1944年~1962年
「軸受加工工場」からのスタート
支給材から始まった軸受生産
1944年に大豊工業株式会社が発足、翌年8月に敗戦、GHQの管理下で平和産業への転換をはかりつつ、ネジやナット、ダイスコマの加工をはじめた。 復興の輸送力確保を前提に1945年にトラック(月産1,500台)、1947年に乗用車(1500cc以下、年間300台)の生産許可を受けて自動車生産は再開した。トラックに関しては材料不足で実質500台にも満たなかった時代であった。
1946年秋、「部品製造については今後、協力工場の専門化を図り、任せていく」というトヨタ自動車工業(株)の方針により、当社はすべり軸受である「青銅ブシュ」の機械加工を引き受けることとなった。 しかし、町工場に過ぎなかった当社には、すべり軸受の知識どころか精密加工用設備もなく、その一式をトヨタ自動車工業(株)から譲り受けるとともに、技術指導を受けて1947年から納入を開始、主にトラック向けのブシュだった。 当初は支給材(直径15㎜、長さ250㎜の青銅パイプ、通称ちくわ)を切削加工して仕上げていたが、巣が多く生産は不安定だった。それらを解消するため、鋳物技術を習得し1949年には鋳物工場を新設し、素材から加工までの一環生産体制を整えた。 戦後の日本で初めて新設計開発されたトヨペットSA(S型エンジン)やトヨペットスーバー(R型エンジン)などが発売されたのもこのころである。
「すべり軸受メーカー」への布石
1954年、プレス工場を新設し、巻ブシュの生産を開始した。このとき当社では銅板を切断し油溜まりや油溝をプレス成形した後、荒曲げして鉄パイプに打ち込こんで仕上げたものを巻ブシュとして販売していた。 鉄に銅板を打ち込んだだけのこのブシュは銅と鉄の間に隙間ができ、軸の回転に伴って抜け落ちたり、熱伝導が悪く激しく摩耗するなど、バイメタル軸受とは言い難いものだった。 この時期、アメリカ・フォード社の巻ブシュを見る機会があった。それは銅と鉄を圧着もしくは溶着してあった。早速、これをサンプルに品質改良に取り掛かった。 最初は圧着から試みたが、温度管理が難しく品質は安定しなかった。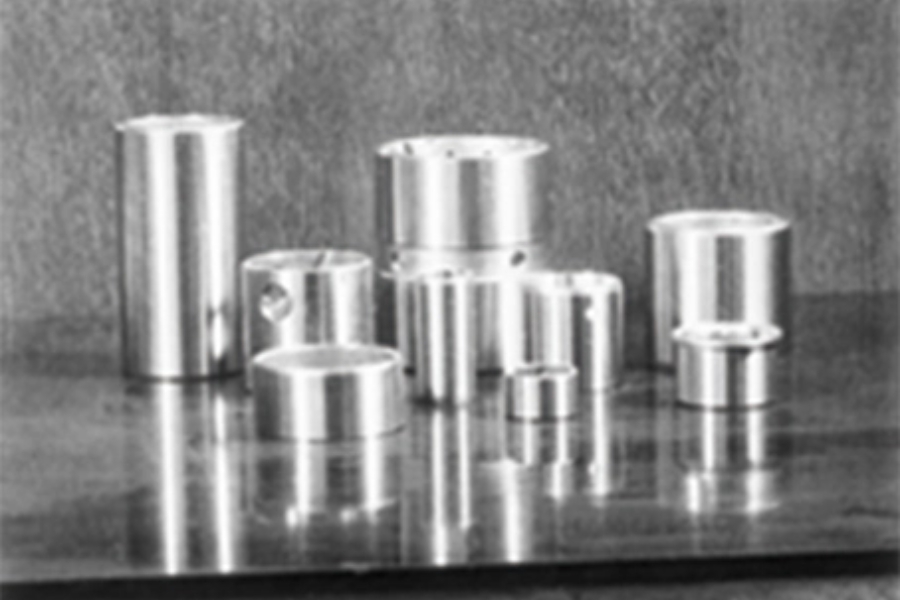
「すべり軸受メーカー」としての生き残り策
戦後さまざまな制約はあったものの、先進諸国からの輸入を厳しく管理・規制するなど、日本の産業は保護されていた。 しかし、諸外国からの要請もあり、日本政府は1960年に「貿易為替自由化大綱」を策定、国際競争力の高まった産業から順次輸入を自由化するとし、自動車産業は1965年を期日と定められた。 当時、日本の自動車技術は欧米に比べ20年のギャップがあるとされていた。 当社でもブシュ用バイメタル素材の生産において鋼板シートからコイル材を使用するまで技術開発を進めていたが、まだ課題は多く、1965年までにそれらを解消するためには先進国からの技術導入が必須と判断された。 早速、アメリカに出向き技術供与先のリサーチを開始、その結果、合金粉末を焼結する方法でエンジンベアリング・ブシュ・ワッシャなどのすべり軸受を生産していたアメリカ最大手のFMBB社(FEDERAL‐MOGUL、BOWER BEARING)に的を絞り技術供与の交渉を進めた。
FMBB社からは技術供与ではなく技術提携とするか、合弁会社設立が条件という回答だった。 また、通産省の「産業合理化審議会」において、国内自動車関連会社を事業別にグループ化し、コスト・性能・生産規模などを少しでも海外自動車関連企業に近づけようという構想があった。当社以外の国内軸受メーカー3社は既に海外メーカーとの提携を終えていたことと、規模的に弱小だった当社は不利な立場にあり、一部には諦め感もあった。 しかし、ここで、当社にとってその先を左右する好機を迎えることとなる。 トヨタ自動車工業(株)においても独自製法で内製していたエンジンベアリングに関して、アメリカから技術を導入し新工場にラインを設置する計画があった。
しかし、戦後まもなく「協力工場の専門化」という方針の下、ブシュを主とした軸受メーカーとして実績のあった当社の状況を知り、エンジンベアリングの生産も委託する意向があるこ伝えられた。 早速、政府当局の承認を前提にFMBB社との技術援助契約交渉を具現化、この中には当社株式の15%をFMBB社に譲渡するという条件も含まれていた。 国内に4社の軸受メーカーを存続させることで過剰競争を懸念する通産省・大蔵省・科学技術省に対し、連日のように訪問し説得、申請後半年を経て政府からの承認を取り付け、1961年12月、正式に「技術導入10ヶ年契約」を締結した。 これで当社は名実ともに「日本の軸受メーカー」としての位置づけが明確になった。 残る課題はトヨタ自動車工業(株)が危惧する外資の受け入れであった。危惧とはエンジンの心臓部に用いるエンジンベアリングを海外メーカーに制される恐れである。当社の企業規模からすれば致し方ないことだった。
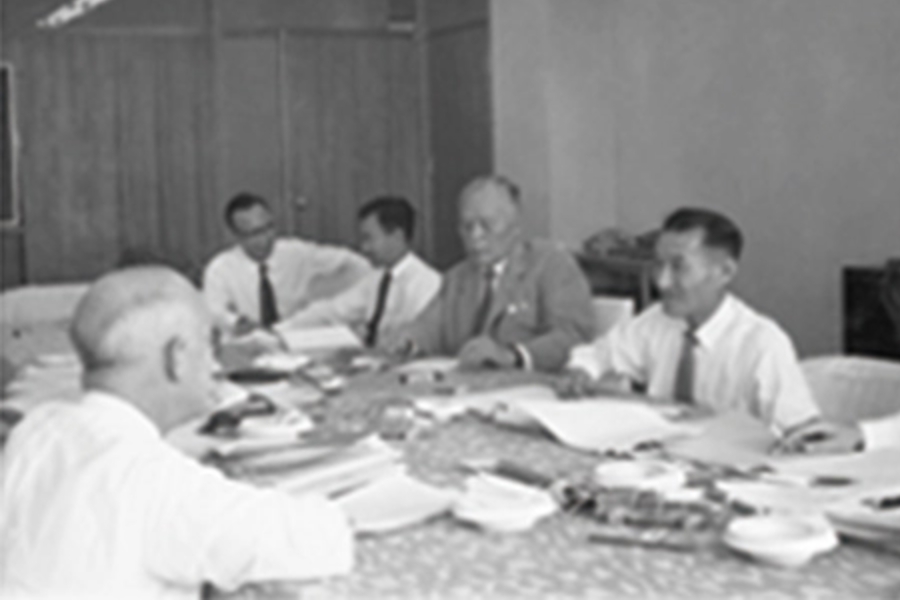
遠心鋳造法によるバイメタル生産を習得
軸受メーカーとして政府認証、トヨタ自動車工業(株)からのエンジンベアリンク生産委託、増資による企業規模の拡大、FMBB社からの技術導入など、短期間で目覚しい変化を遂げた当社であったが、FMBB方式によるエンジンベアリングの生産開始に関して、課題がなかったわけではない。 その最も大きなものは当社はそれまで、エンジンベアリングの生産を経験したことがないということであった。3/100㎜の精度が要求されるブシュに対してエンジンベアリングは3/1000㎜の精度が要求された。 当時、当社の技術者は「初めてエンジンベアリングを見たときは、内面ピカピカで難しそうだなと思った」くらいで、流体潤滑に関する知識はもちろん、とくに海外から導入する生産技術に関しては、全てが未知のものだった。 そこで基本に返り、まず国内在来の技術を経験し、それによってエンジンベアリングの知識を深めるという観点から、1961年にトヨタ自動車工業(株)にあったエンジンベアリング生産設備の何ラインかを当社に移設し実際にエンジンに搭載できるまでの加工精度に高めることになった。
このときの製法は遠心鋳造方式を用いており、長さ30~40㎜の鉄パイプを回転させ、遠心力によって合金を溶着、これを縦に切断し、合せ面、内面を機械加工して半割りメタル(エンジンベアリング)に仕上げていた。 100点を超える設備の移設には4~5ヶ月かかることが想定され、その間生産を止めることができないためトヨタ自動車工業(株)に残っている設備をフル回転させるため、当社から96名の社員を派遣することとなった。 これは生産量確保のみならず、実践的で細かな技術習得となり、移設完了後もスムーズに生産を開始することができた。当社へ移設した設備での生産量は月産9万個、当時のクラウンやニューコロナ、トラックなどに用いられた。
FMBB社の合金粉末と焼結法
ブシュの連帯鋳造法に続き、トヨタ自動車工業(株)から移設した遠心鋳造法によるエンジンベアリングの生産を軌道に乗せていた当社であったが、更なる技術革新においてはさまざまな課題を抱えていた。 それは材料技術、生産技術、品質管理など技術的課題から安全性、収益性にいたるまで多岐にわたり、さらには貿易の自由化による国際競争力の強化も急がれていた。これは当社に限らず、日本の軸受メーカー全てに共通したものだった。 特に技術的課題に関しては、欧米メーカーが1920年代(昭和初期)に既に経験し克服していた内容だった。 FMBB社の合金粉末の組成には目を見張るものがあった。巧みなアトマイズマシンによって製造される焼結用銅鉛合金粉末は、銅が鉛を被服する状態となっており、当社が抱えていた鉛の偏折やブローホールなどを解決し、鉛含有量50%という銅鉛合金製法の領域を超えた超高鉛を実現していた。
鉛の含有量調整域の広さは、低速・高荷重から高速・中低荷重にたいるまで幅広い領域で最適な特性をもった軸受の製造を可能とし、なじみ性の上でもホワイトメタルの性能を上回っていた。とくに、高鉛の軸受は耐圧強度が高いわりに軟らかく、オーバレイ処理や、軸の焼入れが不要でコストダウンにもつながるものだった。 生産技術の大きな違いは軸受素材の製法であった。日本では遠心鋳造法によるバイメタル軸受素材生産が主流であったが、欧米では既に焼結法が主流となっていた。 とくにFMBB社は焼結法に関して高い技術を持っており、裏金との密着性、組織の微細性、鉛の分布状態などが非常に良好で、軸とのなじみや耐圧強度、耐疲労性などに優れた性能を発揮していた。

すべり軸受の歴史
ライニング・裏金・半割
近代的な「すべり軸受」の開発はアメリカの金細工師だったIsaac Babbittが1839年に考案したホワイトメタル(通称バビットメタル)からはじまります。 この合金は錫、銅、アンチモンなどの低融点金属が主材で、とくに軸受に適した配合のものは減摩合金と呼ばれていました。 錫基のホワイトメタルに続き、鉛基のものが開発されます。
何れも軟質で融点が低く、なじみ性に優れていましたが、温度上昇により疲労強度が低下するため、薄肉化(マイクロバビット:0.1~0.3㎜級)が進められました。 はじめ、軸受合金はハウジングに直接熔着して使用してしいましたが、1900年代初めにはソリッドタイプの軸受をハウジングに挿入する方式がとられるようになります。 その後、合金を裏金に熔着したバイメタルが考案され、半割形軸受としてハウジングに組み付けるようになります。裏金には主に青銅が使われていましたが、強度を高めるため、1920年ころからは炭素鋼が使われるようになりました。 このように軸受の表面(ライニング)で摩擦特性を満たし、裏金で荷重を支えるバイメタル構造のすべり軸受は20世紀初頭に確立していました。
また、合金の開発も進み、Kelmetが銅鉛系合金(通称ケルメット合金)を発明、1924年ころから使われ始めます。 はじめは鉛25~40%の銅合金を遠心鋳法によってバイメタル化していたのですが、鉛の溶解度に起因した偏折、ブローホール、収縮割れが発生し品質は不安定だっようです。1940年ころに連帯焼結法が考案されそれ以降は焼結が主流となりました。 適度に硬く熱伝導性の良い銅マトリックスの中に、柔らかい鉛が固溶せずに網状に分散することで、耐疲労性、耐焼付性に優れ、高荷重用軸受に適していました。 これにより、低荷重用にはホワイトメタル、高荷重用には銅鉛合金という体系が定着します。 これは、アルミニウム系合金が軸受材料として実用化される1960年ころまで続きました。 ちなみにホワイトメタルが実用化された1839年の日本は、天保10年、江戸時代中期でした。
1944年~1962年
FMBB社方式の早期習得
1963年、FMBB社と同等の設備を導入した新工場が完成、10月からはパブリカUP10のU型エンジン(697cc、強制空冷水平対向2気筒OHV、最高出力28PS、最大トルク5.4kg・m)向けに月産4万個の鉛基ホワイトメタル[L200]の生産を開始した。 FMBB社からの技術導入に際しては製品の早期出荷を前提に、合金粉末の製法から焼結、加工法、生産方式など、全てを完全に再現することとした。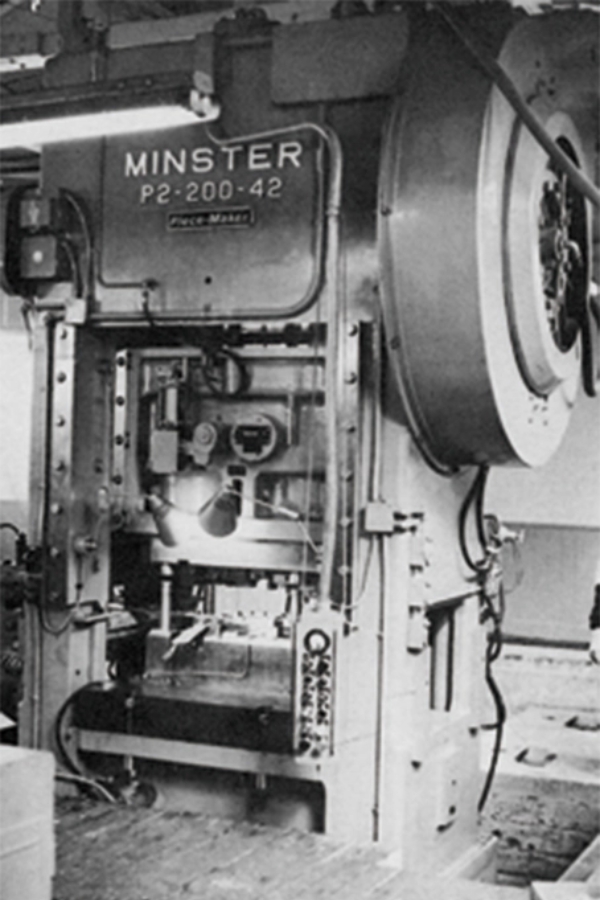
ロット生産から独自の流れ生産へ
FMBB社方式の完全再現により製品の信頼性を早期に高めることができたが、日本の自動車生産にはそぐわない部分も多くあった。 とくに生産方式において、FMBB社と同様にロット生産方式を採用していたのだが、人件費と材料費の割合で人件費が上回るアメリカではロット生産が有利だったが、材料費が高い日本では不利だった。 さらに、熟練度の高いFMBB社の社員に比べ、経験の浅い当社社員にはロット生産は不向きだった。 そこで、巻ブシュ量産ラインの工程間搬送などを工夫しながら、流れ生産・同期化ラインへと変化させ、1965年1月に独自の生産方式を稼動させた。。
トヨタ自動車工業(株)でも、現在、世界的に注目を集めている「かんばん方式」が考案され、日本の自動車産業が独力で世界に羽ばたこうとしていた時代であった。 「貿易為替自由化大綱」による自動車輸入自由化の期日だった1965年、日本の自動車産業はさまざまな懸念事項を払拭し確実に成長、世界を驚嘆させたトヨタ2000GTやスポーツ800が発売されたのも1965年だった。 同年、FMBB社は(FEDERAL‐MOGUL Inc.:FM社)と社名を変更した。 また、摩擦、摩耗、潤滑を総合的に取り扱う科学技術の一分野として「トライボロジー」という言葉が発祥したのもこの頃だった。
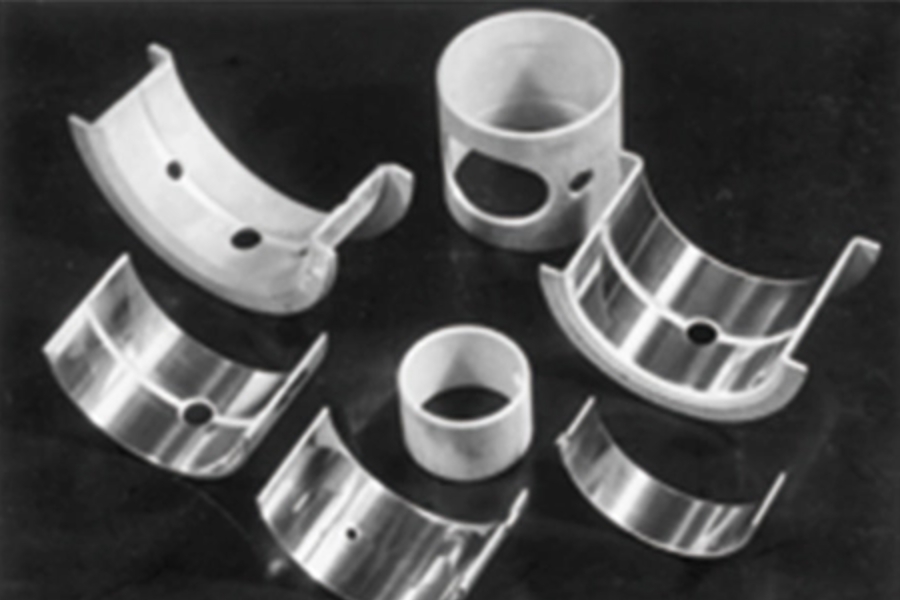
トライボロジースペシャリストへ布石「3つの革新」
「3つの革新」で新時代に立ち向かう
1969年初頭、「人事革新」「技術革新」「経営革新」を軸とした経営理念「3つの革新」が提示された。 これは、世界を相手に急成長を続ける日本自動車産業の波に飲まれること無く、企業としてその波に乗り、より成長するために企業体質の強化を図るものであり、その後この革新を実現するため様々な施策が講じられていく。 とくに、「技術革新」は「製造技術:造る技術」「製品開発技術:創る技術」共に、外部からの導入をはじめとする既存技術の応用ではなく、独自の技術を確立して、それを発展させることを狙いとしていた。 当時の日本は国際的にも一定の技術水準に達しており、「技術を買う時代」から「技術で取引する時代」へと進化していくことを意識したものであった。細谷工場新設で「造る技術の革新」を目指す
3つの革新が提示されて間もない1969年8月、細谷工場が完成した。 モータリゼーションの高進で日本の自動車生産は拡大を続けており、1967年9月、トヨタ自動車工業(株)の生産量は月産8万台を超えて世界第5位に達成、増産は毎月続き1972年には300万台体制が予想されていた。 当社でも、現本社工場で合理化、省力化を重ね増産対応を進めてきたが、敷地・設備ともに限界に達していた。 そこで、20年先の需要予測なども視野に、エンジンベアリングのみを対象とする「精密機械加工工場」として位置づけ、トヨタ自動車工業(株)元町工場に近い細谷町に、軸受生産専門工場の建設に踏み切ったのだった。 その後も自動車生産量拡大に対応すべく増築され、1973年には新たに合理化ライン6本を新設するに至った。これにより「造る技術の革新」の基盤を整えていった。「摩擦のない世界はない」をポリシーに「創る技術の革新」を推進
3つの革新による「技術革新」の一翼となる「創る技術」においても、原点に戻り軸受そのももの基礎研究から着手し、ゼロからの創造力強化を目指した。 そのポリシーは、「摩擦のない世界はない・・物の動くところには必ず摩擦が生ずる。その摩擦を軽減して省資源・省エネルギーに貢献する。」であり、基本理念を「信頼性を支配する摩擦技術の研究を通じて顧客への寄与」とし、技術革新の新たな礎とした。 これは、戦前より内燃機関の権威であった富塚清名誉教授(東京大学)の言葉「物が動くところ必ず摩擦が生じ、”内燃機関(エンジン)の死命を制するもの潤滑”」(1963年)をヒントとしていた。 そして、研究への取組は、「ハードウェアのみならずソフトウェアも、単体のみならずそれらを取り巻くシステムも、そして現在のみならす将来への対応も」をモットーとし、
- 独自の考察 --- そこで何が起きているか
- 本質的追及 --- 専門的な機能の掘り下げ
- システム的解明 --- 環境・周辺を含めた最適化
という要素のもと、
- 企画段階からの最適化
- 機能設計段階における最適化
- システムとしての最適化
をステップ的に実施して顧客への寄与を図ることとした。 このように、潤滑の在り方を含め、潤滑諸元診断・摩擦特性解析・材料解析までシステム的に解析しようとする取り組みはすべり軸受業界では初めての試みであった。
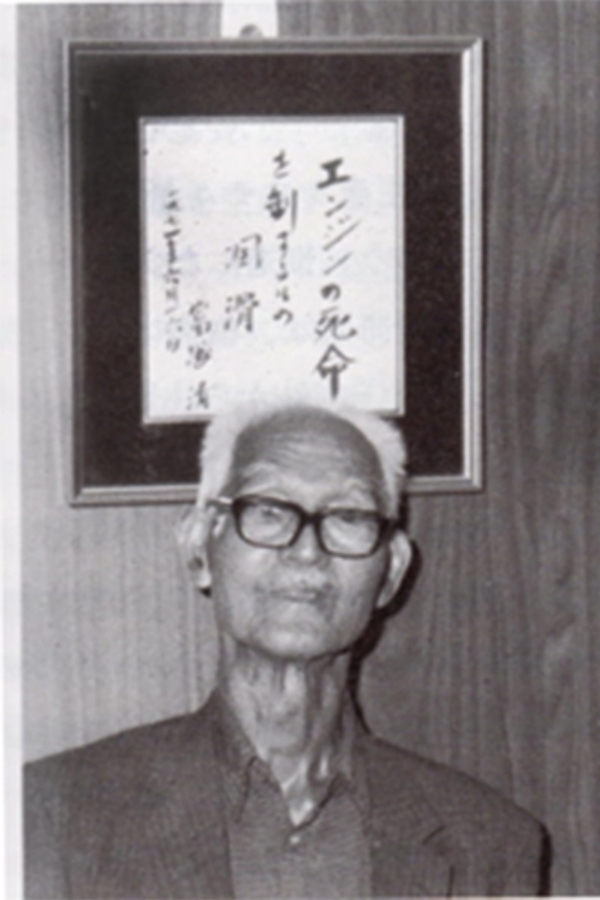
1971年~1976年
無給油樹脂軸受[FBシリーズ]誕生
1971年、当社独自開発の[FB209B]を使用したに無給油軸受軸受(ブシュ)の量産を開始した。 FBシリーズは裏金に焼結された銅合金にフッ素樹脂を含浸したもので、銅合金のマトリックス部で荷重を支え、樹脂がもつ自己潤滑性により無給で使用できた。日本の自動車設計思想に適応した独自の軸受開発
当社の技術部では生産を中心としたFM社からの技術導入と並行して独自に合金研究も進めていた。 しかし、大部分は客先から与えられた仕様に忠実に応えるための研究が主で、軸受そのものの開発とはいいがたかった。FM社からは軸受材料の技術も教示されていたが、大排気量・高出力が前提で全体的に余裕のあるエンジン設計だったアメリカと、小排気量・高出力の設計思想を持っていた日本では、おのずとして軸受に対する品質・性能要求に差がみられ、日本独自の軸受開発が必要だった。
これらを背景に、技術部を解消し開発室を新設した。 ここでは客先が設定するエンジン仕様に対し、最適な軸受を設計し、満足できる品質と価格、納期でのハードウエア提供はもちろん、流体潤滑理論をはじめとする、すべり軸受のノウハウをエンジン設計へフィードバックできるソフトウエアの構築を目指した。 開発室が立ち上がると、豊田中央研究所との技術契約も実現し、研究や特許の面で援助と指導を受けることができるようになった。
具体的な研究対象としては、
- すべり軸受を主体とした摩擦部位関係
- 摺動部よりの漏れを防ぐメカニカルシール関係
- 流動するガスなどの流量制御をつかさどるバルブ関係
などであった。
実験棟の設置
1972年2月、細谷工場敷地内に実験棟が新設され、同工場は生産拠点としての位置づけだけでなく、当社がすべり軸受のリーディングカンパニーとして揺ぎない地位を獲得していくための拠点となった。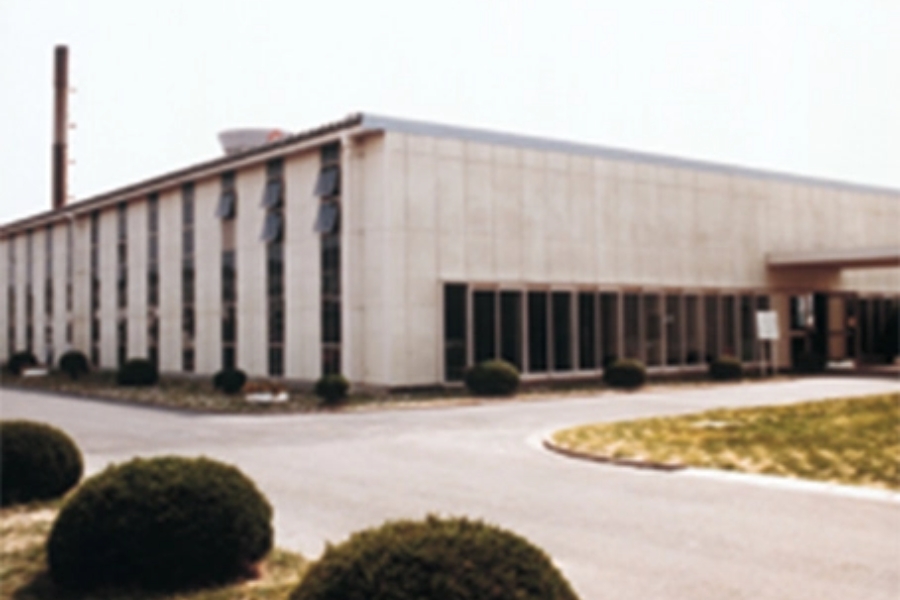
マスキー法
本格的な排気ガス規制
1970年、アメリカで大気浄化法が大幅に改正された。 通称「マスキー法」と呼ばれるこの改正法には、1975年以降に製造する自動車の排気ガス中の一酸化炭素(CO)、炭化水素(HC)の排出量を1970-1971年型の1/10以下に設定する。
さらに1976年以降に製造する自動車の排気ガス中の窒素酸化物(NOx)の排出量を1970-1971年型の1/10以下にするという厳しいもので、それぞれを義務付け、達成しない自動車は期限以降の販売を認めないというものだった。 これを受け、世界中の自動車メーカーが一斉に、さまざまな方式の排気ガス清浄化技術の開発を始めた。
流体潤滑理論に基づく、画期的なエンジン荷重計算システムを完成
このように設備の充実や、各界の権威との交流により、当社の研究開発おけるフィロソフィーが明確になっていくとともに、トライボロジーを中心とする研究体制を確立して、潤滑諸元診断、摩擦特性解析、材料解析などの「システム的解析」に拍車がかっていった。 実験棟には走査線電子顕微鏡、アイソスタティクプレス、各種実態試験装置、さらに独自設計による基礎試験機、ベンチ試験機などが整備され、軸受関係の基礎解析は実験室ですべて解明できるようになった。 また当時、軸受や素材の複雑なメカニズム解明のため、多変量解析手法を応用していたが、軸受設計や潤滑理論計算などが高度化するにつれ、膨大な量のデータ処理が必要となっており、1973年2月、DEMOSを導入した。 これは、300bpsのモデムを使ってオンラインで利用できる当時としては画期的な科学技術計算サービスシステムで、東海地区で導入したのは当社が初めてだった。 多変量解析とDEMOSの組み合わせは当社の研究開発の信頼性向上とスピードアップに大いに役立った。 さらに1973年、実験棟と並んでエンジン棟が設置された。日本のエンジンすべてに対応できるテストベンチを設置したこのエンジン棟の完成で、基礎研究による理論確立から実機試験による理論の検証までが社内で実施できるようになった。 これらをバックグランドとし、1975年に軸受動荷重解析プログラムを開発、1977年には軸受トラブル予防システムを確立し、その集大成として、1980年に「エンジン荷重計算システム」を完成させた。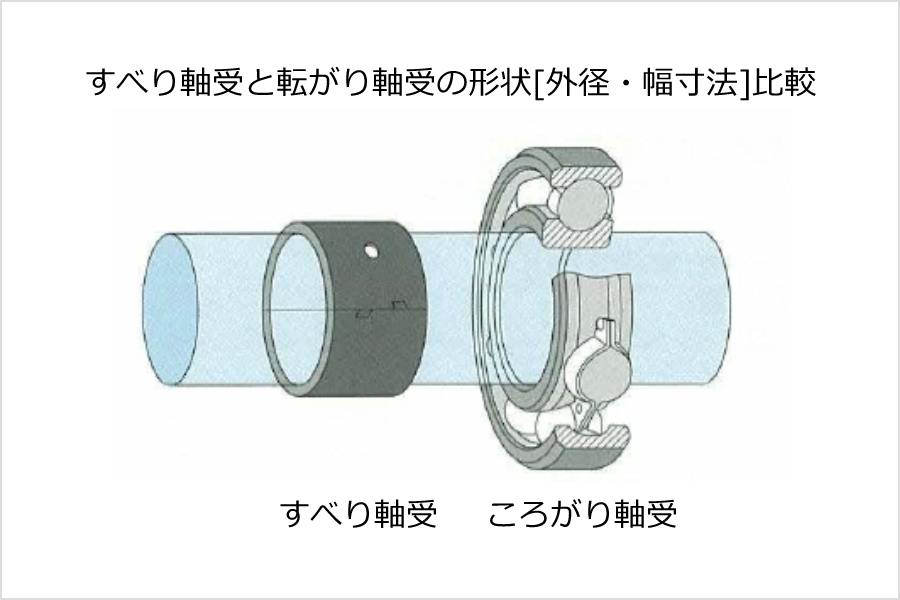
特殊軸受「シュー」の生産を開始
1976年、斜板式クーラコンプレッサ用すべり軸受「シュー」の生産を開始、エンジンベアリング、ブシュ、ワッシャに次ぐすべり軸受の主力製品となった。 これまではクランク式クーラコンプレッサーが主流だったが、小型高効率コンプレッサとして、斜めにした円盤を回転させその軌道に沿わせてピストンを作動させる斜板式クーラコンプレッサーが開発された。 鋳鉄製の斜板とピストンとの間にすべり軸受の一種であるシューが用いられており、当社が開発した銅合金[HF16]を用いたシューが採用された。 斜板に接触する部分に[HF16]を用い、ピストン側には鋼球を用いた2ピースタイプだった。![[HF16]シュー](/assets/media/2023/04/img-tribology_history-9.jpg)
1977年~1988年
FM社との新たな関係
1977年、FM社と締結した「技術導入契約」が終結した。1961年12月に締結した「技術導入10ヶ年契約」は、1970年に「技術援助6ヶ年延長契約」として更新されていた。
この間、当社は軸受の生産技術習得から始まり、材料の独自開発、流体潤滑理論を応用した軸受設計など「軸受メーカー」として培った総合的な力はFM社からも認められるほどになっていた。当時、マスキー法によりアメリカ市場においても自動車の小型化が求められており、そのノウハウに関して当社に期待が寄せられていた。 これらを背景に1979年、両社対等の立場での「相互技術援助契約」が締結され、必要に応じて技術交流会や工場見学会が開催された。
この交流によって、1981年には当社が開発した軸受生産設備をFM社が購入したり、課題となっていたアルミニウム合金軸受の耐久性能などに関しても、当社からのアドバイスが有効にはたらいた。 このように、牽制的ではなく、積極的で具体的な契約は双方の技術力向上に大いに役立った。また、同業社間での友好的な契約は国内外ともに稀なことだった。
摩擦技術研究センター新設
1981年9月、実験棟に隣接して鉄筋2階建て(面積2,500m²)の「摩擦技術研究センター」が完成した。 経営理念「3つの革新」によって、活性化していた研究開発であったが、さらにその専門性を高め、トライボロジースペシャリストとして他社との差別化を図るために不可欠な施設であった。建設計画中には「潤滑研究棟」と呼称されていたが、最終的に「摩擦技術研究センター」となり、潤滑という手段だけでなく、材料や仕組みなどの基礎を総合的に研究する施設となった。
これにより、摩擦特性試験機をはじめ、解析装置、計測装置を設置した摩擦技術研究センターではトライボロジーの基礎研究を、実体試験機、祖形材実験機、生産技術試験研究設備、モデル工作設備を設置した実験棟では単体評価から製法の開発を、エンジン棟では実機試験といった、研究開発から製品化への一連の流れが施設的にも整ったのである。
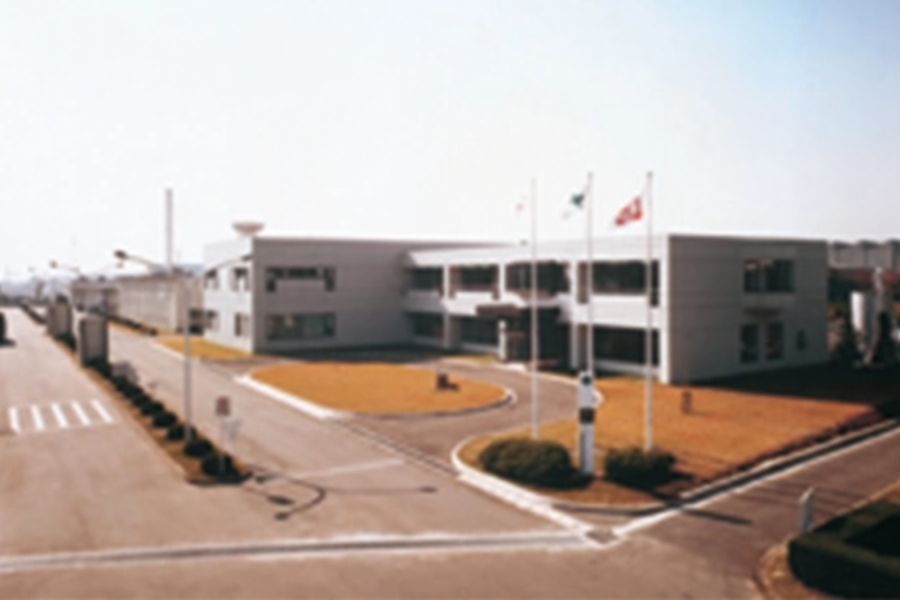
トライボロジースペシャリストとして新たな領域拡大へ
高性能アルミニウム合金「SAシリーズ」
1982年、鋳造軸に対応したアルミニウム合金「SAシリーズ(SA150)」を実用化、6ヶ国で特許を取得した。 アルミニウム合金に関しては、アメリカで1960年ころから使われていたが、耐食性、耐疲労性などの利点はあるものの、軸との「なじみ」が悪く「かじり」を誘発し性能的に不安定な軸受材料とされていた。 この「なじみ」の原理に着目、これまでの「軸受が軸になじむ」という定説を破り、「軸が軸受になじむ」という発想で、あえてSiなどの硬質物をアルミニウムに添加することでかじり現象を解決したのである。 当社では国内他社に先駆け1972年より、FM社から導入した世界標準のアルミニウム合金「ATシリーズ」を使用した軸受を生産しており、耐焼焼付性を改良した「AT300」の開発など既存材料の改良は経験していたが、SAシーズのような独自開発の新素材を実用化したのは初めてだった。 この開発は1978年初頭から始まっておりそのキッカケは鋳造軸で使用できるアルミニウム合金軸受への需要だった。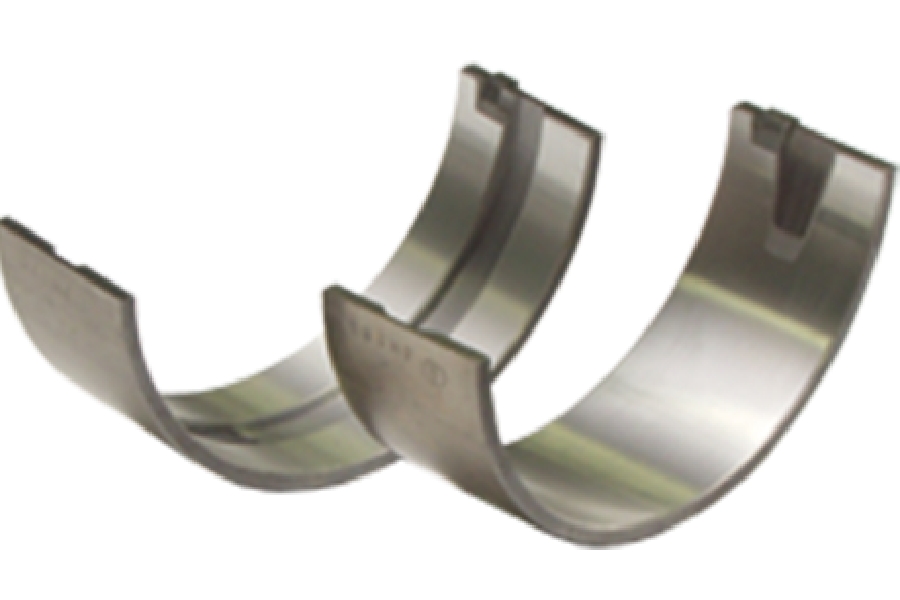
トライボロジーで軸受製品の領域を拡大
摩擦技術研究センターが稼動したことで、今まで以上にトライボロジーの探求が進み、さまざまな製品が開発され市場に送り出された。 1982年、ターボチャージャ部品の開発により、銅合金系軸受材料[MBA2]を使用したフローティングブシュや、テーパランド型スラストワッシャ、カラーなどが製品化された。 燃焼直後の高温・高圧な排気ガスによって駆動するタービンシャフトは150,000~200,000rpmにまで達し、その軸を支えるブシュには超高精度加工が要求された。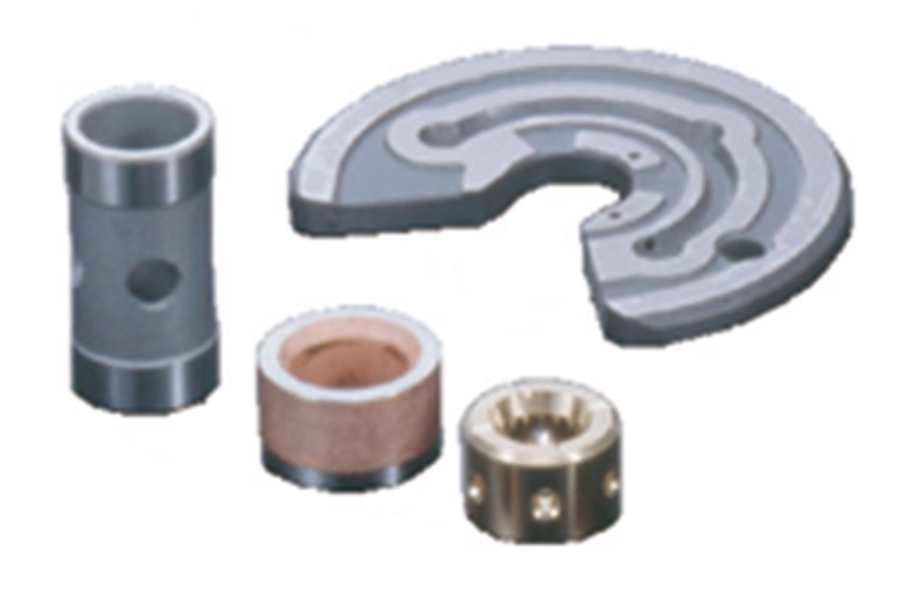
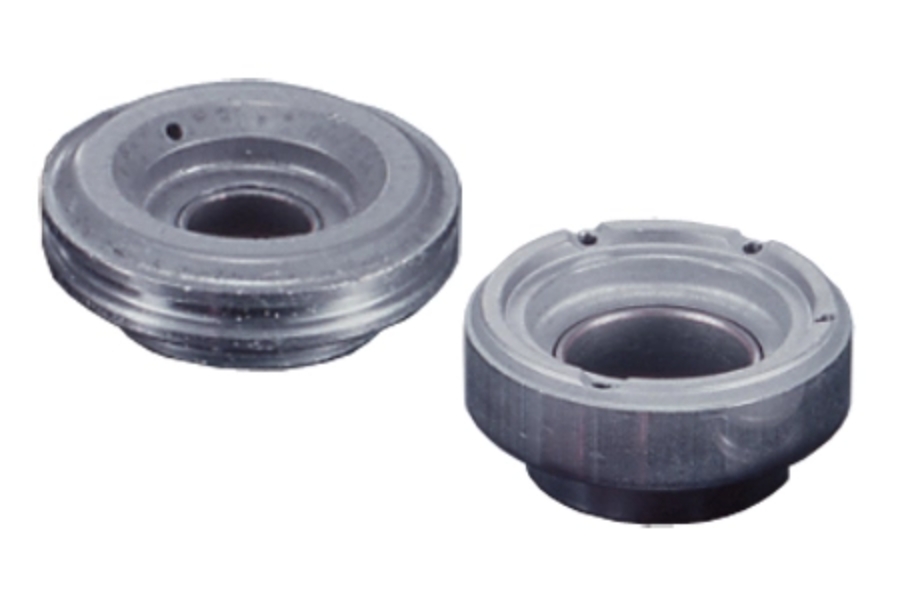
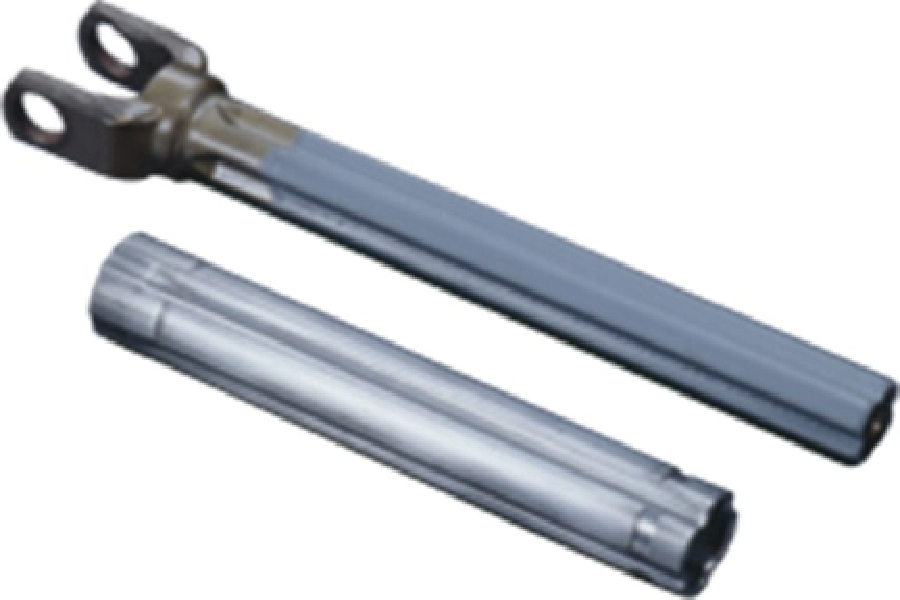
![[PA100]紙送り機用ローラー](/assets/media/2023/04/img-tribology_history-15.jpg)
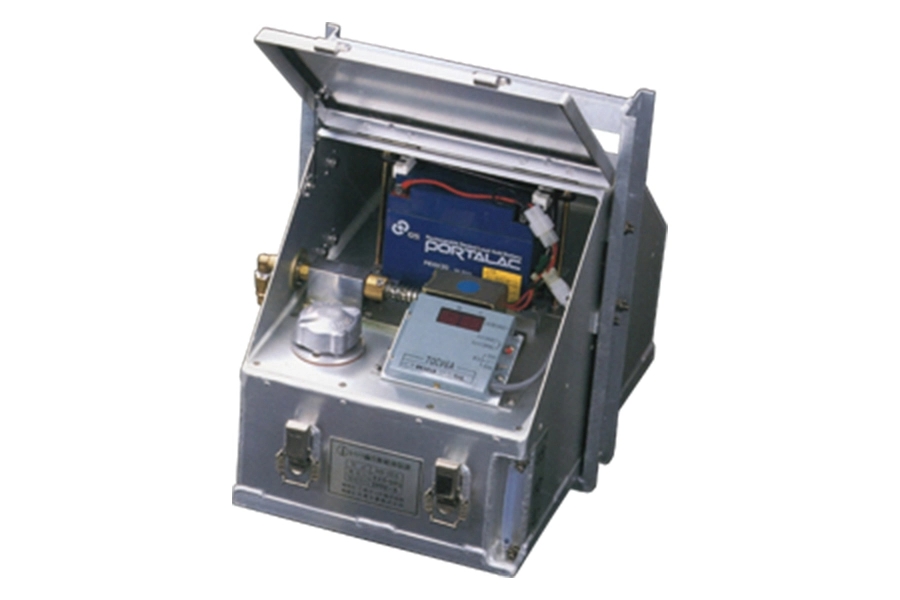
エンジンベアリング一貫生生産体制確
1985年、細谷工場でアルミニウム合金エンジンベアリングの一貫性生産体制を確立した。 このころエンジンベアリング材料の主流がアルミニウム合金へと変わろうとしていた。この需要増に対し、既存ラインの改善だけでは対応が難しく、ライン構造自体を見直す大規模な整備に取りかかった。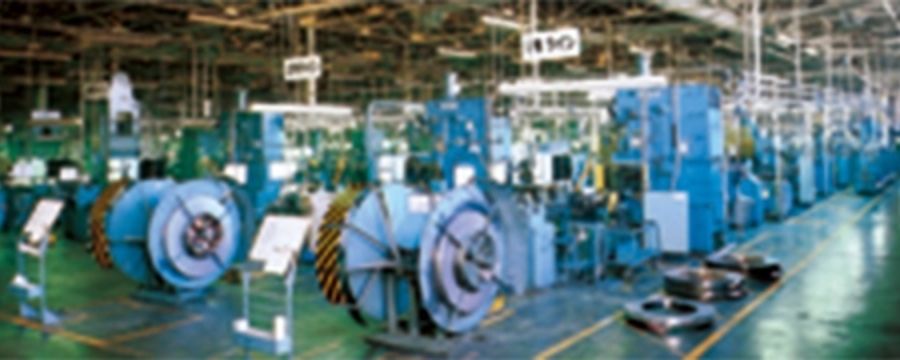
コンプレッサ用軸受のパイオニアとして
1980年年代は、使用環境に合わせさまざまなタイプのカークーラコンプレッサが開発された。 当社でも1980年には、アルミニウム斜板用にすべり面と球体を一体化した「半球シュー」を開発、軽量化に貢献した。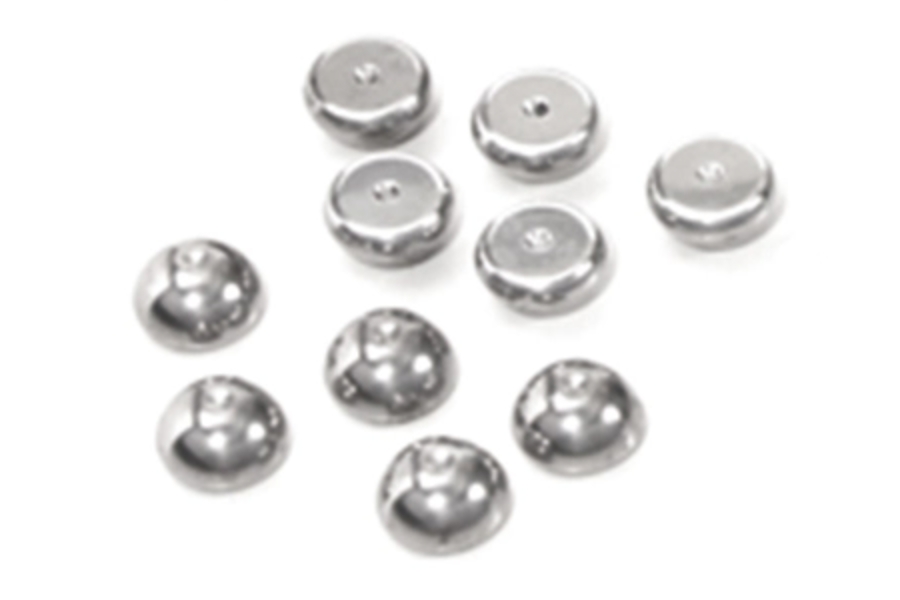
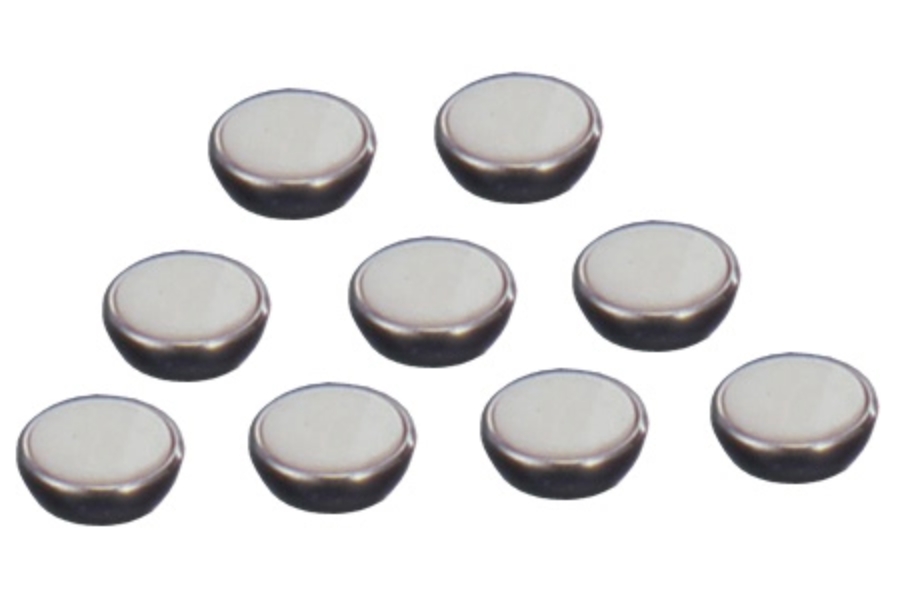
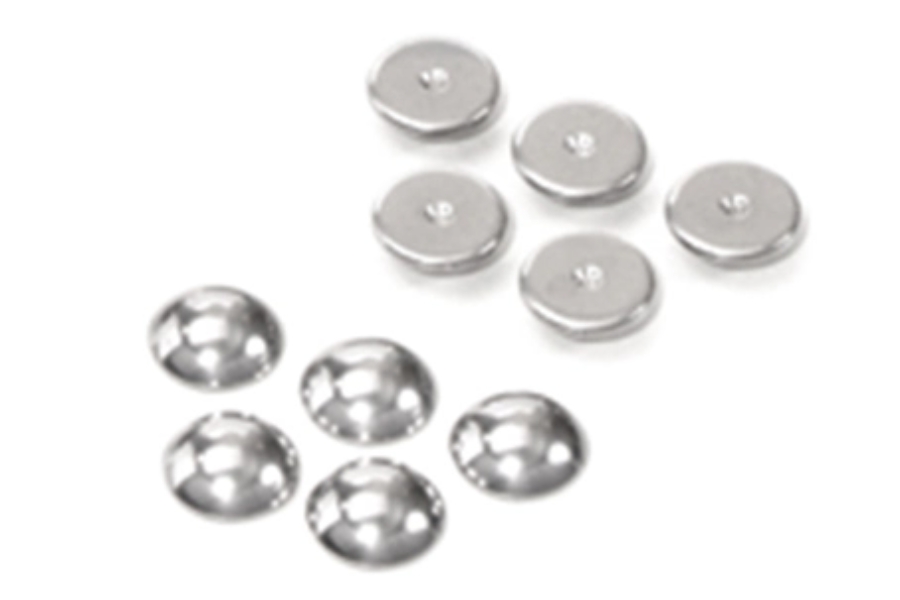
![ボロン処理ベーン[BS100]](/assets/media/2023/04/img-tribology_history-21.jpg)
![[BS100]](/assets/media/2023/04/img-tribology_history-22.jpg)
![[CB100]](/assets/media/2023/04/img-tribology_history-23.jpg)
1989年~2000年
常識を覆したマイクログループベアリング
1989年、トヨタレクサス(セルシオ)用エンジン1UZ-FE型 (4000cc V型8気筒 DOHC 最高出力260PS 最大トルク36.0kg·m)に、当社が開発した「マイクログルーブベアリング」が採用された。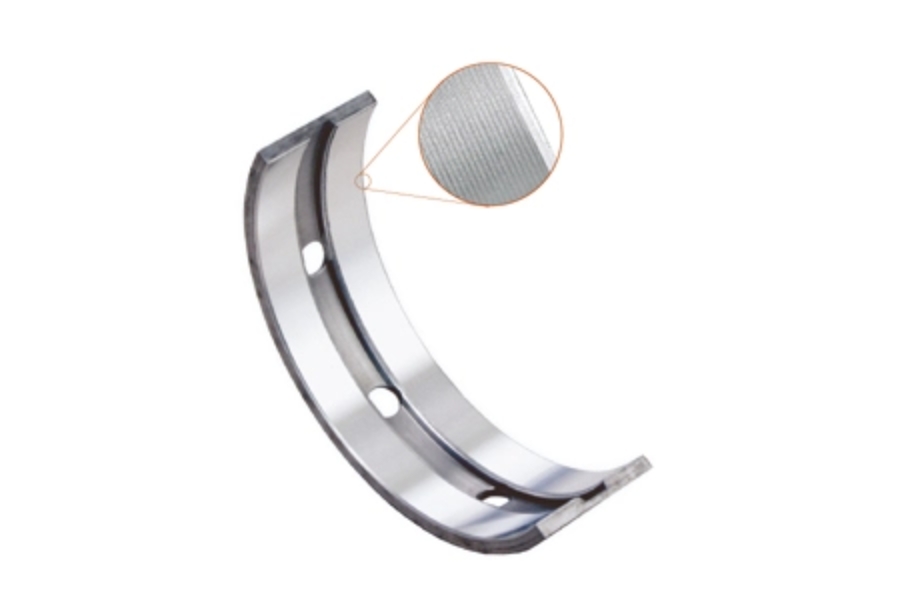
1980年半ばから、自動車にはこれまで以上の高出力化に加え「快適性」「安全性」「静粛性」が強く望まれるようになっていた。その中でもレクサスは、あらゆる面に最新技術を投入した「最高の車」づくりを目指していた。 こうしたニーズに応えるため当社では、開発パートナーとしてデザイン・インを一歩進めたコンセプト・インの姿勢でエンジンの企画段階から参加、付加価値の高い技術提案を目指した。 その結果、低温時の始動性やアイドリングから中・高速走行時のエンジン音、性能の維持(耐久性)に至るまで細部に亘り徹底的に検討した結果、軸受のすべり面全体に極めて細い溝を儲けるといった発想が生まれた。エンジン停止時にもこの溝に油を残し、始動により早く安定した流体潤滑状態に移行できるようにしたのである。これはすべり軸受の「すべり面は滑らかであるべき」とした今までの常識を覆すものだった。
また、この溝は始動性だけでなく、なじみ性、荷重の変化による打音などにも好影響をもたらした。 さらに、始動時の良特性はエネルギーロスを抑え、軽自動車用低出力エンジンに対しても有効で、その後開発が進んだ低燃費エンジンにも広く採用されていく。 フレキシブルな発想から生まれた「マイクログルーブベアリング」は、1996年に日本トライボロジー学会「技術賞」をはじめ、さまざまな賞を受賞、当社のトライボロジーのレベルの高さを世界に知らしめることになった。
技術標準の設定とデザインガイドの発行
1992年1月、「エンジンベアリング&クランクワッシャ」と「ブシュ&ワッシャ」のデザインガイドが完成した。 これまではFM社のデザインガイドを翻訳して流用していたが、設計思想や材料開発、製法など、当社独自の技術革新が進み、様々な不具合が生じてきていた。 そこで、社内標準となる“大豊工業技術標準(製品設計技術標準)”を設定し、設計の確からしさとスピードアップを図ると共に、後継者への技術伝承ツールとした。
さらに並行して、この技術標準から要素を抜粋し、社外展開を目的とした「デザインガイド」を発刊した。 当時、自動車エンジン用すべり軸受に関する潤滑理論から軸受設計、トラブル事例、要因解析などを一貫して掲載する専門書は存在しておらず、当社が独自で構築した実践的な軸受技術をまとめたこのデザインガイドは客先にも好評だった。 これにより「軸」側の条件が前提だった軸受設計や材料選択に対し、「軸受」側の要素に関しても客先技術者の意識が高まり、軸と軸受周辺の全体での最適設計を目指す当社のデザイン・イン姿勢が客先と新しいのコミュニケーションを生むこととなった。
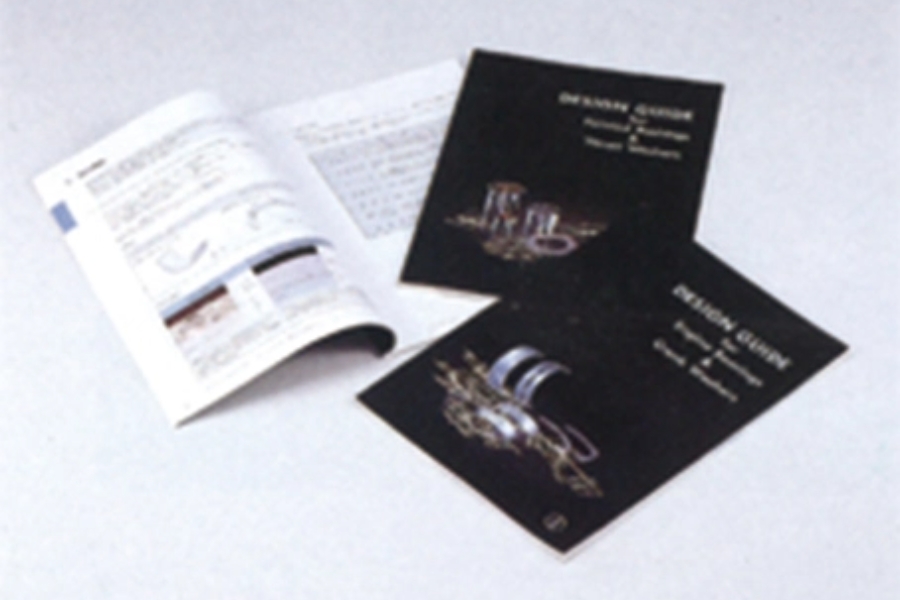
瞬時に8000rpmのレスポンスに対応
1992年、ホンダNSX用エンジンC30A型(3000cc V型6気筒 DOHC 最高出力280PS 最大トルク30kgf・m)に当社が開発した「LN762/HD240」が搭載された。NSXのエンジンはアイドリング状態から瞬時に8000rpmまで立ち上がる。![[LN762/HD240]](/assets/media/2023/04/img-tribology_history-26.jpg)
トヨタ「技術開発賞」
1994年1月、長期間使用での信頼性を大幅に向上させた「TN300/SA151」が、トヨタ「技術開発賞」を受賞した。![[TN300/SA151]](/assets/media/2023/04/img-tribology_history-27.jpg)
「技術本館」が担うもの
1998年8月、細谷工場内に摩擦技術研究センターと結ぶ形で「技術本館」が完成、「技術の生産工場」として位置づけられた。 技術本館では新製品の生産準備、品質管理までを収容し、基礎研究から出荷にいたるまで実践的で具体的な管理ができるようになった。さらに、開発・設計段階でのIT化や、各種実験・測定をフレキシブルに行うことができるスペースや設備などを充実させ、少しでも気になること、疑問に思うことを早期解決できるようになっていた。 これによりトライボロジーをコアとし、その応用や、フィードバック、さらにはコラボレーションの可能性が高まり、ノウハウを構築するのではなく創造するという姿勢で「技術の生産工場」を成立させていくことになる。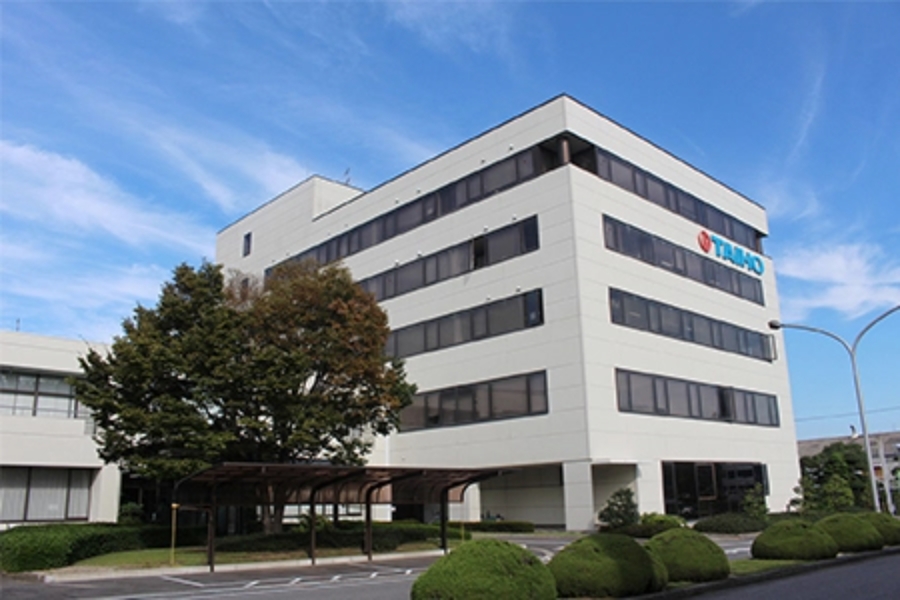
鉛からの呪縛から離脱した高性能軸受
約160年の昔から、「金属製のすべり軸受に鉛は不可欠」という定説があり、技術者はその呪縛から逃れられなかった。 しかしエンジンの小型・高出力化が進むと軸受には高い負荷がかかり温度も上昇、鉛の特性を生かせる環境ではなくなる。 急速に小型・高出力化するエンジンに対し、当社技術者は意を決して鉛からの離脱を決意、未知の技術に挑戦することとした。 高速・高負荷対応の軸受には銅鉛合金を用い、さらに合金特性を補助するために鉛やむすずめっき(オーバレイ)を施すことが一般的で、合金・オーバレイともに鉛が使われていた。 この2つの鉛フリー化にあたって、2つが補完し合って性能を維持するのではなく、両方ともに最高の性能を持たせ、それを組み合わせることで更に上の性能を目指した。
こうして1997年に完成したのが、固体潤滑オーバレイ[RAシリーズ]、銅合金[HB・HSシリーズ]、翌年にはアルミニウム合金[SAシリーズ]も加わり、世界に先駆けて鉛フリー軸受を実用化することができた。 ELV指令最初の法案発表と同じ年であり、2000年以降で施行されていく環境負荷物質撤廃の流れとは一線を区くものであった。 1998年、国内メーカーの欧州向けディーゼルエンジンに採用され、2002年にはその性能が認められ「技術開発賞」を受賞、その後も、学協会から多くの賞を受賞している。 固体潤滑オーバレイ[RAシリーズ]はアルミニウム合金軸受にも適用でき、高出力エンジンの合金選択肢にアルミニウム合金を加えることができるようになった。
2003年には、RA520/SA250が欧州大手自動車メーカーの高出力エンジンW12(6050cc W型12気筒 最高出力450PS 最大トルク57.0kgm)に採用され、「このベアリングが無かったら、W12は量産できなかったであろう」という意図のコメントを聞くことができた。![W12用[RA520/SA250]](/assets/media/2023/04/img-tribology_history-29.jpg)
TTRF設立とトライボロジーとの関わり
2000年10月、当社が東証・名証へ上場したことを記念して、「大豊工業トライボロジー研究財団:TTRF」を設立した。 当社はトライボロジーという言葉が成立する以前より、すべり軸受の開発・生産を通し、摩擦・摩耗・潤滑に携わっており、今後はトライボロジストの育成・支援を含め、さらにトライボロジーとの関わりを深めて行くことになる。 また、2011年には当社技術顧問の熊田善生(元専務取締役)が、社団法人日本トライボロジー学会の会長に就任したことも、当社とトライボロジーとの深い関わりの証として特筆すべきことといえる。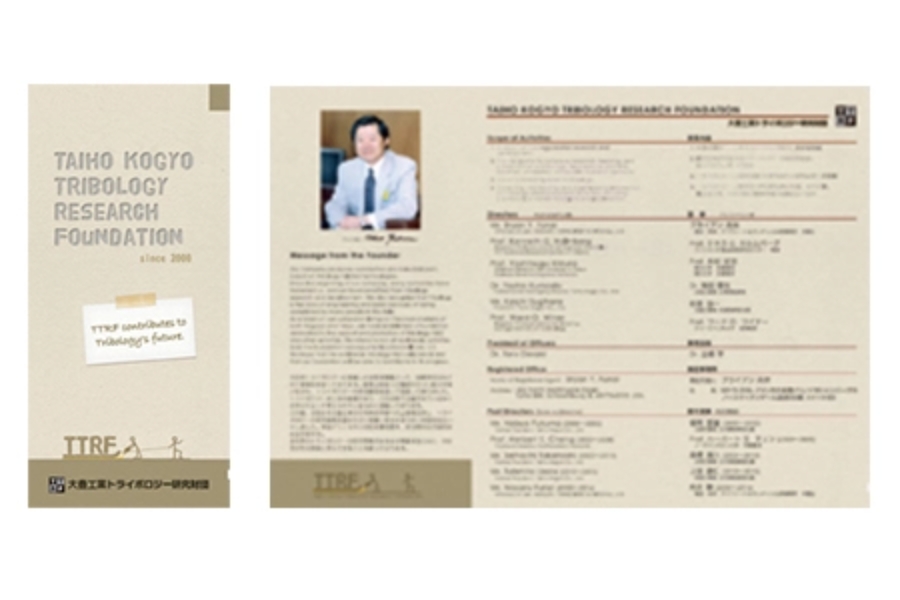
2000年~
要素技術からシステムへ
当社はこれまで、軸受という観点から潤滑を追求してきており、ハード・ソフト面でさまざまな技術を構築してきた。 近年の低燃費エンジンは新しい仕組みや機構が用いられ、その多くは油圧を利用している。 エンジンにおいて軸受は1つの要素部品であり潤滑を必須としているが、エンジン全体の潤滑のに与える影響も大きい。この観点で、軸受部での油量削減を目的とした偏心溝ベアリングや、油路内の異物排出機能付きベアリング、I穴クランクシャフトなど、軸受に新たな機能を持たせる設計が始まった。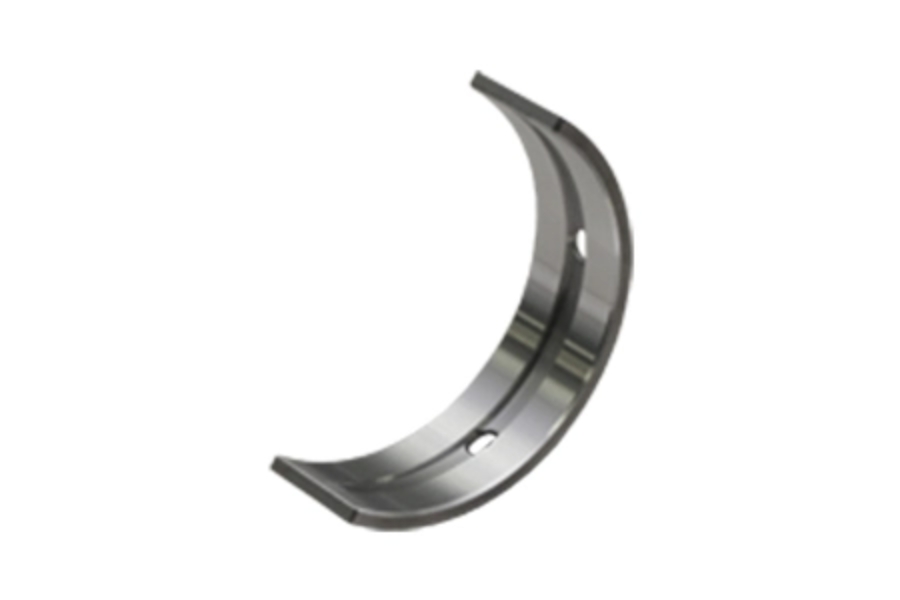
エコエンジンへの対応
クリーンディーゼル、過給ダウンサイジング、ハイブリッドシステム、さらにそこで使用される補機にいたるまで、当社のトライボロジーを生かす領域はますます拡がっていく。 ディーゼルエンジン用に高速・高荷重下での耐焼付き性の向上と、異物混入時や片当たり発生時でも十分な性能を発揮できる、銅合金軸受[BP100/HI100]を開発、2013年に欧州メーカーに採用された。
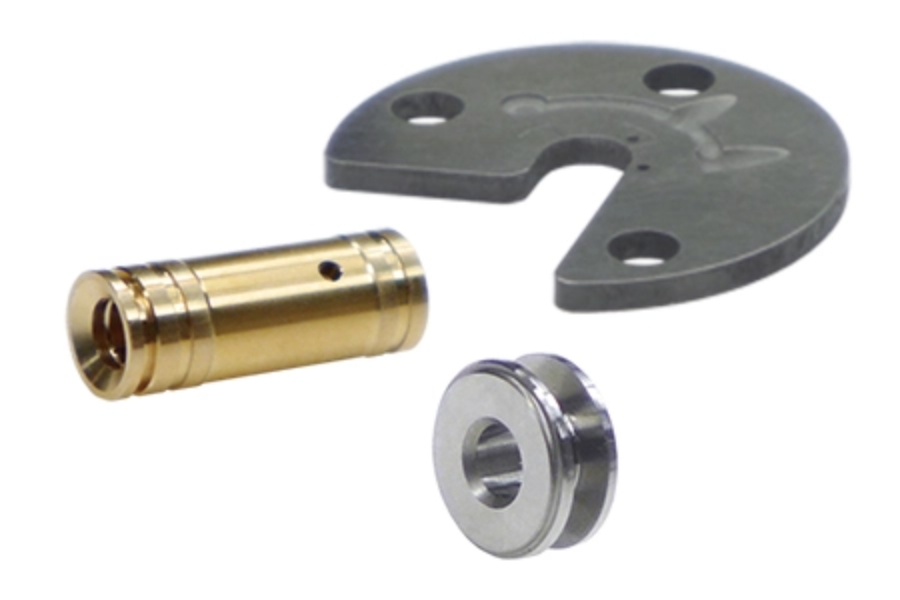
![[CB600]](/assets/media/2023/04/img-tribology_history-34.jpg)
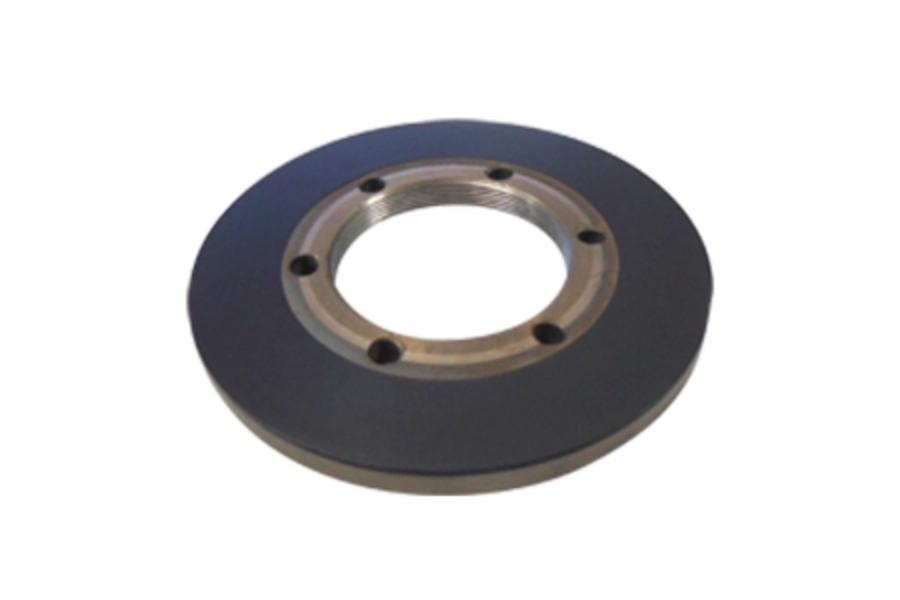
![[RC100]](/assets/media/2023/04/img-tribology_history-36.jpg)
異物対策で軸受のロバスト性を向上
2009年、異物排出機能をもったコンロッドベアリングが完成した。軸受の鉛フリー化やエンジンの高性能化にともない、油膜厚さの減少や軸受の高強度化が進み、軸受部に侵入した異物による焼付きの可能性が高まっており、「耐異物性」は軸受にとって重要な性能の1つとなっていた。 これまで、自動車メーカーでは異物混入防止策や異物管理規格などの面で、軸受メーカーでは軸受材料の改良による耐異物性を向上させるなどの対策を図ってきたが、2007年から新たなる発想として、コンロッドベアリングの油穴に到達した異物を、摺動面を通すことなく排出させるという軸受部でのロバスト性を重視した開発を進めることとなった。 具体的には合わせ面の面取り深さを調整し異物を補足、さらに異物が摺動面に移動しようとした際の障害となるようにクラッシリリーフの長さや角度を見直した。 この設計数値の変更は流体潤滑時の油圧低下や合わせ面の座屈などのリスクを考慮し、試験機を改造して可視化装置を作るなど、実際の流れを確認しながら最適値を求めていった。 その結果、軸受材料を変えることなく寸法の変更だけで異物排出性を向上でき、油圧低下よるエンジンへの影響もごく僅かで、異物排出効果の貢献度の方が高いすべり軸受が完成、この技術はエンジン側の改良や生産設備の変更の必要がなく、受け入れやすい技術革新となった。軽量シューの開発とグローバル生産
代替フロンなどの環境対応を経て、クーラコンプレックスはさらに高性能化しており、斜板は耐焼付き性の向上のため摺動面に樹脂コーティングを施すことが多くなってきた。 シューは圧縮工程後の吸引工程から次の圧縮工程に移行する時、自重によって発生する慣性力によって、斜板面を叩き、樹脂コーティング層の摩耗を増大させており、斜板の耐久性を向上させるには、シューの重量を軽くして、往復運動時の慣性力を弱めて斜板面への衝撃を軽減することが必要だった。 シューの軽量化には、素材の軽量化や、内部の中空化などの方法があったが、既に他社特許があり当社では採用できなかった。そこで当社ではシューの本質を見直し、設計レベルで軽量を実現化する道を選択した。 現状のシューの球面において、ピストンの球面と接触しているのはシューの球面部の一部分であり、その他の部分(球面の裾部分)は機能的な役目を果たしていないことに着目、この部分を除肉することによって軽量化する設計としたのである。
この設計は、従来とほぼ同じ設備、工程での量産が可能であるという利点もあった。 シューは当社のトライボロジー技術を活用した特殊軸受であり、1996年の北米TCAからはじまった世界戦略の主力製品となっており、2001年の韓国TCKでの生産開始まで、熟成された設備で、性能・品質を維持できる大豊グルーブのグローバル生産の要として、カーエアコン用コンプレッサの高性能化に寄与している。
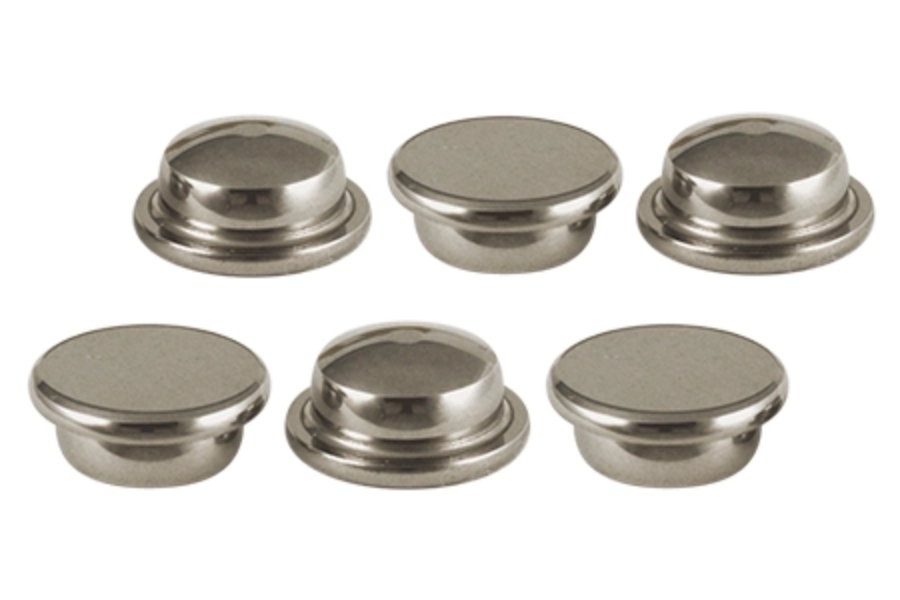
大豊トライボロジーを世界へ
2012年に細谷工場で稼動したRR(良品・廉価)メタルラインを、PTN(インドネシア)、TCY(中国)へと展開、細谷工場をマザープラントとし、海外での本格的な生産がはじまった。 トライボロジーをコアに、軸受技術と生産技術のコラボレーションで生まれたこのグローバルラインから、大豊ブランドエンジンベアリングの世界的競争力を高めた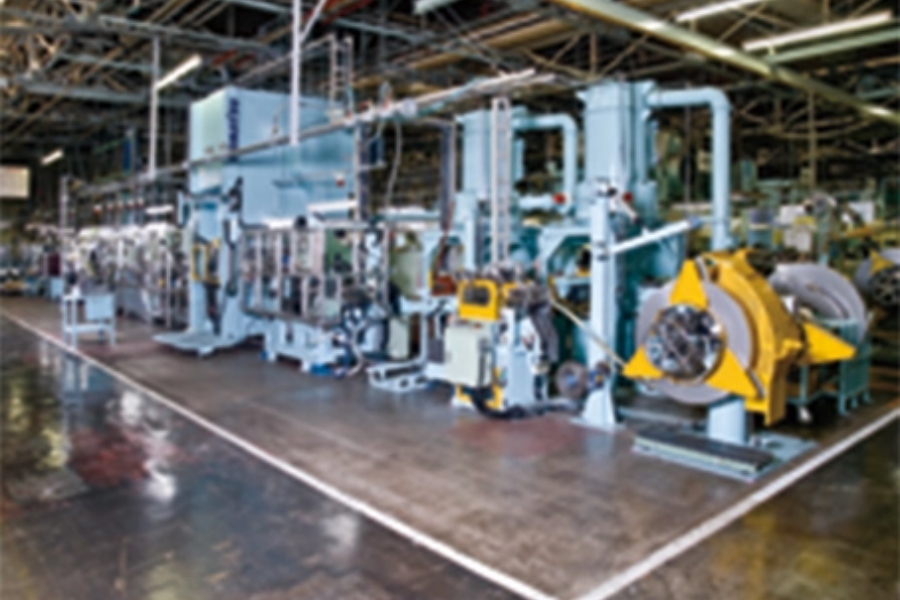
冷間摩擦低減技術を新化--細溝付き軸受
1997年に本格に量産が始まったハイブリッドシステムや、比較的導入が容易なアイドリングストップシステムが幅広い車種に採用されるようになった。これらのエンジンの特徴は頻繁に始動と停止を繰り返すことで、一般的なエンジンに比べ暖機に要する時間が長くかかる。これにより潤滑油も暖まり難く、適温になるまでの間、軸と軸受の摩擦が大きくなってしまう。 流体摩擦の低減には、軸受の幅狭化など摺動面積の低減が考えられるが、そこには物理的な限界や制約があった。 そこで従来技術の延長ではなく、まったく新しい技術で冷間時の摩擦低減技術の開発に着手、この開発における基本的な考え方を、「潤滑油の早期昇温」とし、様々な手段を検討・検証した結果、油膜のせん断発熱の積極的利用に搾り込んだ。 開発のポイントは、油膜のせん断発熱を有効に利用するため、冷間時の漏れ油量の低減を図りながらも、高回転、高負荷時の信頼性を損なわない構造とすることだった。
開発当初、軸受から漏れるオイルをシールリングによって塞き止める方法を検討したが、リング剛性や組付け性に課題が残り、試行錯誤したももの開発を断念せざるをえなかった。 次の手段として、油膜内に発生する負圧の利用に着目した。ロアベアリングにおける軸の回転方向下流で僅かに生じる負圧によって、軸受の外側からオイルが吸い戻されていることが計算で明らかになっており、この「吸い戻し作用」を増強して漏れ油量を低減、さらに油膜のせん断発熱で暖まったオイルを再循環させることで、早期昇温が可能と考えたのだ。 この「吸い戻し作用」を増強には、負圧を増加させる機構をロアベアリングに付加する必要があった。
早々、形状設計、3D-CFDによる計算および可視化実験で検証を繰り返し、ロアベアリング上で、すきま形状が末広がりになる領域(逆くさび域)の両端に細溝を施したロアベアリングを2014年に完成させた。 この細溝部で負圧が増加され「吸い戻し作用」が増強される。また懸念された高温時の信頼性も確保でき、2015年秋から量産されことになった。 2011年4月1日以降に発売された新型車は、JC08モードによる燃費測定が義務付けられた。これまでは完全暖気状態で測定していたのに対し、JC08モードは暖気前から測定を始める。 暖気前のエンジンは排気ガスは濃く、燃料消費も多い。 これは、ハイブリッドやアイドリングストップシステムに限らず、一般的なエンジンにおいても完全暖機状態になるまでの燃費向上が求められていることを示しており、「冷間摩擦低減技術」の重要性が増した。
次世代のエンジニアリングへ
戦後の動乱期に自動車メーカーや海外軸受メーカーからの技術導入に頼り「軸受メーカー」として出発した当社だが、日本経済の発展とモータリゼーションに追従しつつ、産学協同でトライボロジーをコアとした独自の技術を構築、様々な課題を克服してきた。これは日本の自動車産業発展の一翼を担ってきてといっても過言ではない。 18世紀後半の産業革命においてエネルギー損失が話題となってから今日まで、摩擦・摩耗の低減には様々な人が関わり知恵を出して課題を克服してきた。当社のエンジニアもその中の一人である。
当社設立の約20年後に「摩擦・摩耗の現象を解き明かす科学技術」として「トライボロジー」という言葉が使われはじめ、今では地球規模の環境改善、省エネルギーのキーテクノロジーとして位置づけられ多くの産業分野において重要な役割を担っている。大豊エンジニアは今後、トライボロジーの原点を見失うことなく技術革新を目指すものである。