeve filling rate
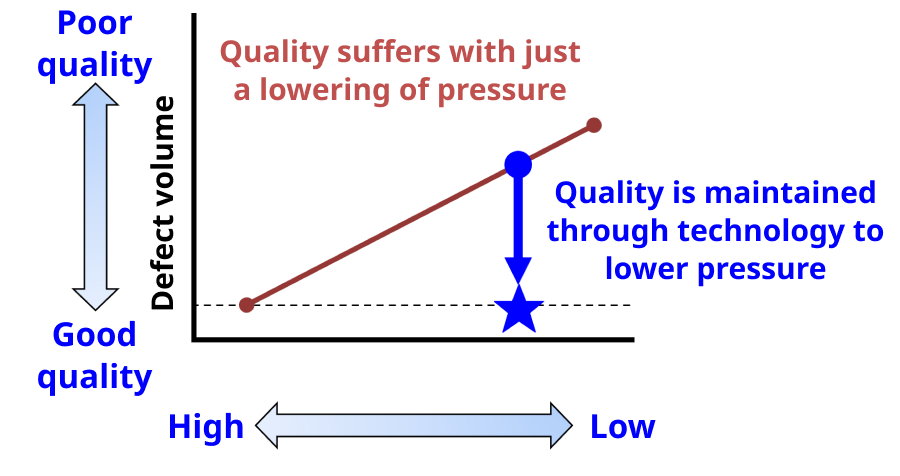
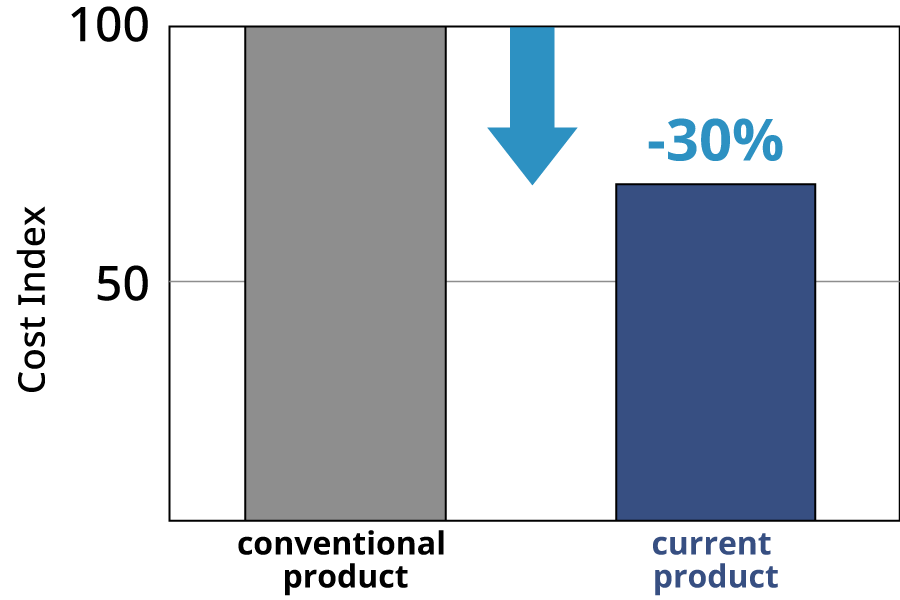
casting cost by approximately 30%
Weight reduction thanks to an optimal rib design
Calculating strength with the use of CAE
Optimal rib placement has been designed with a focus on both the necessary strength and the manufacturing requirements
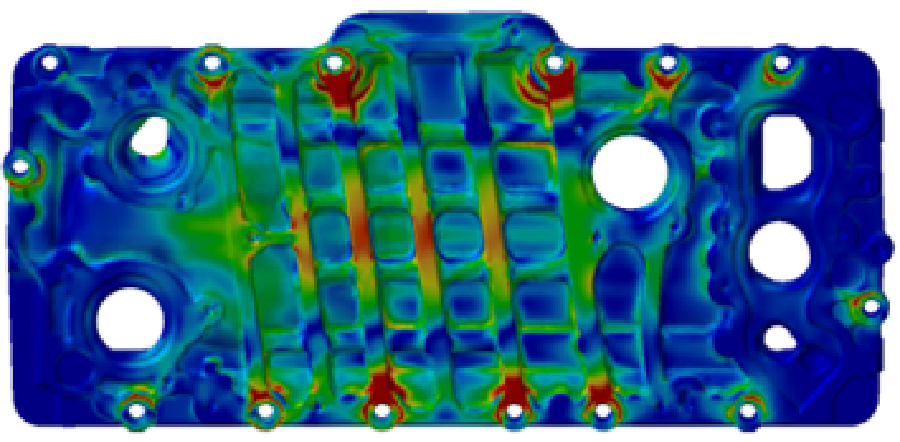
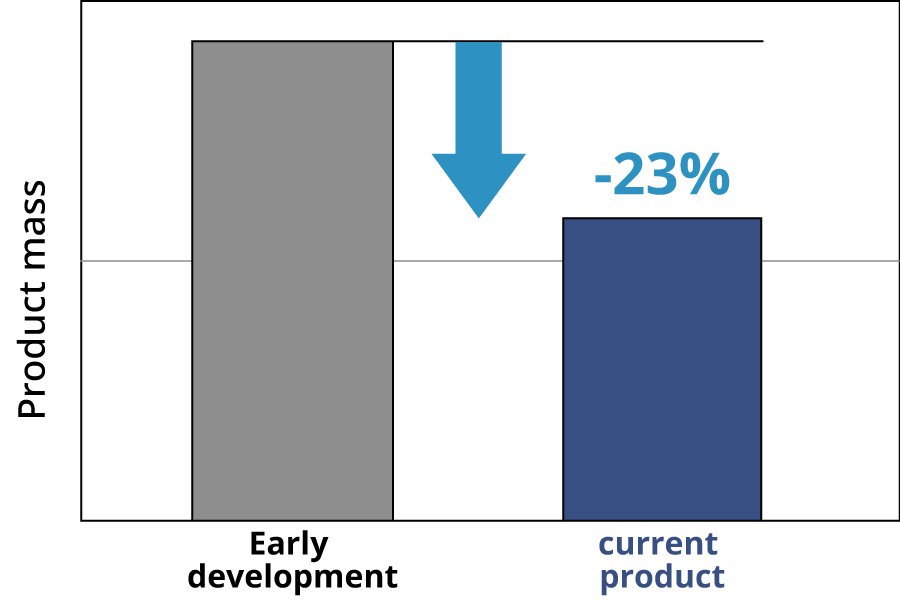
the weight was reduced by 23%.