軸受
軸受は回転または往復運動をする軸を支えるとともに、軸に作用する荷重を支えて、円滑に作動させるための機能部品です。軸受はその構造から「すべり軸受」と「ころがり軸受」に大別されますが、エンジンのクランクシャフトを支える半割り形のエンジンベアリングやクランクワッシャは、すべり軸受を代表するものです。
すべり軸受ところがり軸受
すべり軸受は平軸受とも呼ばれ、通常、摩耗面に潤滑油が存在することを前提として用いられます。軸の回転とともに、軸と軸受のしゅう動面隙間に潤滑油の油膜が形成されると、摩擦係数、摩擦損失がころがり軸受よりも遥かに小さくなるという特徴があります。また、油膜の形成により軸と軸受の固体接触を避けることができ、振動・同音を吸収するとともに、容易に大きな負荷を支えることができます。ころがり軸受に比べて周速・負荷容量・軸受剛性・静粛性・寿命・軸受容積・組付けの簡便性など、軸受に求められる諸特性は優れており、エンジンの軸受はすべり軸受が主流を占めています。ただし、すべり軸受の特性を活用するためには、潤滑法に細心の注意を払い、周辺部品の寸法精度、特に幾何公差の精度を高く保つ必要があります。
![すべり軸受ところがり軸受の形状[外径・幅寸法]比較](/assets/media/2023/04/img-sliding-1.jpg)
ころがり軸受の起動時の摩擦抵抗は、すべり軸受に比べて小さい値を示します。また、一つの軸受でラジアル、スラストの両荷重を支えることができる特徴があります。 さらに、形状・寸法・精度が国際規格で統一されているうえに、グリース潤滑が可能で潤滑方法についての制約が少ないため、一般に広く利用されています。一方、構造上から振動・騒音が発生しやすく、また、衝撃荷重に弱く、高速・高荷重で使われるエンジン用軸受としては不向きであるといえます。さらにすべり軸受に比べ、軸受幅[軸受の軸方向寸法]の寸法が小さい利点があるものの、外形寸法が大きいことと、分割が難しく多気筒エンジンのクランクシャフトにはほとんど組付けが不可能で、一部の単気筒エンジンのベアリングとして用いられているにすぎません。
エンジンベアリング・クランクワッシャ
エンジンベアリング、クランクワッシャの使われている場所
(1) エンジンベアリング
メインベアリング(ジャーナルベアリングまたはクランクシャフトベアリングとも呼びます。以下、メインベアリングを用います)とコネクティングロッドベアリング(ピンベアリングまたはコンロッドベアリングとも呼びます。以下コンロッドベアリングを用います)を総称してエンジンベアリングと呼びます。
メインベアリング
シリンダブロックのハウジングボア(以下、ハウジングを用います)に装着して、クランクシャフトのジャーナルを把持し、クランクシャフトを支える軸受。
コンロッドベアリング
コネクティングロッドのラージエンドボア(以下、ハウジングを用います)に装着して、クランクシャフトのピンを把持し、コネクティングロッドを支える軸受。
(2)
クランクワッシャ(スラストワッシャ)
メインベアリングと組み合わせて用い、クランクシャフトとシリンダブロックの軸方向位置決めと、クランクシャフトのスラストを支える軸受。
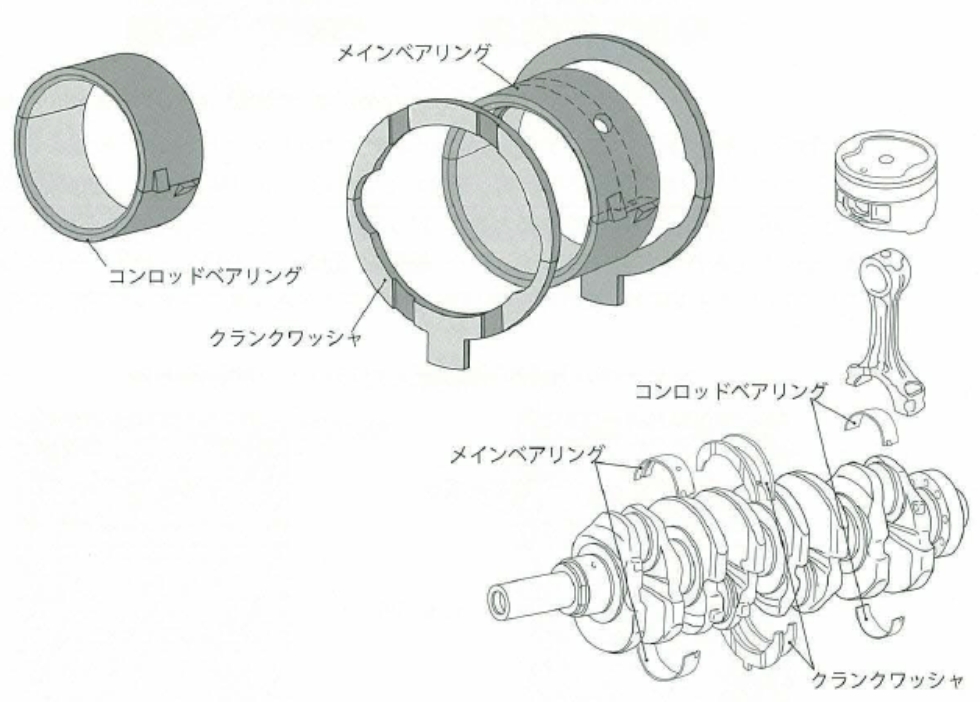
メインベアリングには組付け上の便利さからクランクワッシャとメインベアリングが一体となった、下図のようなフランジベアリングが使われることがありますが、フランジ部の当たり精度の問題や曲げ部の折損などの信頼性不足から、現在ではほとんどのエンジンにクランクワッシャを別体にしたセパレートタイプが採用されています。
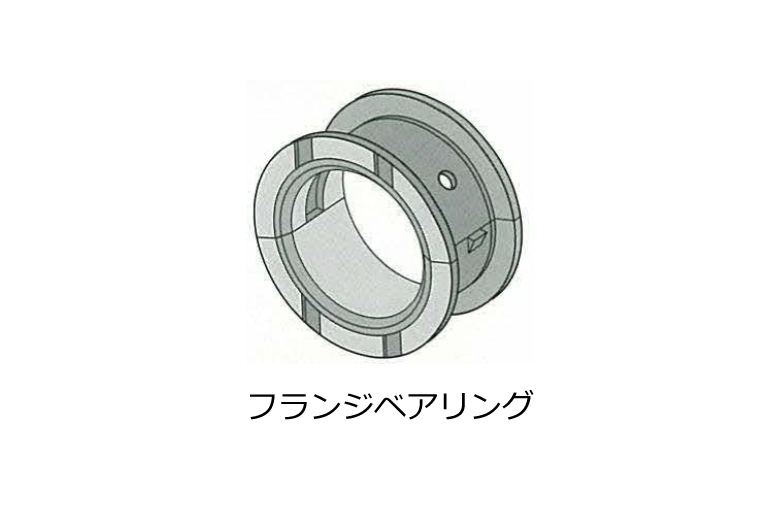
すべり軸受と潤滑
すべり軸受は、軸と軸受との間にわすかな隙間を設け潤滑油を供給し、軸の回転に伴って油膜をつくり、この油膜で軸を支えて金属相互の直接接触を避けます。このとき油には油膜圧力と呼ばれる圧力が発生します。この圧力によって軸にかかる負荷を支えます。この荷重を支える能力を負荷容量といいます。
エンジンベアリング内の油膜圧力発生のメカニズムと負荷容量
一般のすべり軸受では、相対するすべり面の間に潤滑油を挟み、外力を受けながら相対運動をします。この時潤滑油は粘性流動を起こし、それに伴って潤滑油中に発生した粘性抵抗につり合う油膜圧力が発生します。
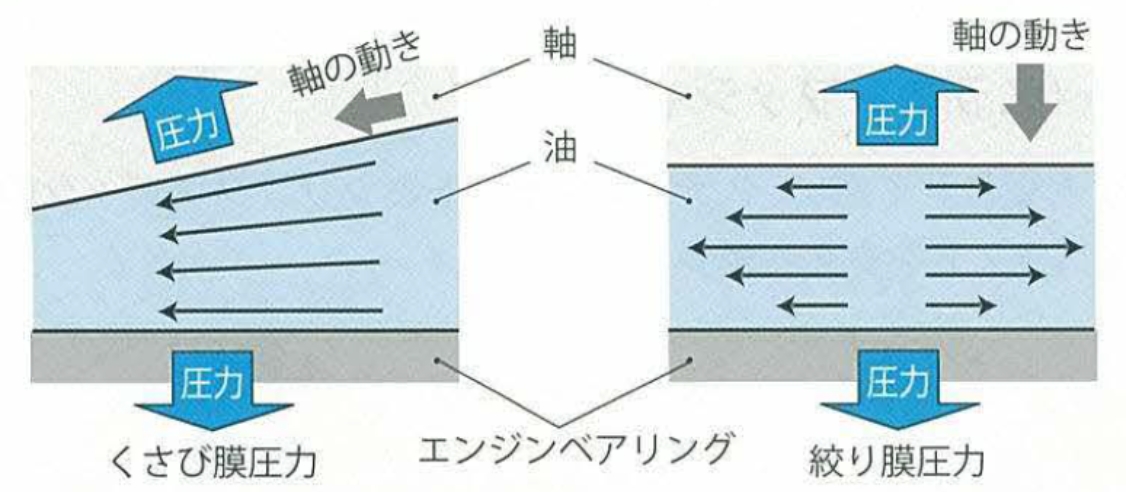
すべり軸受は、軸と軸受の間にわずかな隙間を設けて軸を回転させるので、隙間を満たした油が軸の回転につれて先細りの空間に引きずり込まれるときの「くさび膜圧力」と、軸が軸受のすべり面に接近して隙間が時間とともに狭くなる時の「絞り膜圧力」が発生します。これらが組合されて、すべり面に働く外力を支える力、すなわち、すべり軸受の「油膜圧力」を発生させることになります。この時の「くさび膜圧力」「絞り膜圧力」それぞれの圧力分布形態のモデルを下図に示しました。
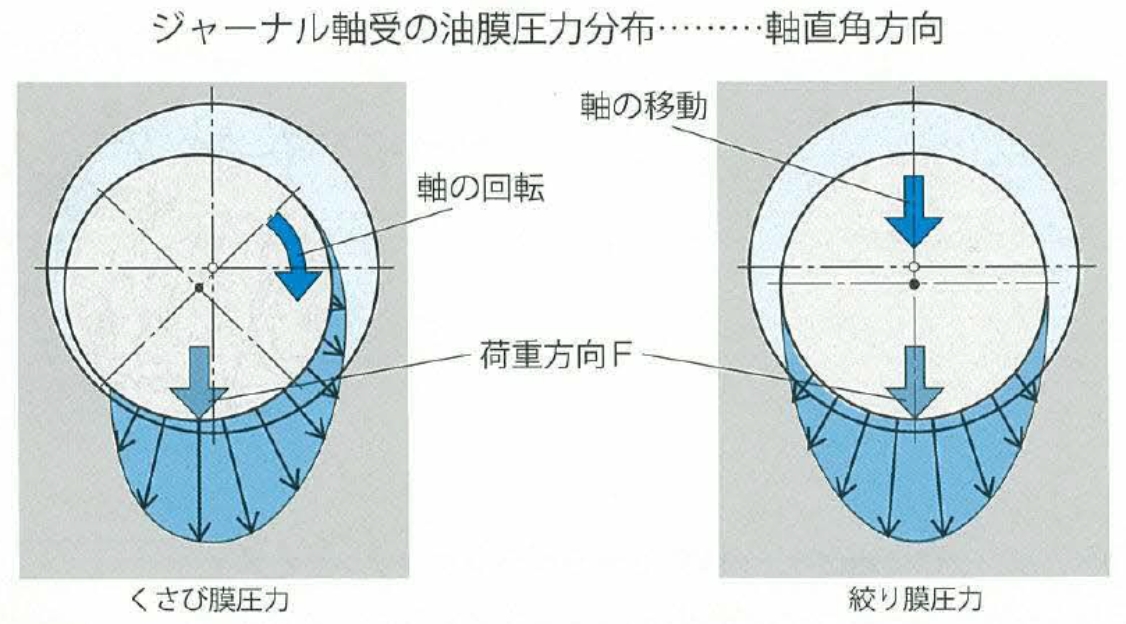
実際のエンジンのクランクシャフトには複雑に変動する力が加わります。その変動する力につれてクランクシャフトの軸心は軸受内で絶えず移動するため、上図のような単純な圧力分布を示すことはありません。
このような理由からクランクシャフトの正確な作動解析をして、負荷容量を知る必要があります。
エンジンベアリングの潤滑
クランクシャフトとエンジンベアリング間に適切な給油状態が保たれているとき、停止から定常回転に移るまでのすべり運動と潤滑油の挙動は、次のような過程をたどります。
(1)
停止しているとき
運転中にシャフトとベアリングのすべり面に介在していた油は、長時間停止している間にシャフトの自重で押し出されています。このじょうたいではクランクシャフトとエンジンベアリングは個体接触をしています。
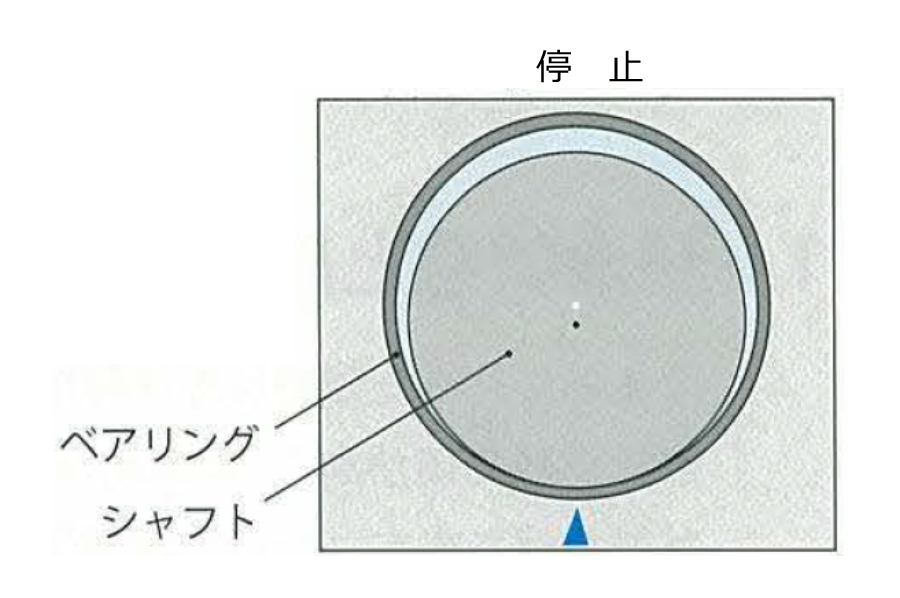
(2)
回転が始まったとき
「境界潤滑」「混合潤滑」
「境界潤滑」「混合潤滑」
このとき同時に給油が始まりますが、接触面への油の到達が遅れたり、たとえ同時に油が届いたときでも給油圧だけではクランクシャフトを持ち上げるだけの力が無いため、金属相互の相対すべりが始まります。やがてシャフトの回転に伴って油のくさび膜圧力が働き、シャフトが浮き上がって接触面に油膜が作られていきます。このように、すべり面は「境界潤滑状態」から「混合潤滑状態」へと移っていきます。
相対すべりが始まるとき、特に境界潤滑状態ではすべり面の平滑さが欠けていると、微小な凹凸での固体接触が起こるため、一様な油膜が形成されにくくなります。また、接触面の表面あらさが粗いときに、この状態を長く続けると激しい摩耗や焼付きなどの損傷に至ることがあります。
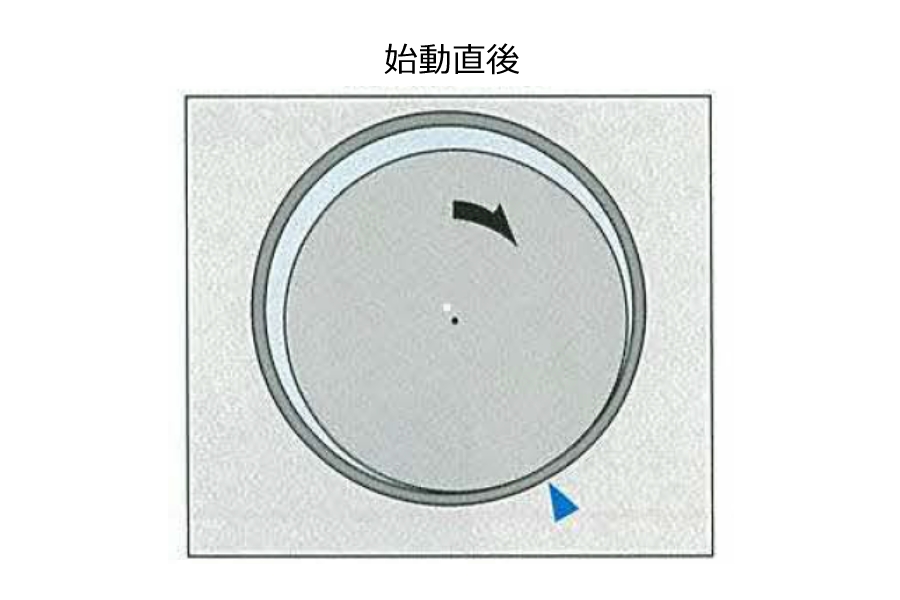
(3) 定常回転になったとき
「流体潤滑」
潤滑油のくさび膜圧力がさらに増加し、流体力学上からみて平衡状態を保ったとき、初めて安定した油膜が形成され、クランクシャフトはエンジンベアリングの表面を離れ、油膜を介しての相対すべり状態、すなわち「流体潤滑状態」での回転になります。
このように、安定した油膜を作って流体潤滑状態を確保することが、すべり軸受では必須の条件となります。このときの油膜の厚さは、クランクシャフトの負荷状態や油の粘度によって様々な値を取り、厳しい使用条件の下では、1マイクロメートル(1μm)以下の値になるため、接触面の表面あらさ・幾何交差には極めて高い精度が要求されます。
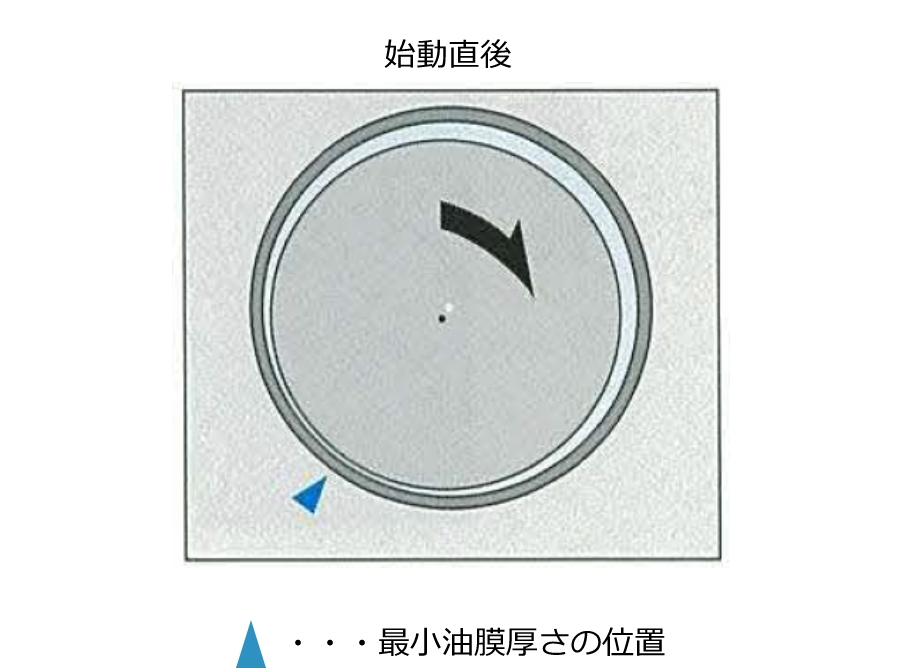
エンジンと流体潤滑
今日のエンジンは急速な技術の進歩により、ますます高性能化されています。その中においてエンジンベアリングが流体潤滑状態を確保して、安定した軸受特性を維持することは、エンジンの低燃費化、静粛性向上、耐久性向上、信頼性向上などに大きく寄与します。
潤滑状態と摩擦の関係
今までに述べた潤滑状態を整理すると下図のようになります。無潤滑と境界潤滑の状態では著しく摩擦係数の値が高く、混合潤滑の状態は不安定な領域であり、流体潤滑の領域で初めて安定した状態を保ちます。したがって、無潤滑、境界潤滑、混合潤滑の領域では、クランクシャフトを回転させるためのエネルギー損失が大きいばかりではなく、軸と軸受のすべり面での固体接触による摩擦熱や摩耗が発生し、やがて重大な損傷に至ります。また、エンジンベアリングの性能は、流体潤滑状態により早く移行し、安定した流体潤滑状態をいかに確保するかが重要なポイントになります。しかし、無潤滑状態と流体潤滑状態の間を縮めることができたとしても、ゼロにすることは到底不可能なため、その間における軸受への影響を最小限に抑える工夫が必要になります。
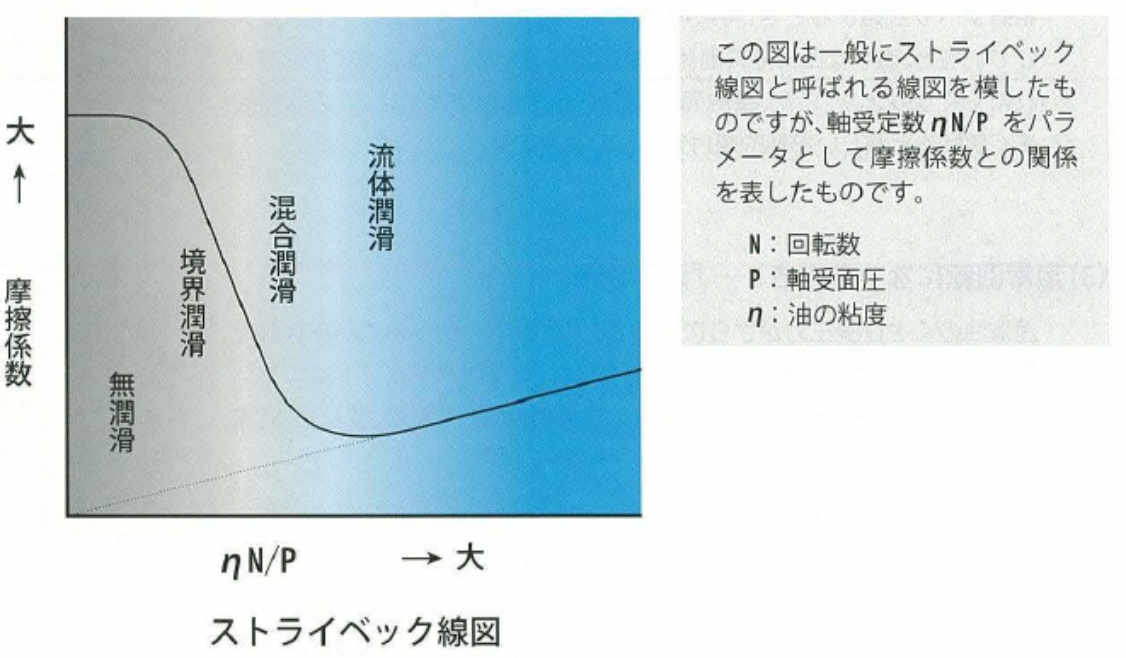
エンジンベアリングに求められる性能
流体潤滑の確保に関しては、十分な油膜形成が必須条件であり、潤滑油の有効な給油や、軸・軸受のすべり面の平滑さ及び相互のアライメントが重要であす。そのため、軸受すべり面の幾何交差は極めて高い精度が要求されます。
弊社ではこの軸受すべり面に極めて微細で精密なみぞを規則正しく配列した、マイクログルーブベアリング[弊社商品名、略称:MGB、特許・商標登録済]を開発し製品に加えました。
その効果は前項のストライベック線図のように、無潤滑状態から流体潤滑状態に至るまでの間を接近させて、流体潤滑状態の早期確保を実現し、軸受性能の著しい向上を図ったものであります。
このマイクログルーブベアリングでは、なじみ性・保油性などの改良による軸受温度低減の効果が確認されており、耐焼付き性・耐疲労性などの軸受性能が飛躍的に向上いたします。
また、オイルクリアランスの値を小さくすることができるので、エンジン騒音の低減効果に寄与することも確認されています。
この軸受は、すでに多くの自動車用エンジンに採用されて効果を認めていただいており、この形式のベアリングは、装着するエンジンや求める軸受特性によってグルーブの深さ(h)とピッチ(P)など選択し、仕様を決める必要がありますので、詳細についてはお問合せください
マイクログルーブベアリングのすべり面の断面
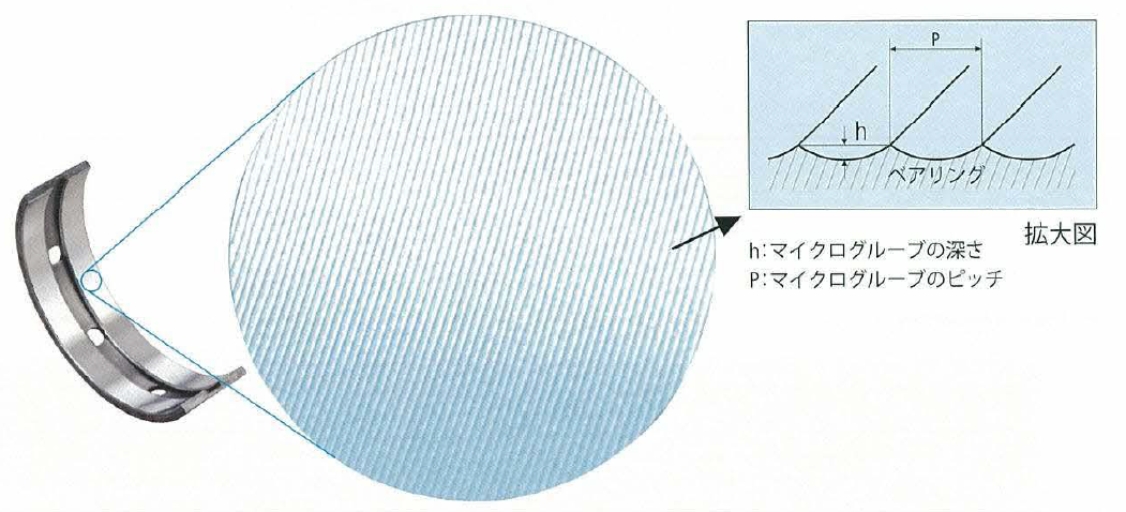
軸受材料
実際のエンジンでは、起動・停止、過負荷、ミスアライメント、変形、異物混入などによって、すべり面の固体接触が避けられない事態が発生いたします。クランクシャフトが静止しているときの、シャフトとベアリングの接触面は殆ど無潤滑の状態になっていますが回転が始まって流体潤滑状態に至るまでの間における、軸受すべり面の損傷を極軽微な状態に留め、また運転中の流体潤滑領域においても大きな負荷、高い湯松圧力や高温下での繰り返し運転に対して十分な耐久性を確保するためには、軸受材料の選択が重要な要素となります。
潤滑経路と潤滑油
流体潤滑を確保する要素としては、軸受自体の性能以外に、潤滑油の確実な供給が必要です。潤滑油は潤滑装置によって強制的に供給されます。この経路に不具合が生じたり異物が混入したりすると、エンジンベアリングは正常な流体潤滑状態を保つことができません。また、潤滑油にはすべり軸受が流体潤滑を確立するための役割と併せて6つの機能を持っており、中でも減摩擦・減摩耗作用、冷却作用、清浄作用は特に重要な機能です。劣化した潤滑油の使用を避けることはもちろん、エンジンメーカーの推奨する油種、グレード及び交換頻度を遵守されることを推奨します。
(1)
潤滑経路
一般的な4サイクルエンジンの潤滑経路(直列4気筒エンジン)
一般的な4サイクルエンジンの潤滑経路(直列4気筒エンジン)
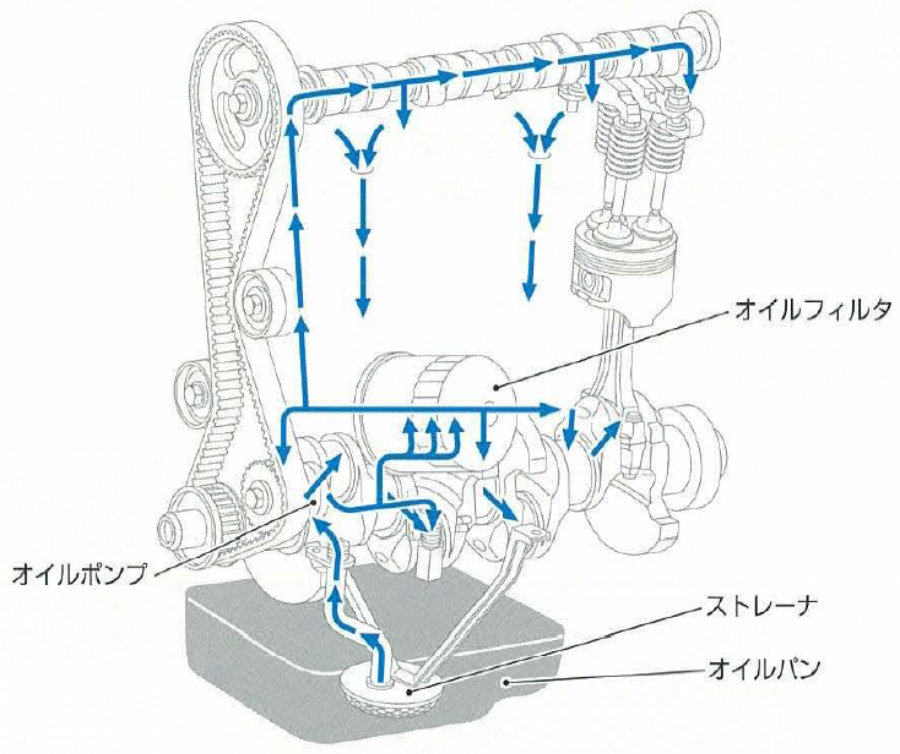
(2) 潤滑油の働き
機 能 | ||
---|---|---|
1 | 減摩擦・減摩耗作用 | すべり面の摩擦抵抗を減らし、流体潤滑状態での適正油膜を保持して摩擦損失を軽減し、耐用年数を伸ばす。 |
2 | 冷却作用 | 油膜中に発生する摩擦熱を持ち去り、温度を安定させてすべり面の焼付き、軸受合金の疲労を防ぐ |
3 | 清浄作用 | 運転中に生成する摩耗粉や、外部からのゴミなどの異物を分散させ洗い流す。 |
4 | 密封作用 | シリンダとピストンとの間を密封し、ガス漏れを防ぐ。 |
5 | 防錆作用 | 錆を防ぎ、寿命を延ばす。 |
6 | 衝撃吸収作用 | 衝撃を吸収し、作動を滑らかにする。 |
エンジンベアリングの設計に必要な要素
実際のエンジンベアリングの設計にあたっては、さらにさまざまな情報を必要とします。このため設計の初期段階から各エンジンの特性に最も適したエンジンベアリングとなるように、エンジンベアリングに及ぼす様々な影響を事前に解析し設計を進めます。 ここでは、エンジンベアリングの設計にあたって、その周辺環境の最適化のために、エンジンで発生する変動荷重の大きさや形態の違いを解説するとともに、特にエンジンベアリングに深いかかわりのある、クランクシャフトの作動解析の実例を紹介いたします。
エンジンベアリングとその関連部位に求められる条件
エンジンの高性能化に伴い、エンジンベアリングの使用条件はますます厳しくなり、以下のことが重要となります。
- エンジンの高速・高荷重による軸受温度の上昇、また、それに伴う潤滑油の酸化・劣化などに対する軸受および潤滑油の耐久性向上。
- 軸受の負荷条件が厳しいときには、油膜厚さが1μm以下と非常に薄い状態で使われるため、軸受およびその周辺構成部品の高精度確保。
以上のようにエンジンベアリングは、周辺構成部品の精度や潤滑法に密接な関係があり。「すべり軸受」そのものを十分に理解して使用したときに、最高の性能が発揮されます。このような状況のもとで、弊社は社内・社外にわたって次のような努力をしております。
社内では
- エンジンベアリングの性能を保証するために、対象とするエンジンごとにクランクシャフトの作道解析を行い、エンジンベアリングの最適諸元を求めたうえで、取り揃えた各種の軸受材料から、それぞれのエンジンに最も適合した軸受材料と寸法・精度を選択します。
お客様に対しては
- 油種、油量及び油温などの潤滑条件を完備していただくようにお願いしています。
- クランクシャフトのジャーナルとピン及びハウジング穴の寸法精度、真直度・真円度など幾何交差の厳密な管理をお願いしています。
- その他、すべり軸受をより良い性能でご使用いただくため、軸受専門メーカーとしての立場から、各種の提案をさせていただいております。
変動荷重の種類
4サイクルエンジンでは、クランクシャフトが2回転する間に、爆発荷重・回転慣性荷重・往復慣性荷重が発生し、これらの荷重が組み合わあされ複雑な変動荷重となって、メインベアリングとコンロッドベアリングに加わります。
その様子をコンロッドベアリングを例にとり、下図に示しました。
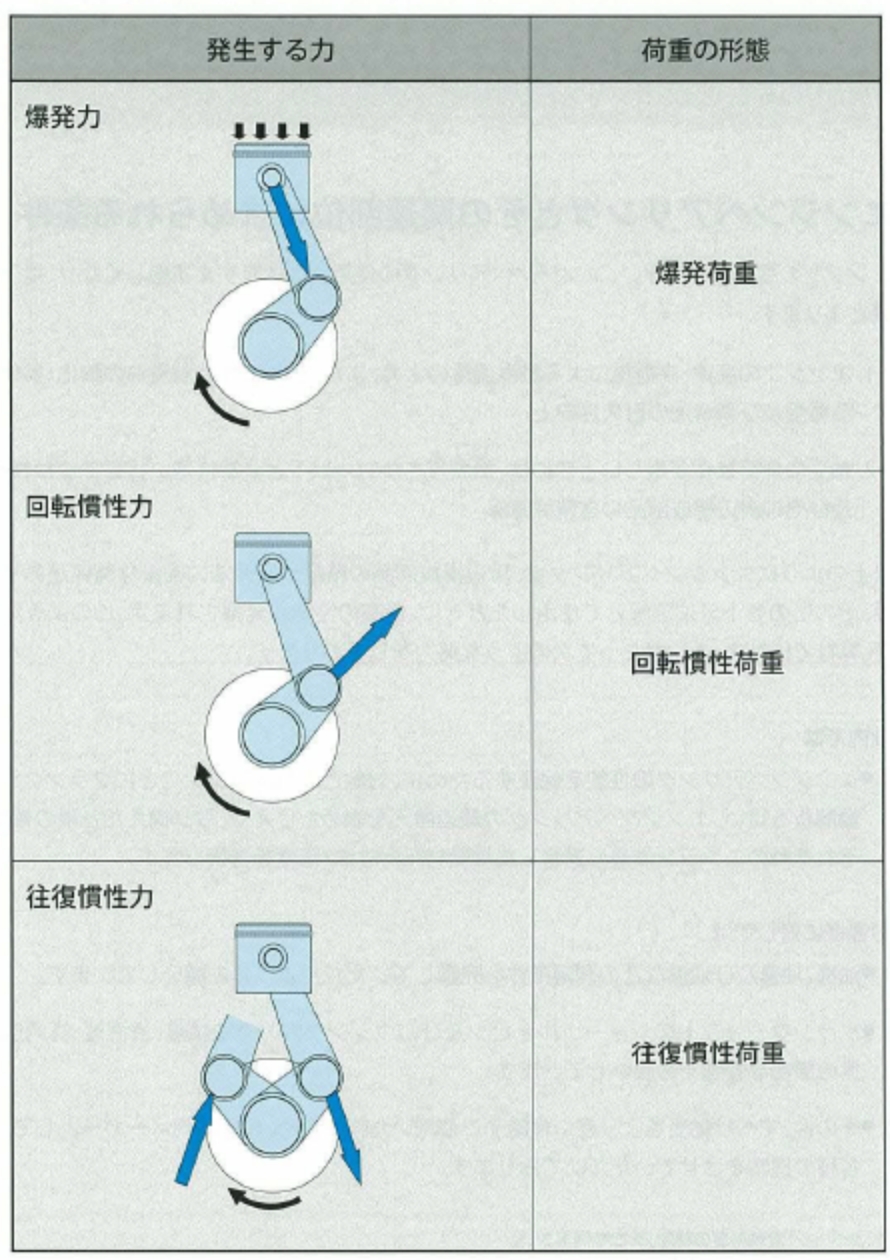
クランクシャフトの作動解析と軸受設計
エンジンベアリングにかかる負荷状態には大きな違いがみられ、作動解析による荷重極線図と軸心軌跡図には著しい変化が現れます。
荷重極線図は、軸受にかかる変動荷重の様相を示しています。ここから最大軸受面圧を求めることができるので、機械的強さを主眼にした軸受材料、特に軸受合金の選択を行うことができます。
軸心軌跡図は、変動する荷重につれてクランクシャフトの軸心が、軸受内を絶えず動き回る軌跡を示すので、最小油膜厚さや、その発生位置を読み取ることができます。
この作動解析で、油膜が薄くなり過ぎて焼付きなどが憂慮されるときには、軸受幅、油穴位置、カウンターウェイト、油温などの改善を行うことになります。
下図は、軸受内面展開上での油膜厚さの分布図及び油膜圧力の分布の例です。
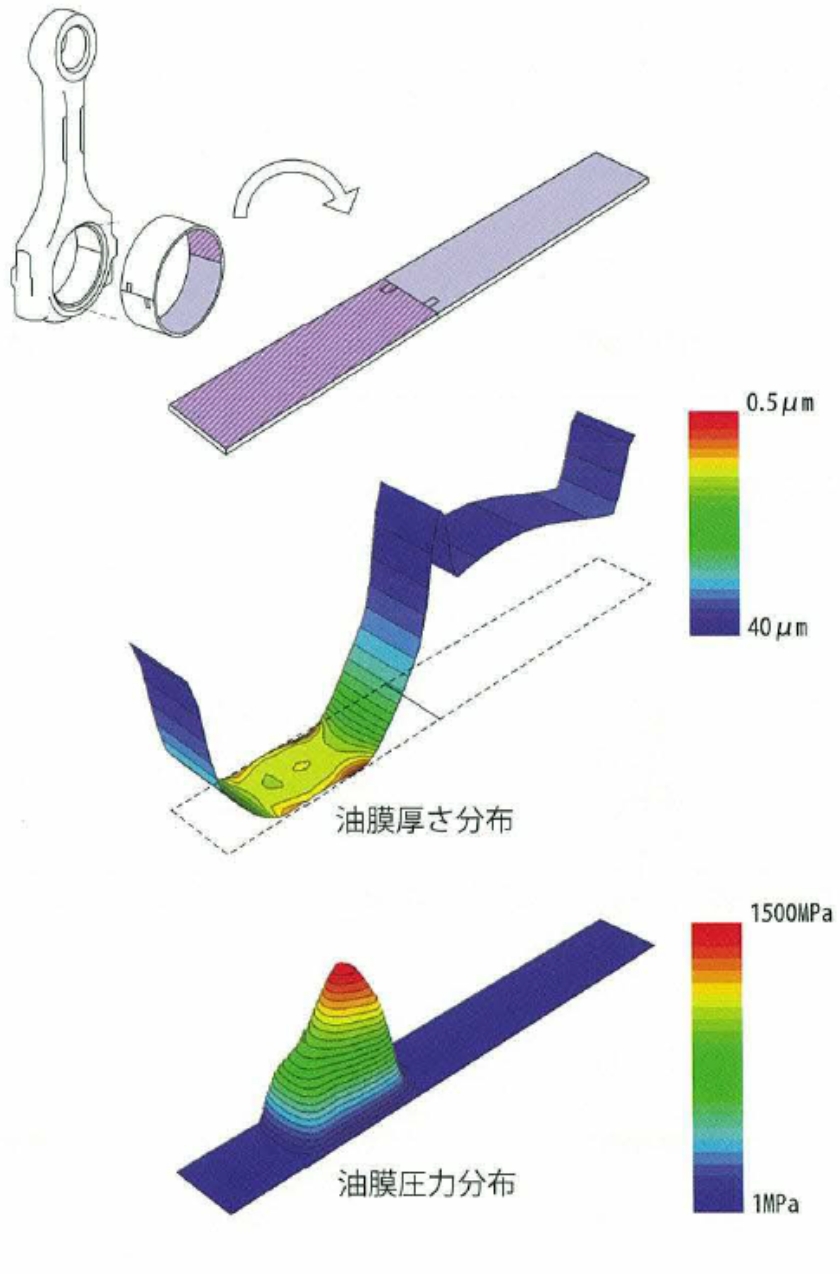
作動解析の実用例・・・軸受にかかる荷重
直列4気筒2000ccのガソリンエンジンと、ディーゼルエンジンの軸受固定座標の荷重極線図の例を示しました。 軸受に作用する荷重の大きさと方向を示しています。
ガソリンエンジン
Aが低速運転、Bが高速運転の状態を示します。低速の領域では爆発力の影響が大きく、高速では慣性力の影響を強く受けていることが分かります。
A. 低速運転状態(1000 rpm)
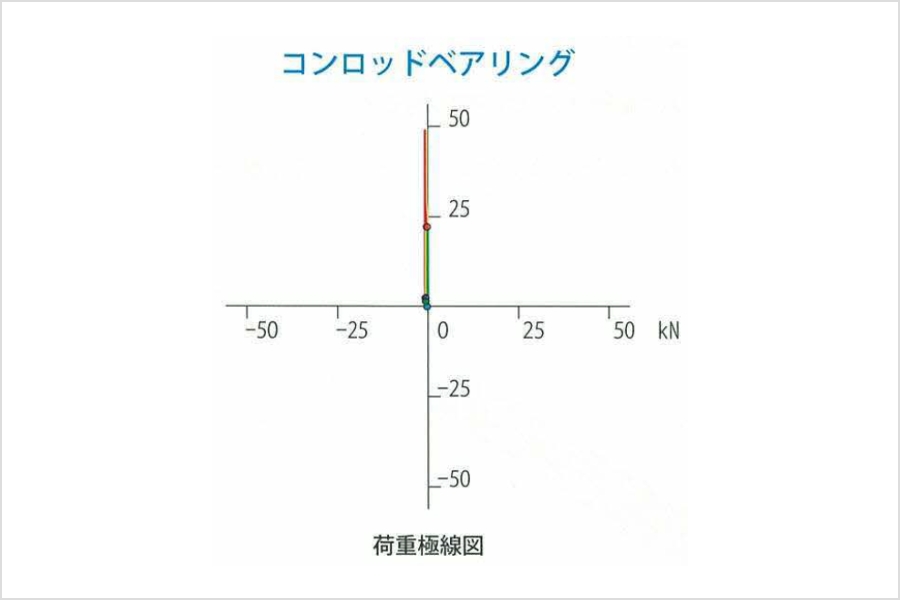

B. 高速運転状態(5600 rpm)
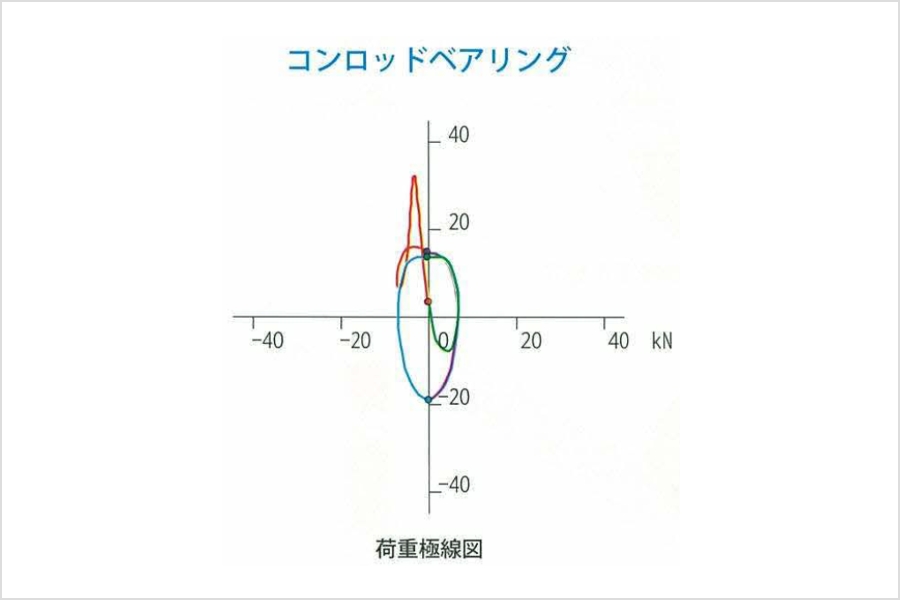
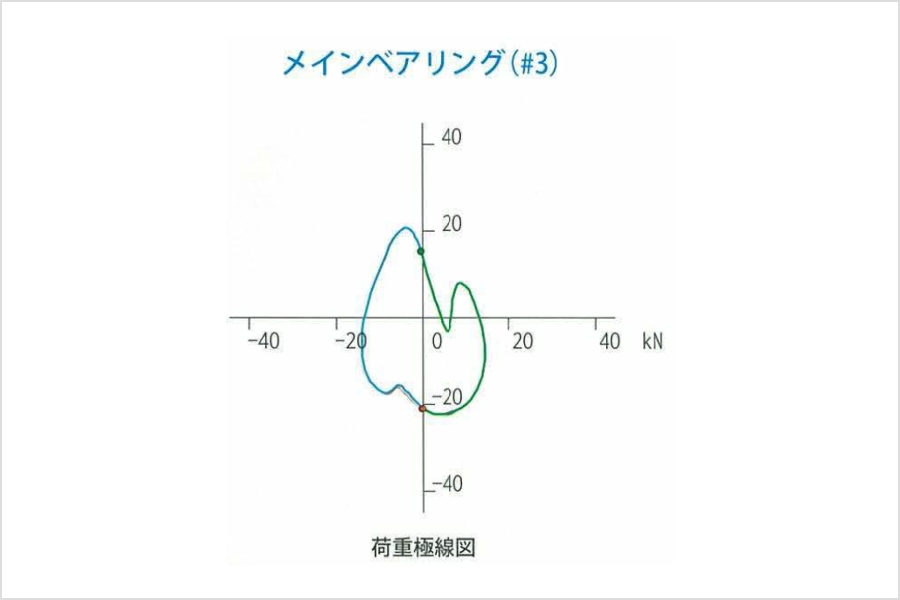
ディーゼルエンジン
ガソリンエンジンに比べ、爆発力の影響をさらに大きく受けていることが分かります。
A. 低速運転状態(1000 rpm)
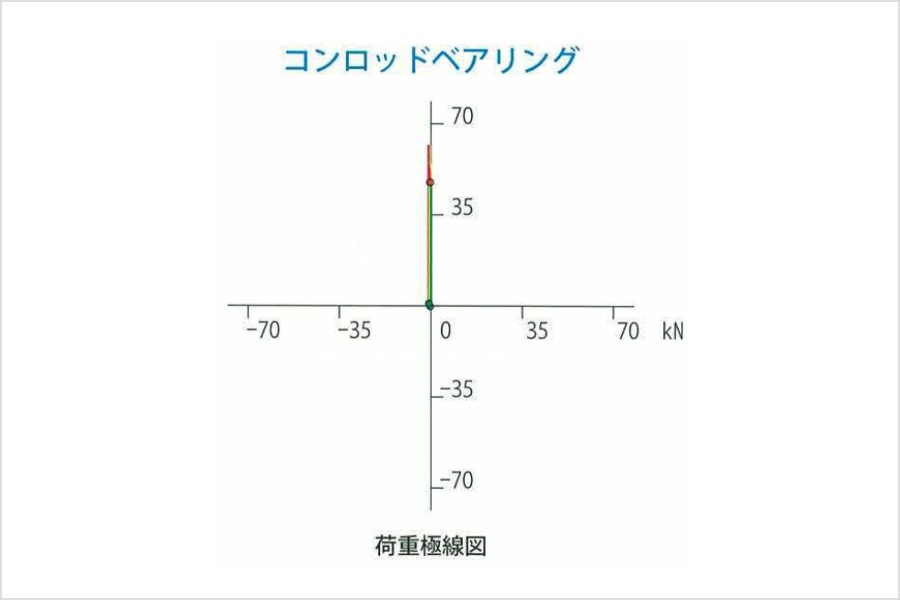
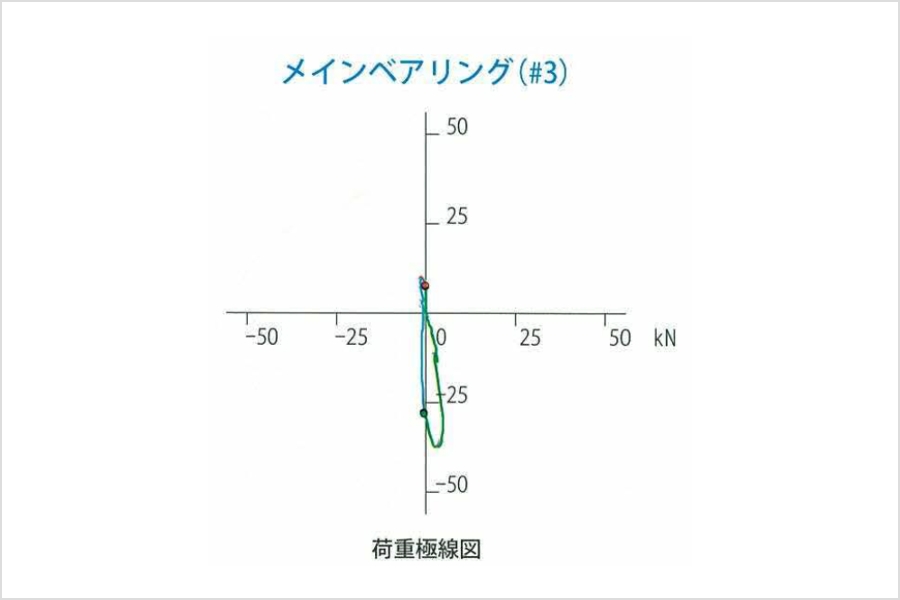
B. 高速運転状態(4000 rpm)
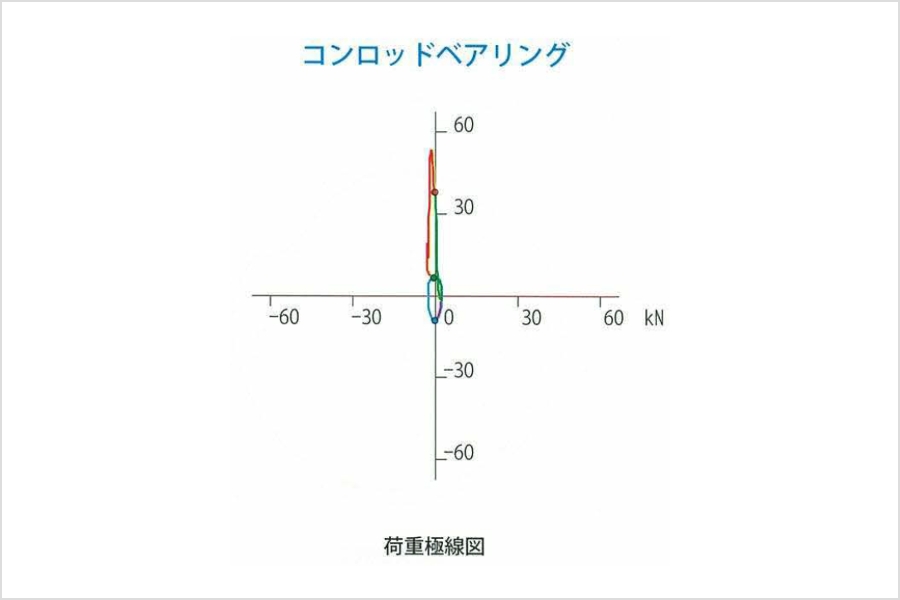
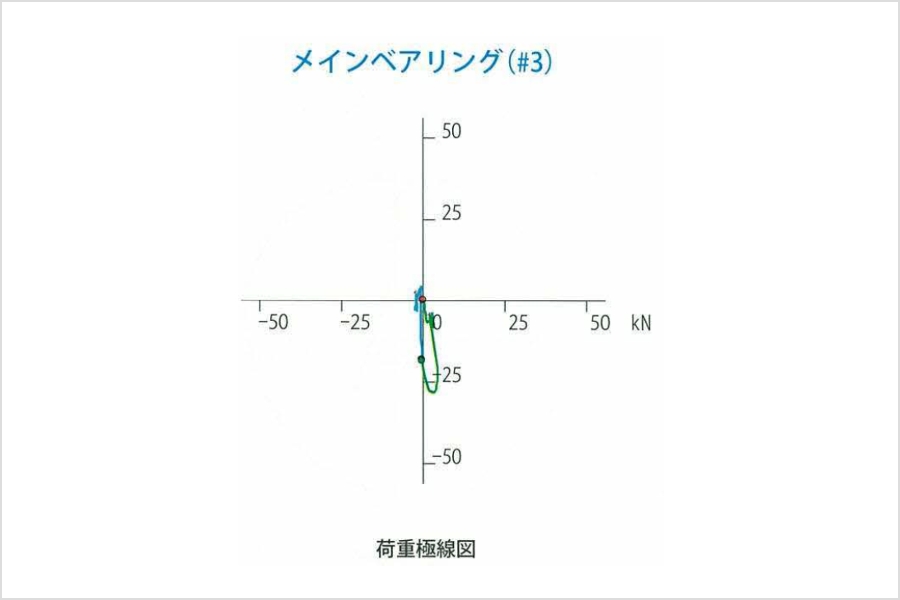

作動解析の実用例・・・軸受の油膜厚さ
直列4気筒2000ccのガソリンエンジンと、ディーゼルエンジンの1サイクルにおけるクランク軸心の軸心軌跡を軸受固定座標で示しています。軸受内での軸の動きを示しています。
ガソリンエンジン
Aが低速運転、Bが高速運転の状態を示します。軸受の中で軸がどう動くのかや、油膜厚さが分かります。代表として、コンロッドベアリングとメインベアリングと#3ジャーナルの例を示しています。
のところが最小油膜厚さの位置です。
A. 低速運転状態(1000 rpm)
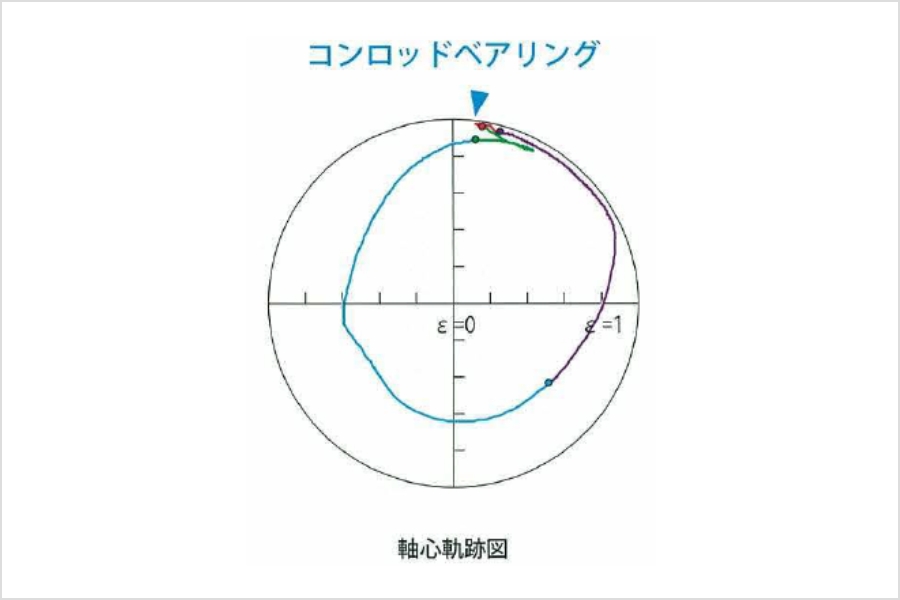
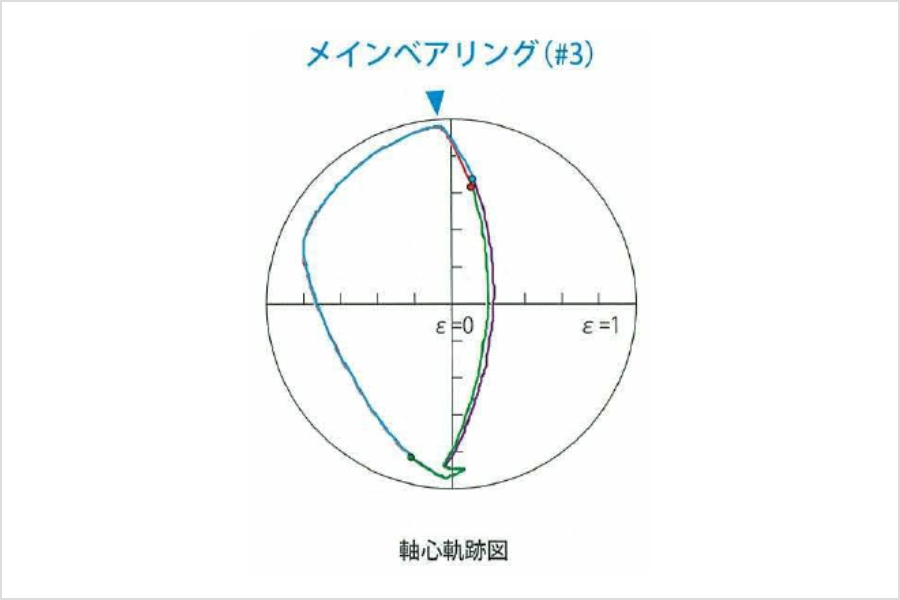
B. 高速運転状態(5600 rpm)
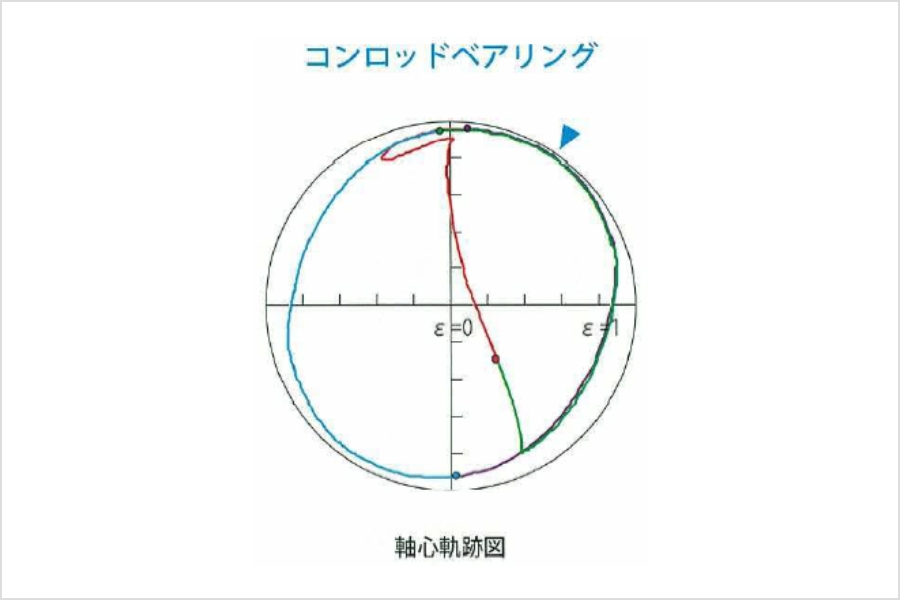
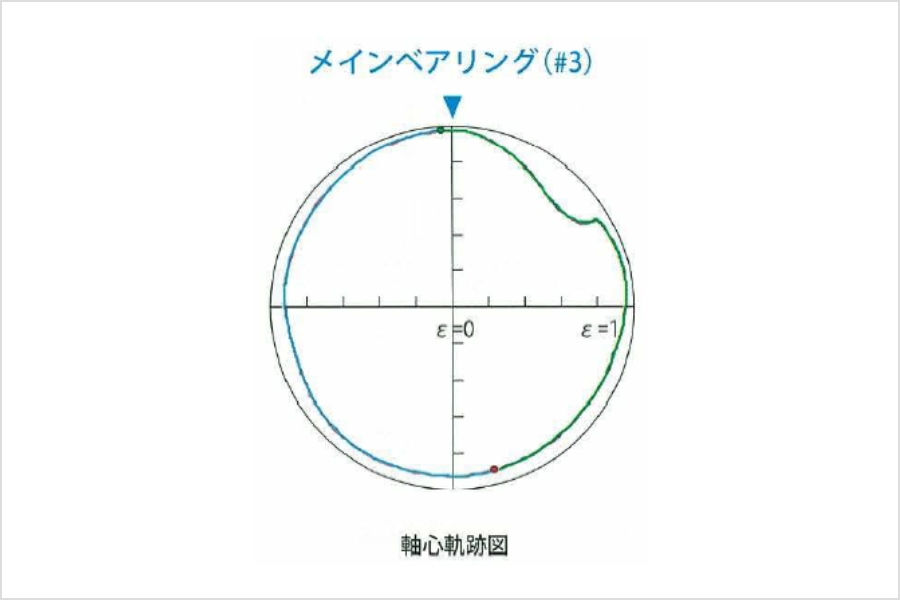
ディーゼルエンジン
ガソリンエンジンに比べ、メインベアリング(#3)の軸心軌跡では、爆発力による軸心の急激な動きがみられます。
A. 低速運転状態(1000 rpm)
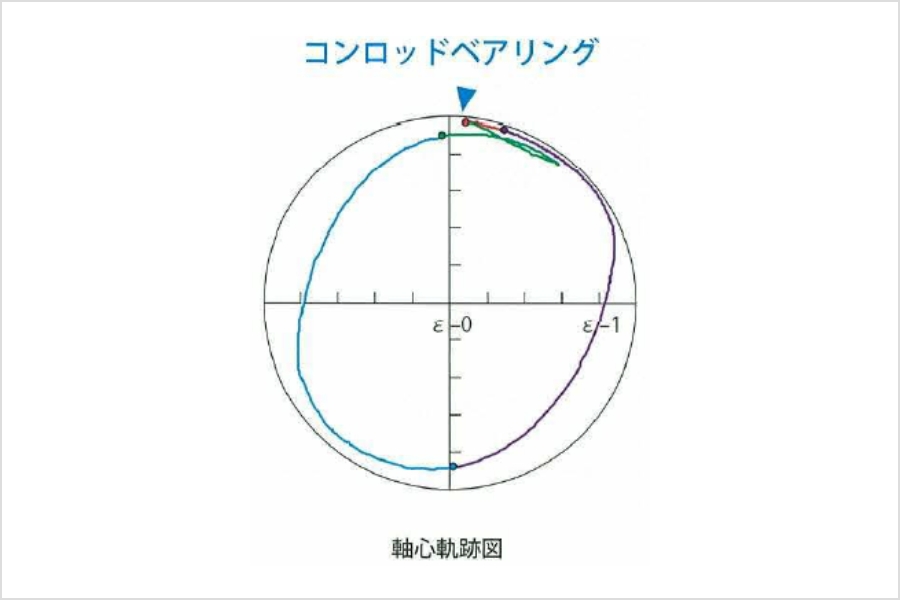
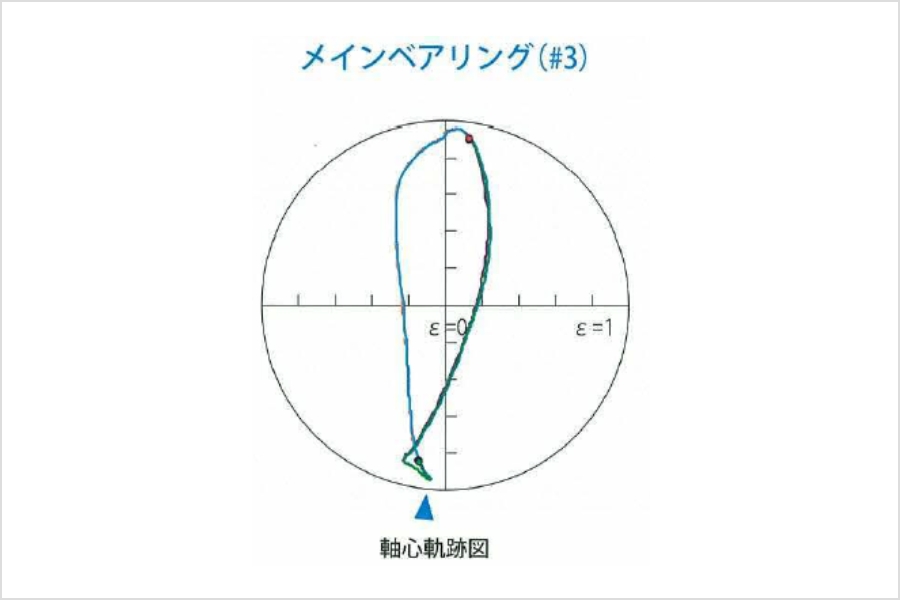
B. 高速運転状態(4000 rpm)
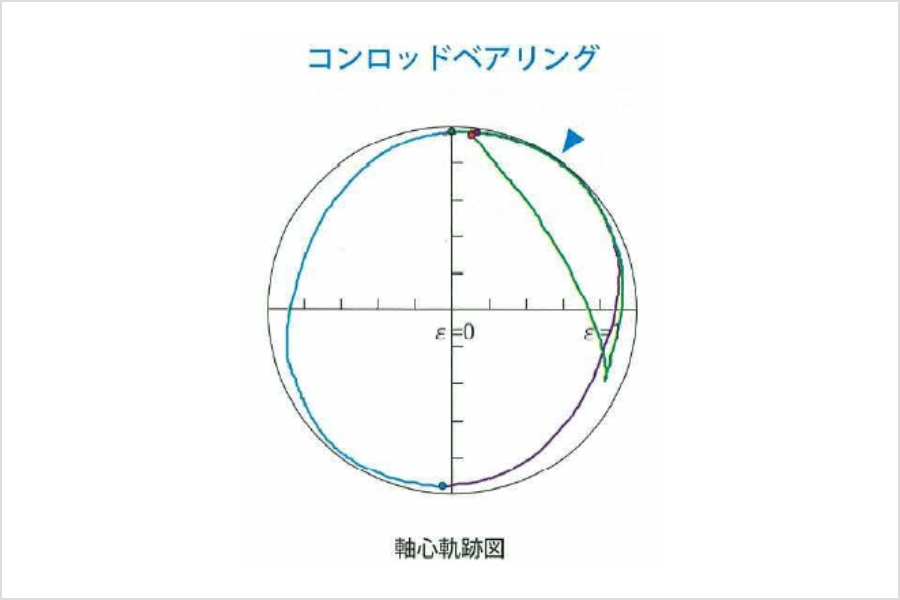
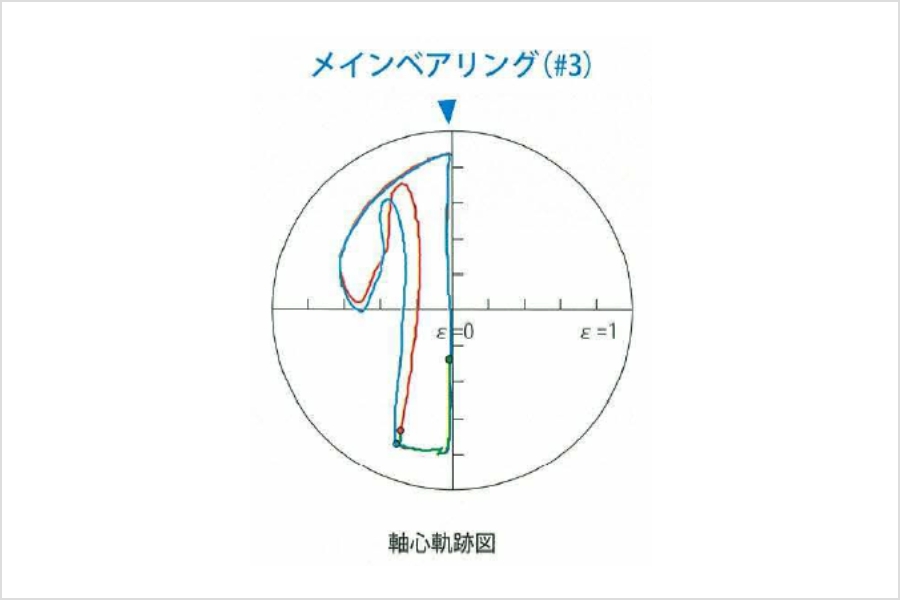


作動解析の応用例・・・クランクシャフトのバランス率が悪い事例
クランクシャフトのバランスが悪いときには、特に高速域でメインベアリングの特定な部位に非常に高い面圧がかかったり、さらには最小油膜厚さが極端に薄くなる事態を招くことがあります。
次に直列4気筒2000ccガソリンエンジンを例にとって、改善する手段の一例を紹介します。
メインベアリングの荷重極線図と最大面圧 6500rpm-1/2負荷
#3ベアリングの荷重が非常に高い
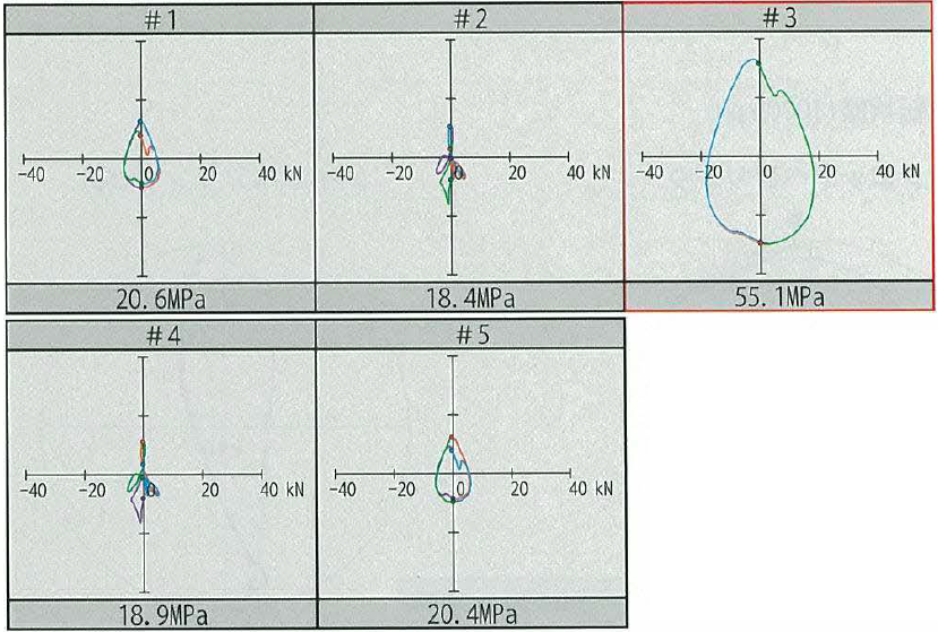

対応として軸受面圧の低減、あるいは最小油膜厚さを増加させるには、次のような事例があります。
軸受側 | エンジン側 | |||
---|---|---|---|---|
方法 | ねらい | 方法 | ねらい | |
|
|
|
|
|
|
|
(1)
#3ジャーナルベアリング有効幅を拡大したときの比較(計算値)
#3メインベアリングの面圧と最小油膜厚さ 600rpm-1/2負荷 M/N#3
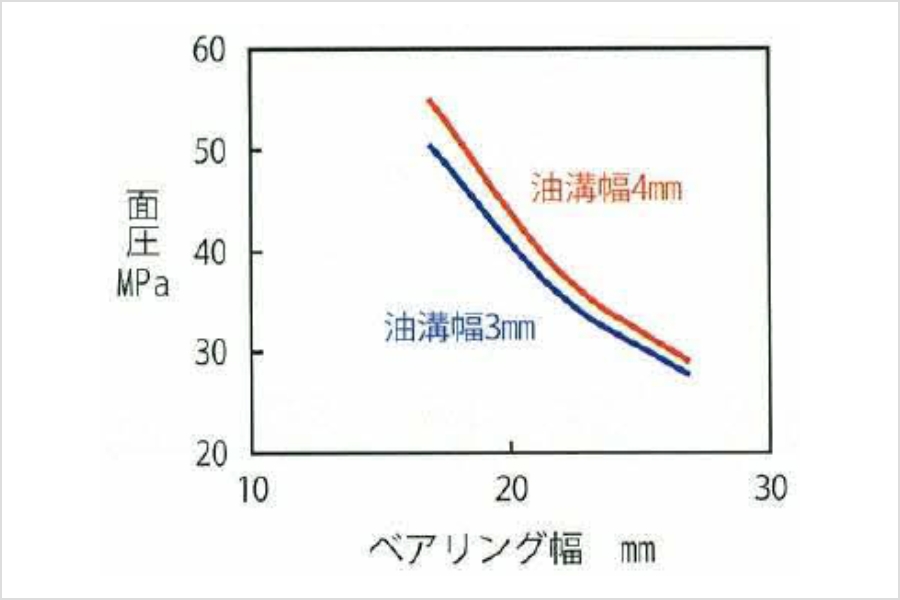
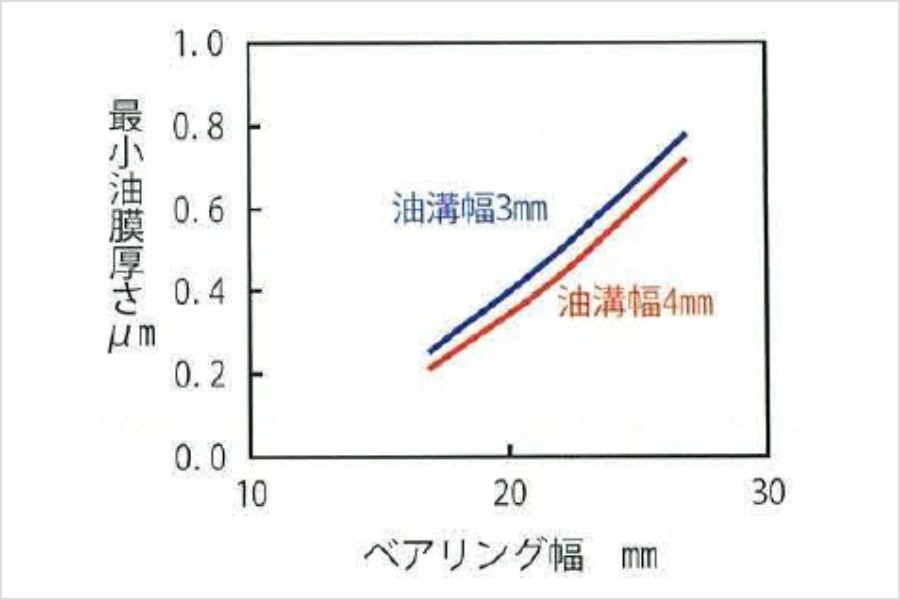
受圧面積を広げることによって、面圧低減、油膜厚さの増加を図ることができる
(2)
クランクシャフトのバランス率を変化させたときの比較(計算値)
メインベアリングの荷重曲線図と最大面圧 6500rpm-1/2負荷
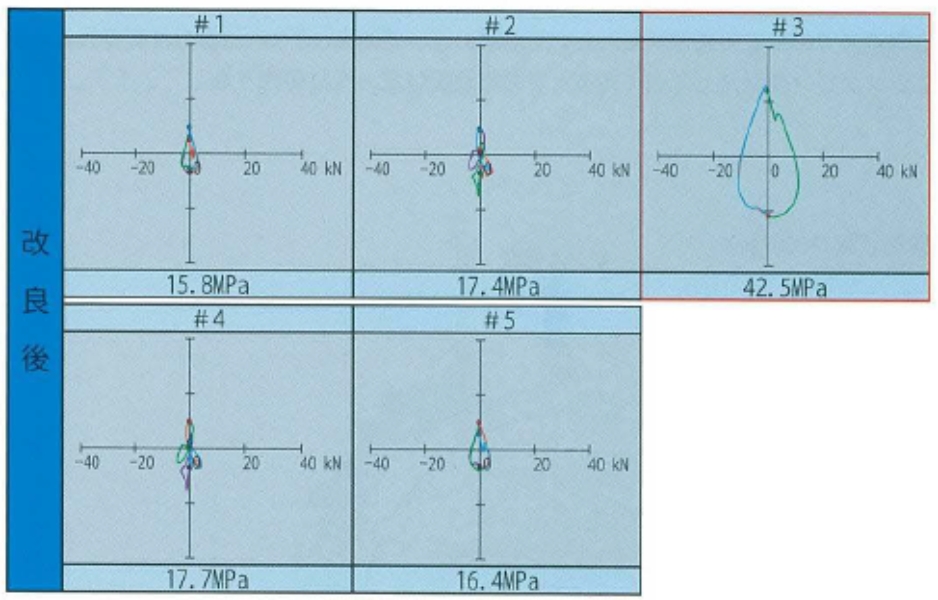

#3ベアリングの荷重とともに全体の荷重も小さくなっている
バランス率 57%改良
#3ベアリングの負荷低減比較
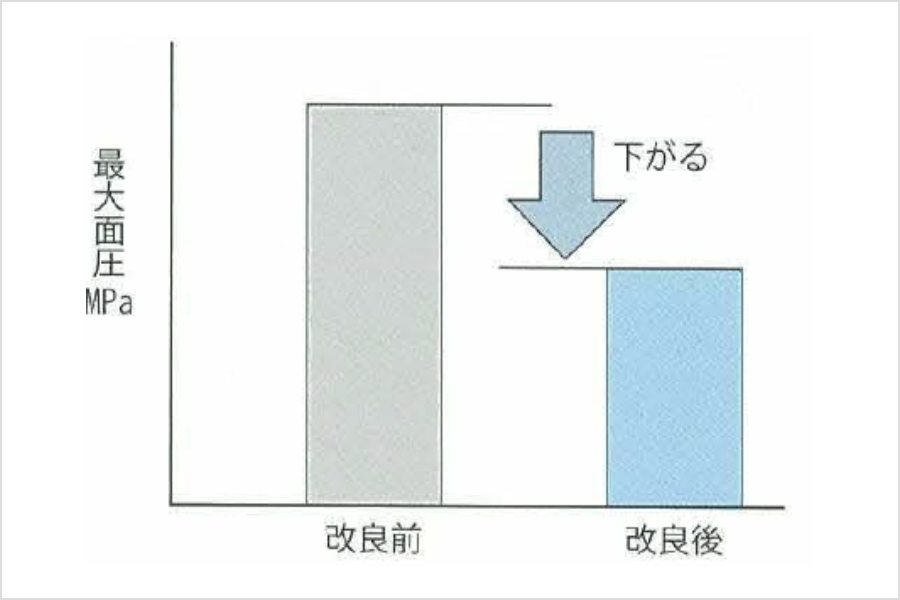
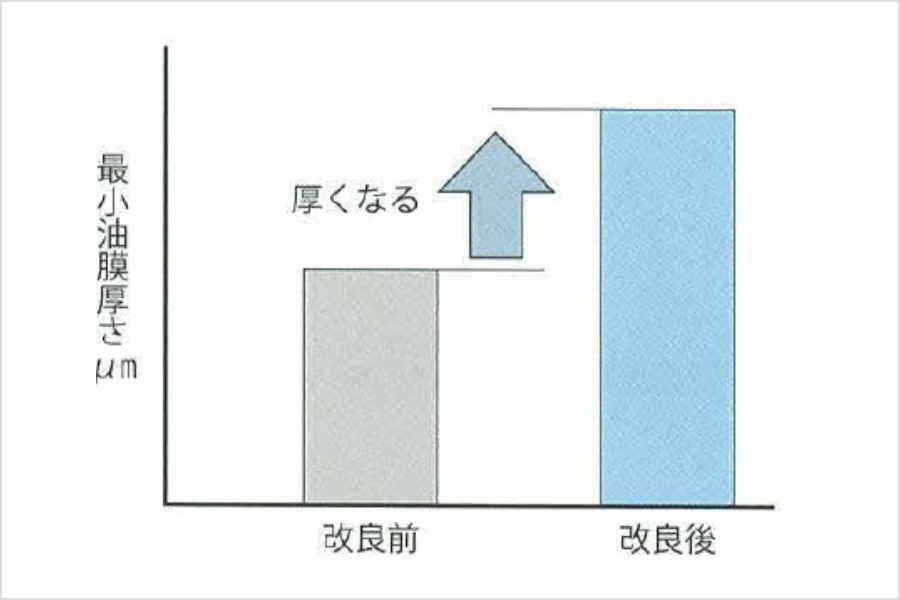
作動解析の応用例・・・クランクシャフトピン部の給油穴位置
コンロッドベアリングへの給油量を増やすため、クランクシャフトにあける油穴は、最適な位置を選ぶことが重要です。
給油穴の位置は油膜の厚いところ(油膜圧力の低いところ)に設定します。油膜の厚さや圧力の分布は軸固定の軸心軌跡図やエクステントマップから知ることができます。
(1)
軸心軌跡図・・・軸固定座標の軸心変化
低速から高速までのすべての運転状態において油膜の厚い範囲を、給油穴位置の推奨範囲とします。
下図はクランクピンが爆発上死点にあるときの給油圧位置の推奨範囲を表しています。
a.低速運転状態(1000rpm)
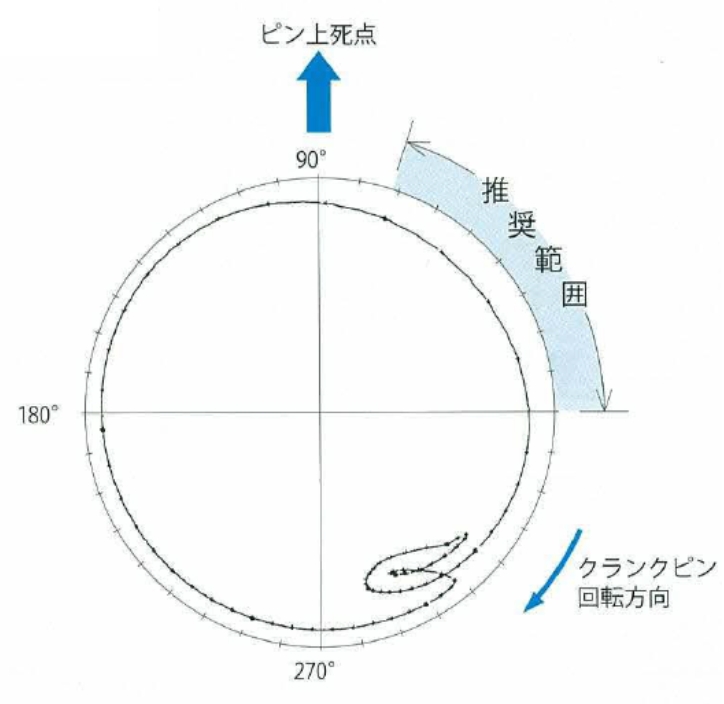
b.高速運転状態(6000rpm)
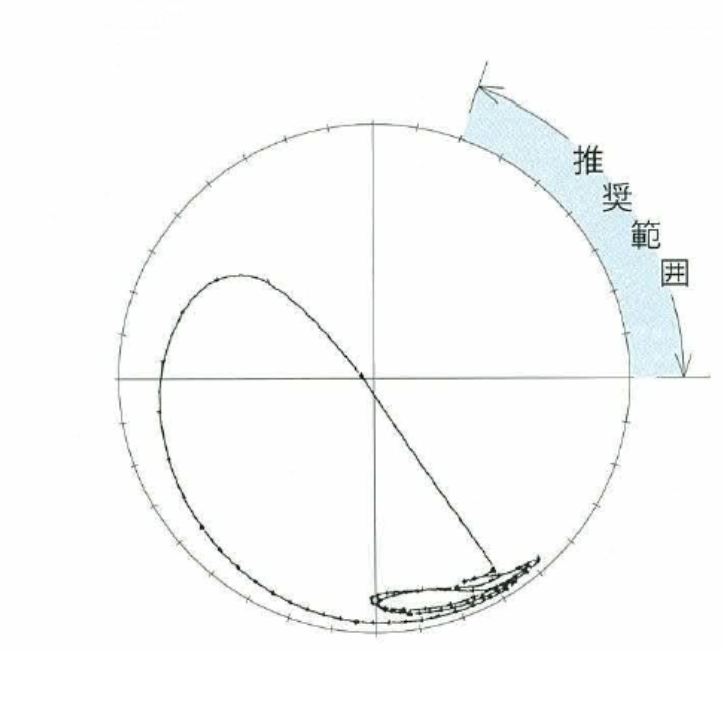
(2)
エクステントマップ・・・油膜圧力分布
下図は、エンジン回転の1サイクル(2回転、720°)でのコンロッドベアリングの幅方向中央部での円周方向油膜圧力分布を示したエクステントマップです。
エクステントマップで油膜圧力の低いところを給油穴の軌跡が通過するようにクランクピンの給油穴位置を設定します。
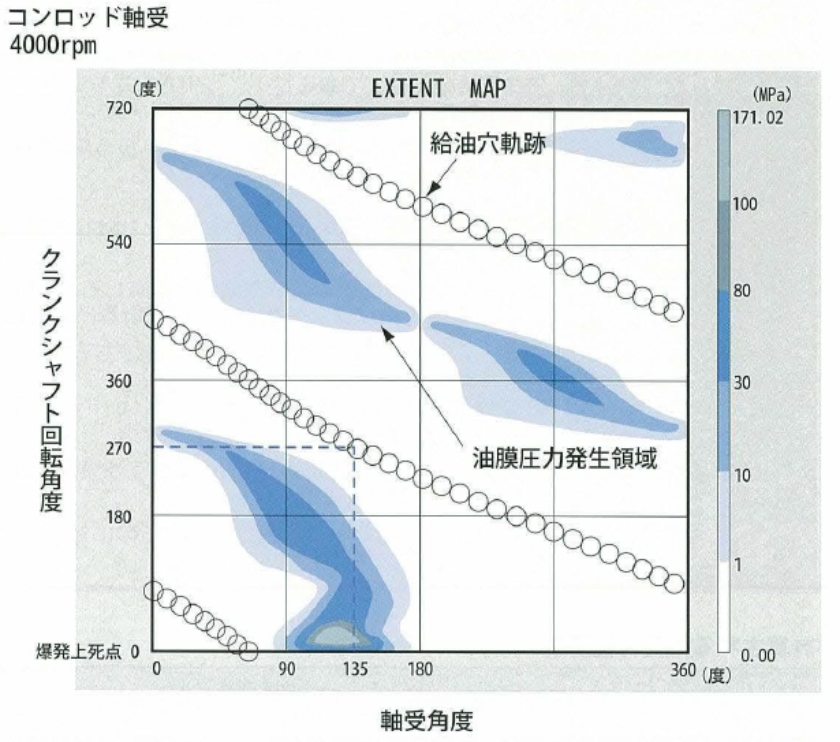
下図は上記エクステントマップにおける、クランクシャフト回転角度270°のときのクランクピン給油穴位置と軸受角度との位置関係を表しています。
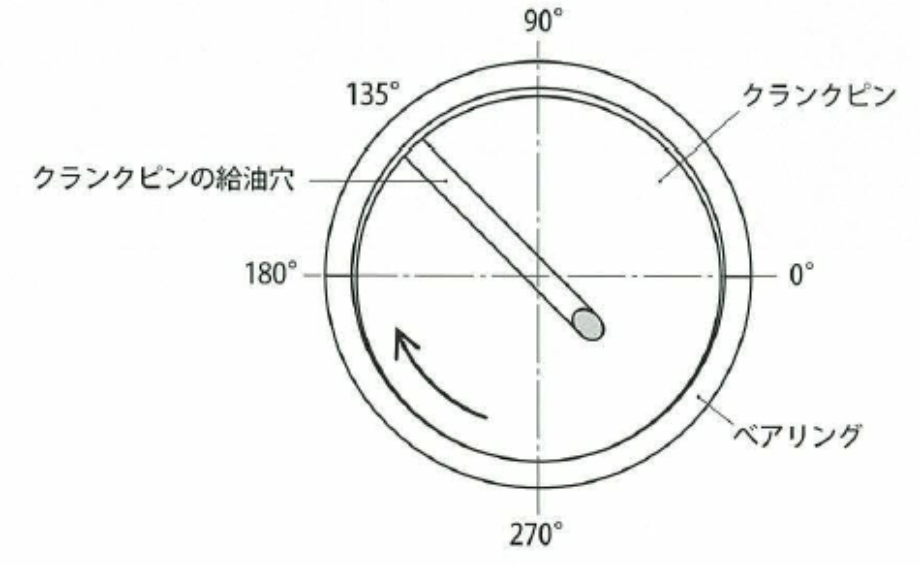
設計診断のための計算解析
軸受の使用条件の解析のために、以下のような解析ツールを開発しております。
計算解析ツール
HL |
流体潤滑理論(Hydrodynamic Lubrication Theory)を基にした計算手法。 流体潤滑の木組織であるレイノズル方程式をエンジン軸受に適用し計算することにより、軸受特性を予測する。 軸と軸受、ハウジング剛体として取り扱う簡便な計算であることから、一般的に広く用いられている。 |
---|---|
EHL |
弾性流体潤滑理論(Elasto-Hydrodynamic Lubrication Theory)を基にした計算手法。 エンジン軸受の使用環境の苛酷化に対応して、油膜圧力による(主に軸受とハウジングの)弾性変形を計算に考慮したもの。 これにより詳細な軸受特性の予測が可能である。 |
TEHL |
熱弾性流体潤滑理論(Thermo-Elasto-Hydrodynamic Lubrication Theory)を基にした計算手法。 潤滑油膜内の発熱、熱伝導、熱伝達に伴う油膜内の温度分布、年度分布を考慮した計算。 従来、潤滑油膜は等粘度と仮定しているのに対して、3次元に分布する粘度にて軸受特性を計算する。 |
計算される軸受特性要素
計算解析 ツール |
軸受特性要素 | ||||||
---|---|---|---|---|---|---|---|
軸心 軌跡 |
油膜 厚さ |
油膜 圧力 |
変形量 | 軸受 油量 |
油膜 温度 |
軸受 温度 |
|
HL |
〇 | 〇 | 〇 | 〇 | |||
EHL |
◎ | ◎ | ◎ | ◎ | ◎ | ||
TEHL |
◎ | ◎ | ◎ | ◎ | ◎ | ◎ | ◎ |
〇:計算予測可能 ◎:より詳細に予測可能