Testing and evaluation
We propose optimal specifications by completing design investigations in the upstream section of the V process.
Analyses and simulations, which are upstream processes in the V process, and unit testing and evaluations of actual machines, which are downstream processes, are all performed in-house. Directing feedback of evaluation results into the analytical technology makes it possible to improve the strength and precision of model-based development (MBD).
Accordingly, we can propose highly accurate and optimal materials from the initial stages of development and thereby help clients speed up the development process and reduce man-hour requirements.

Accommodating client needs with an extensive array of technological solutions covering everything from basic research on to the manufacturing of engine parts
For our slide bearings, our flagship product, we must ensure excellent slide and lubrication performance and exceptional durability and wear resistance in extreme sliding environments. For this reason, we observe and measure the coefficient of friction, lubrication performance, and wear performance under conditions that replicate actual usage conditions as much as possible through stand-alone and actual equipment testing and work to harness the results of this process to develop and manufacture high-performance bearings.
Unit testing
Basic tribology testing machines
- Stick-slip testing machine
- Pin-on-disk testing machine
- Ring-on-disk testing machine
- Thrust testing machine
- Reciprocating slide testing machine, and more
Every type of sliding motion can be covered to enable performance evaluations to be conducted.
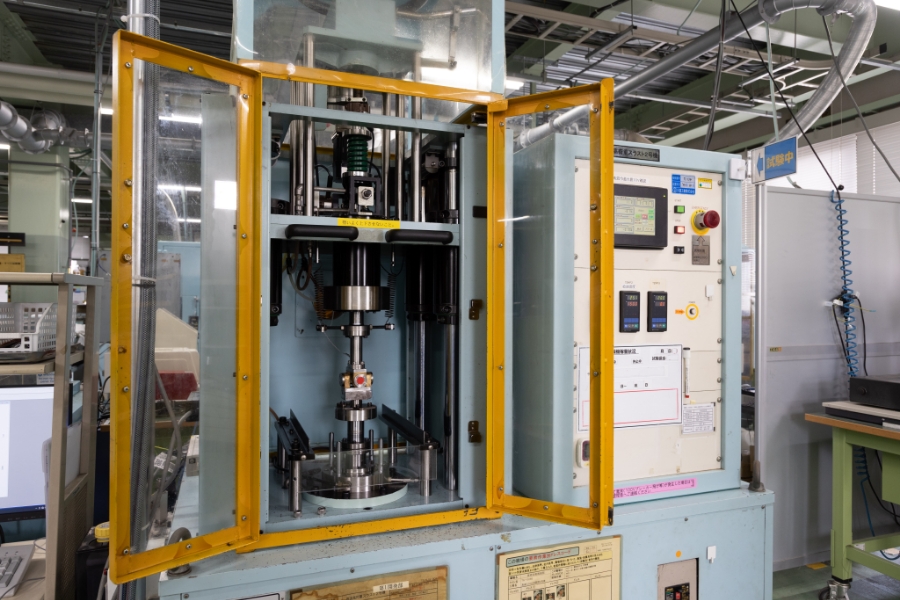
Engine bearing testing machines
- Reciprocating dynamic load testing machine
- Rotational load testing machine
- Static load testing machine
- Single-side load testing machine
- Low-temperature friction testing machine, and more
We conduct evaluations of durability and reliability in such terms as fatigue resistance, seizure resistance, wear resistance, and robustness against foreign matter.
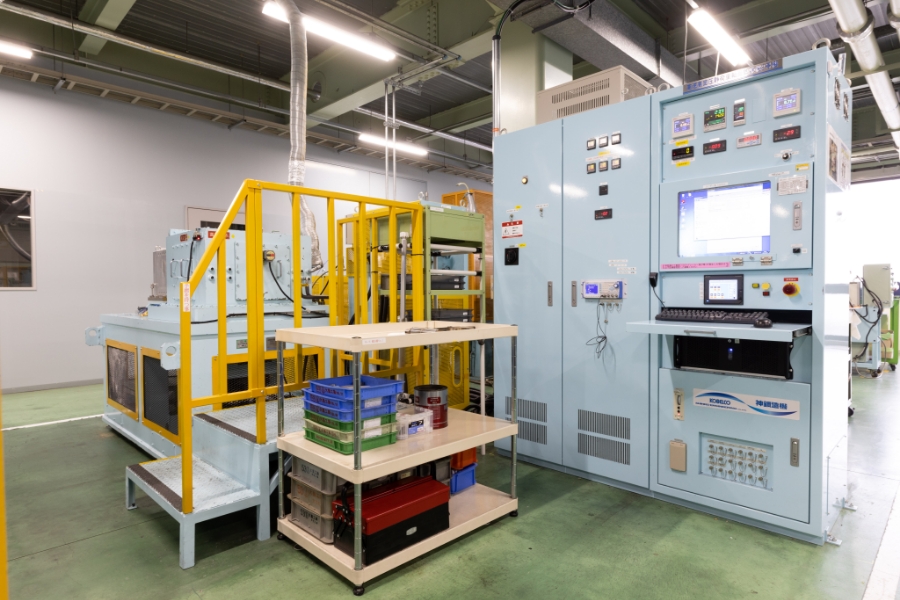
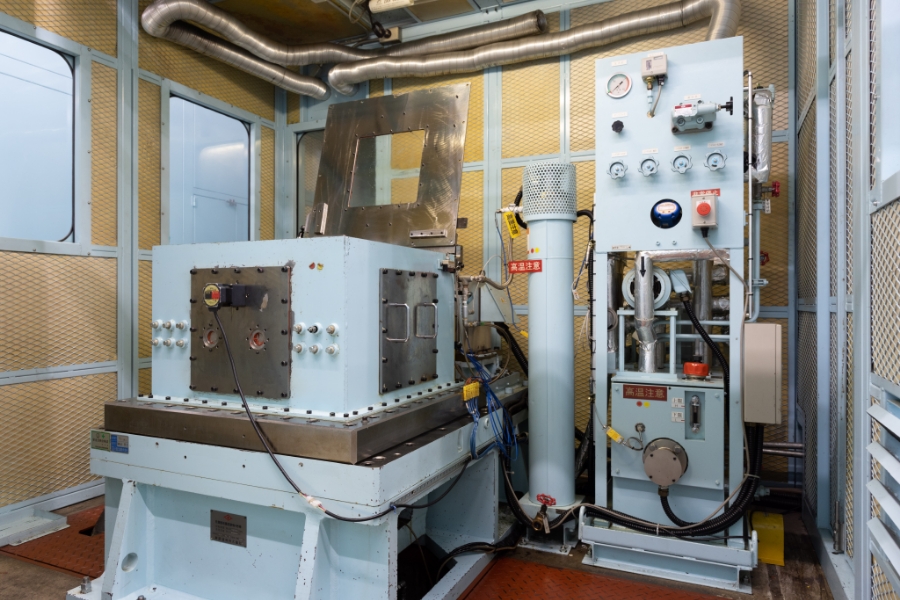
Bush washer testing machine
- Static/dynamic load testing machine
- Rotational load testing machine
- Partial contact load testing machine
- Friction testing machine
- Vibration testing machine
- Thrust static/dynamic load testing machine, etc.
We conduct evaluations of durability and reliability in such terms as fatigue resistance, seizure resistance, wear resistance, and robustness against foreign matter.
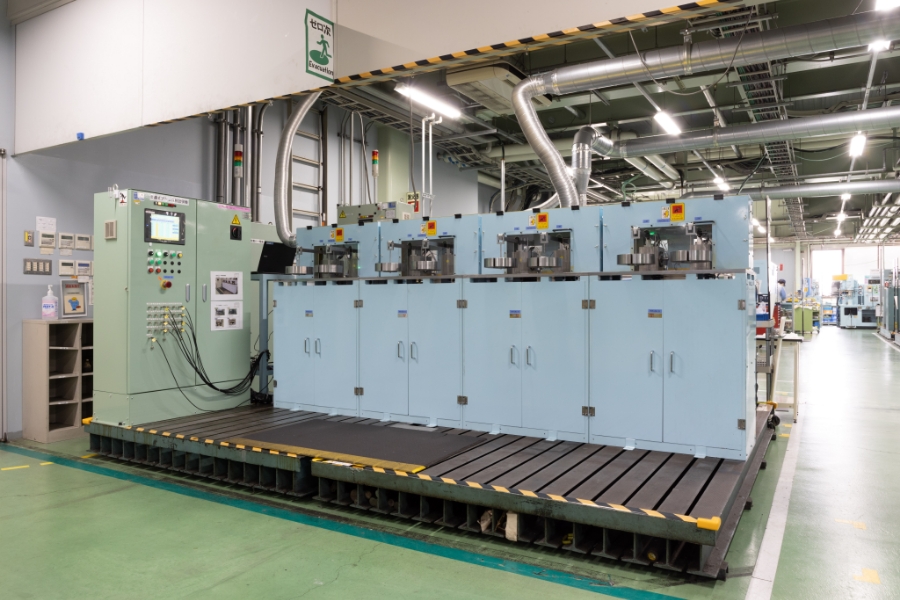
Compressor bearing testing machines
- High-pressure atmospheric friction and wear testing machine
- CO2 high-pressure atmospheric testing machine, and more
We conduct evaluations of durability and reliability in such terms as the seizure resistance and wear resistance of compressor parts.
Other testing machines
- Vibration testing machine
- Environmental testing machine
- Actual product testing machine (vacuum pumps, EGR valves), and more
Performance and durability evaluations are conducted for the development and mass production of various products.
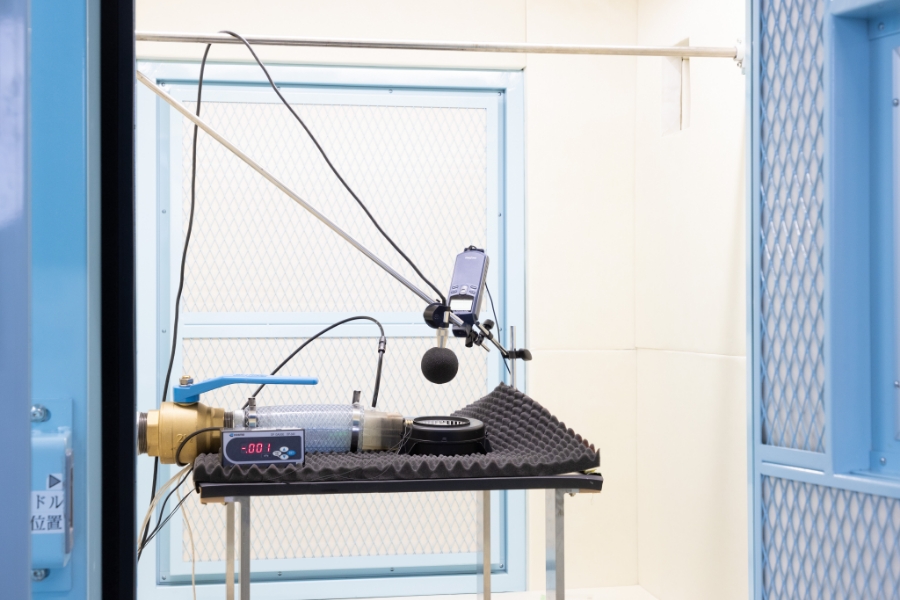
[Case studies of the use of stand-alone testing machines]
Clarifying the bearing seizure mechanism with AE measurements
By positioning AE sensors in a bearing and taking measurements with the use of a bearing testing machine, we can ascertain the process by which bearing materials become damaged in real time. This can reveal the mechanism by which seizures occur and is used for designing materials.
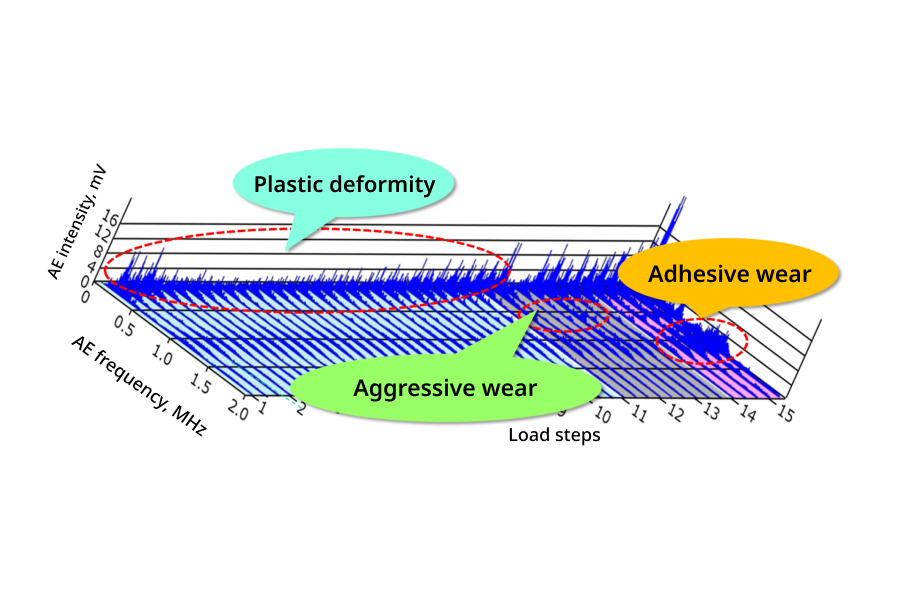
Related pages | Shedding light on mechanisms underlying issues with bearings |
---|
Bench for conducting evaluations of actual engines
This bench can be used to conduct performance evaluations and durability evaluations and take measurements of engine characteristics. Contracted testing services can also be offered.
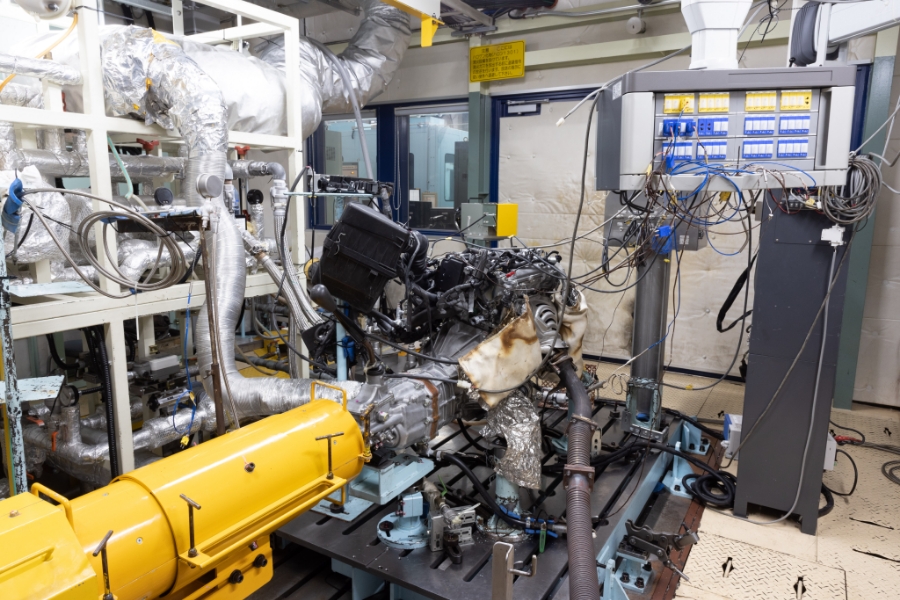
Bench for conducting evaluations of actual transmissions
This bench can be used to conduct performance evaluations and durability evaluations and take measurements of transmission characteristics.
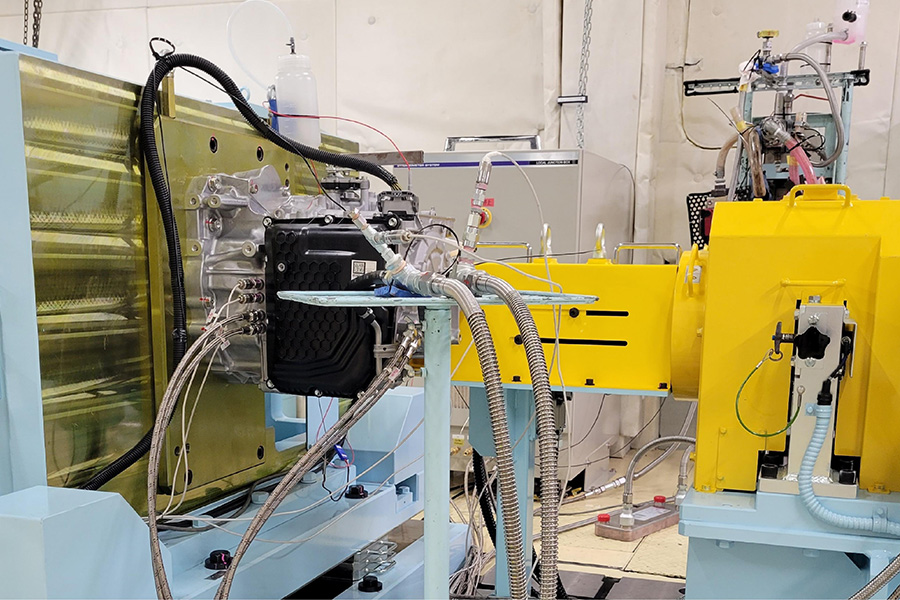
Actual compressor testing equipment
Efficiency measurements under conditions equivalent to those acting on actual compressors can be taken.
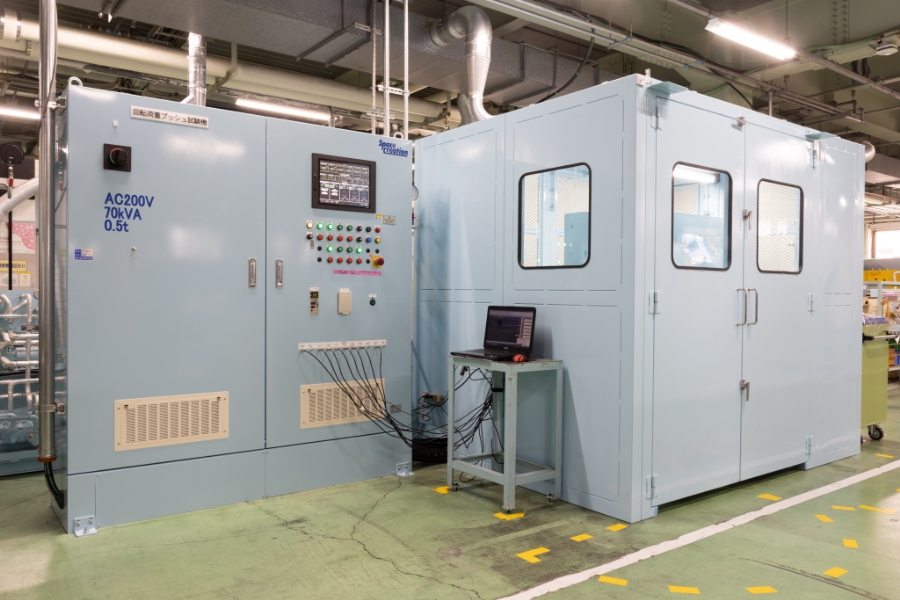
[Case studies of the use of a bench for conducting evaluations of actual engines]
NClarifying the relationship between NV measurements and axial center behavior
By taking NV measurements after attaching an acceleration sensor to an engine in an actual engine test and checking the results against the behavior of the axial center trajectory in the bearing, a correlation can be obtained. This can be used to design bearings with low NV by suppressing the axial center behavior.
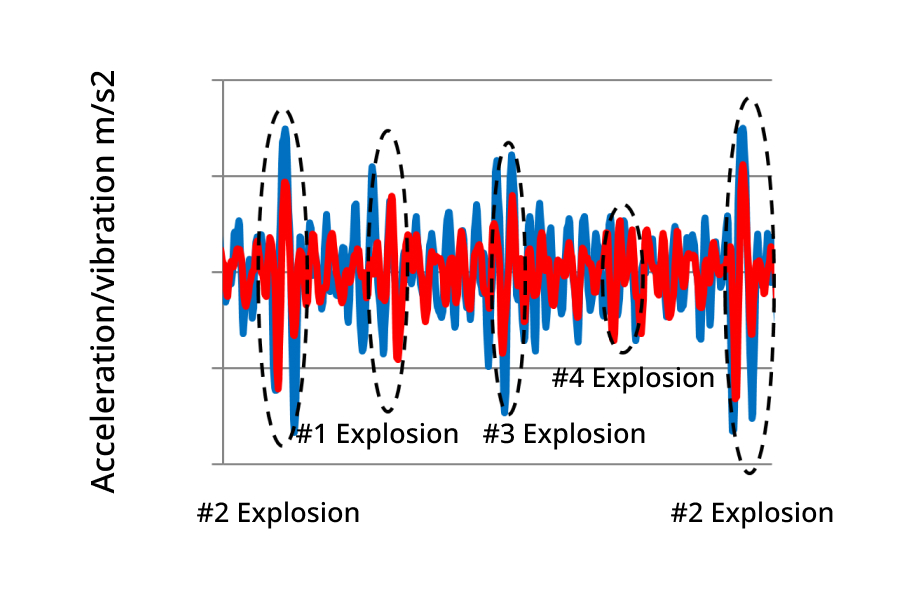
Related pages | Shedding light on mechanisms underlying issues with bearings |
---|